In workplaces worldwide, chemicals are integral to various processes and operations. Chemicals are crucial in many industries, from manufacturing and healthcare to laboratories and construction sites.
While these substances are essential, they also pose inherent risks to the health and safety of workers. This is where the concept of chemical safety in the workplace comes into play.
Chemical safety includes the practices, procedures, and policies put in place to ensure that the handling, storage, use, and disposal of chemicals are done in a manner that minimizes risks to human health, property, and the environment.
It's about preventing accidents, injuries, illnesses, and environmental harm from exposure to hazardous chemicals.
Chemical safety protects employees' health and well-being and safeguards the surrounding community and the environment.
Chemical accidents can lead to severe injuries, long-term health issues, property damage, and even fatalities. Moreover, the mishandling of chemicals can have far-reaching ecological consequences.
This article will explore the topic of chemical safety in the workplace. We aim to provide valuable insights and practical guidance to employers, employees, and safety professionals, helping them create and maintain safe workplaces where the risks associated with chemicals are effectively managed!
Types of Chemicals Found in the Workplace
When it comes to chemical safety within the workplace, it's imperative to comprehend the diverse range of chemicals encountered daily.
These substances can pose huge risks, from minor irritations to severe health threats and environmental hazards.
Therefore, understanding these chemicals' nature and potential dangers is foundational to any effective chemical safety program.
1. Hazardous Chemicals

Hazardous chemicals constitute a significant category among workplace substances. These are compounds that, due to their intrinsic properties, can inflict harm on human health, property, or the environment.
They encompass a broad spectrum, including corrosive materials, flammable substances, carcinogens, and toxic compounds.
Identifying, labeling, and handling these chemicals appropriately is paramount to mitigate risks and safeguard the well-being of employees and the workplace environment.
2. Common Chemicals in Various Industries
Chemical use is pervasive across industries, from manufacturing and construction to healthcare and laboratories. Each sector employs specific chemicals tailored to its processes and applications.
Understanding the common chemicals pertinent to each industry is crucial for implementing targeted safety measures. For instance, the chemicals utilized in a healthcare setting might differ significantly from those in an automotive assembly plant.
Recognizing these distinctions allows for tailored safety protocols, minimizing risks and ensuring compliance with industry-specific regulations.
Chemical Safety Practices
Chemical safety practices form the bedrock of a secure work environment when dealing with hazardous substances. These practices encompass a multifaceted approach to protecting the workplace and environment from the potential risks of chemical exposure.
1. Chemical Inventory and Labeling
.png)
Maintaining an accurate chemical inventory is the first step in chemical safety. It involves creating a comprehensive list of all chemicals used or stored in the workplace.
Each chemical container must be labeled appropriately, providing essential information such as the chemical's name, hazard warnings, and handling instructions.
This practice ensures that employees can quickly identify and understand the potential risks associated with each chemical they encounter.
2. Safety Data Sheets (SDS)
.png)
Safety Data Sheets, or SDS, are crucial documents that provide detailed information about each chemical's properties, hazards, and safe handling procedures.
It is typically organized into sections, including product identification, hazard identification, composition, and first-aid measures. Access to up-to-date SDSs is essential for employees to understand how to work safely with chemicals and respond to emergencies effectively.
3. Hazard Communication

Effective communication of chemical hazards is vital to chemical safety. This practice involves using labels, signs, and other forms of communication to convey information about chemical hazards to employees.
It also includes training employees to recognize and respond to these hazards - hazard recognition training can be helpful in this regard.
Clear and consistent hazard communication ensures that workers know the risks associated with the chemicals they handle.
4. Personal Protective Equipment (PPE)

Personal Protective Equipment, or PPE, is a last defense against chemical exposure. This includes gloves, goggles, respirators, and protective clothing. The selection, use, and maintenance of PPE are critical aspects of chemical safety.
Employees must complete PPE training to understand the proper use of PPE and be provided with the necessary equipment to protect themselves when working with hazardous chemicals.
5. Proper Storage and Handling

Safely storing and handling chemicals are essential to prevent accidents and chemical spills. Chemicals should be stored in designated areas, away from incompatible substances, heat sources, and direct sunlight.
Proper handling procedures, such as using appropriate containers and equipment, reduce the risk of spills and exposures.
7. Ventilation and Engineering Controls
Ventilation systems and engineering controls are designed to minimize chemical exposure in the workplace. Local exhaust ventilation, for example, can capture and remove airborne contaminants, while automated processes can reduce manual handling of chemicals.
These controls are essential for maintaining air quality and reducing the risk of chemical inhalation or skin contact.
6. Employee Training and Education
The most critical aspect of chemical safety is ensuring that employees are well-informed and trained in safe practices. Training programs should cover chemical hazards, safe handling procedures, emergency response protocols, and the use of protective equipment.
Canada Safety Training offers valuable training for workers belonging to different industries. Some of the training are listed as follows:
- Bloodborne Pathogen Certification
- WHMIS Online Certification
- Benzene Awareness Program
Regular education and refresher training inform employees of the latest safety procedures and best practices.
Types of Chemicals Hazards
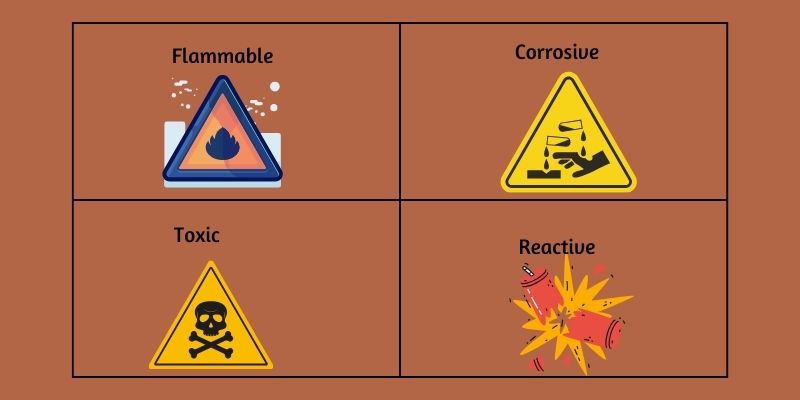
Chemical hazards in the workplace can pose significant risks to employee health and safety. Understanding the different types of chemical hazards is essential for implementing effective safety measures.
The following are the main types:
- Flammable
- Corrosive
- Toxic
- Reactive
Each type requires specific precautions and controls to ensure a safe working environment, so let's discuss them individually.
1. Flammable
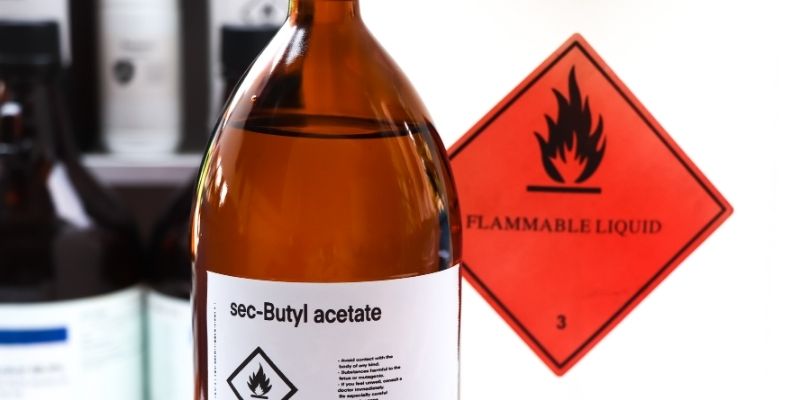
Flammable chemicals can easily ignite and burn when exposed to an ignition source, such as heat, sparks, or open flames.
These chemicals can be found in various forms, including liquids, gases, and solids, and are commonly used in many industries, including manufacturing, construction, and healthcare.
Characteristics and Risks
Flammable chemicals are characterized by their ability to vaporize and mix with air to form explosive mixtures.
The lower the flash point (the lowest temperature at which a chemical can vaporize to form an ignitable mixture in air), the more flammable the substance.
Examples of flammable chemicals include gasoline, ethanol, acetone, and propane.
The primary risk associated with flammable chemicals is fire and explosion. An uncontrolled fire can cause severe injuries, fatalities, and extensive property damage.
Additionally, the release of flammable vapors can lead to suffocation or poisoning if inhaled in high concentrations.
2. Corrosive
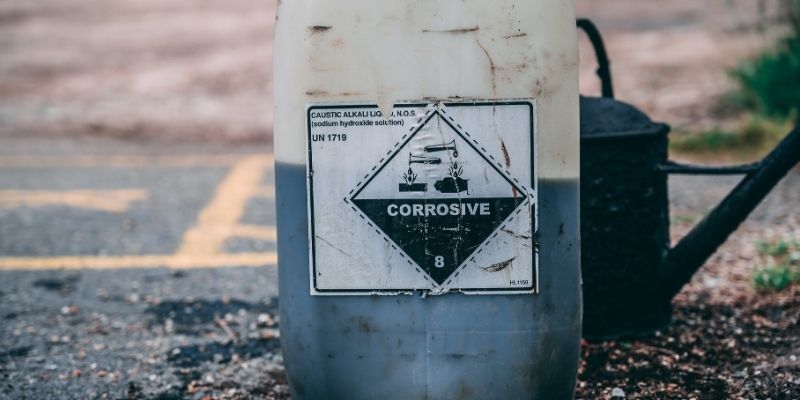
Corrosive chemicals can cause severe damage to living tissues, metals, and other materials by chemical action.
These chemicals can be acidic or basic (alkaline) and are commonly used in industrial processes, laboratory settings, and cleaning operations.
Characteristics and Risks
Corrosive chemicals can cause immediate and severe damage upon contact with the skin, eyes, respiratory system, or digestive system.
They can also corrode and degrade materials such as metals, leading to structural failures and equipment damage.
Common corrosive chemicals include sulfuric acid, hydrochloric acid, sodium hydroxide, and ammonia.
The primary risk associated with corrosive chemicals is their ability to cause chemical burns, tissue damage, and respiratory distress.
Inhalation of corrosive vapors can lead to severe respiratory tract irritation and damage. Eye contact can result in blindness, while ingestion can cause internal burns and organ damage.
3. Toxic
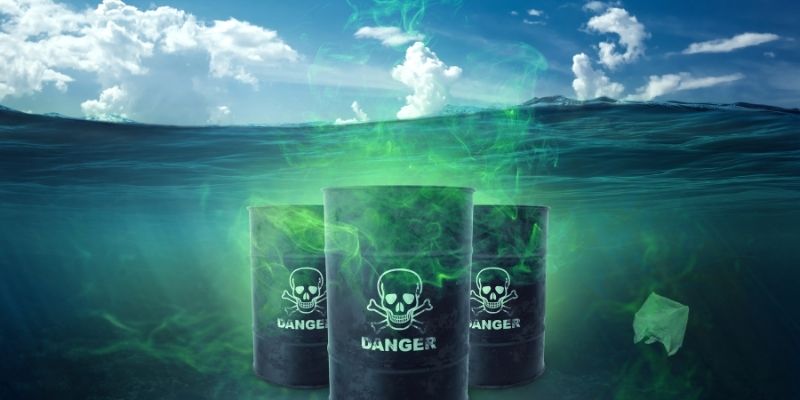
Toxic chemicals can harm living organisms through exposure, including inhalation, ingestion, or skin contact.
They pose significant health risks and can lead to acute or chronic health effects depending on the level and duration of exposure.
Toxic chemicals are prevalent in many industrial, agricultural, and laboratory environments.
Characteristics and Risks
Toxic chemicals can range from mild irritants to highly poisonous substances. They can affect various organs and systems in the body, leading to symptoms such as headaches, dizziness, nausea, respiratory distress, neurological damage, and even death.
Pesticides, heavy metals (like lead and mercury), solvents, and certain pharmaceuticals are typical examples of toxic chemicals.
The primary risk associated with toxic chemicals is their potential to cause immediate or delayed health effects.
Acute exposure can result in immediate symptoms and severe health consequences.
In contrast, chronic exposure, even at low levels, can lead to long-term health problems such as cancer, reproductive issues, and organ damage.
4. Reactive
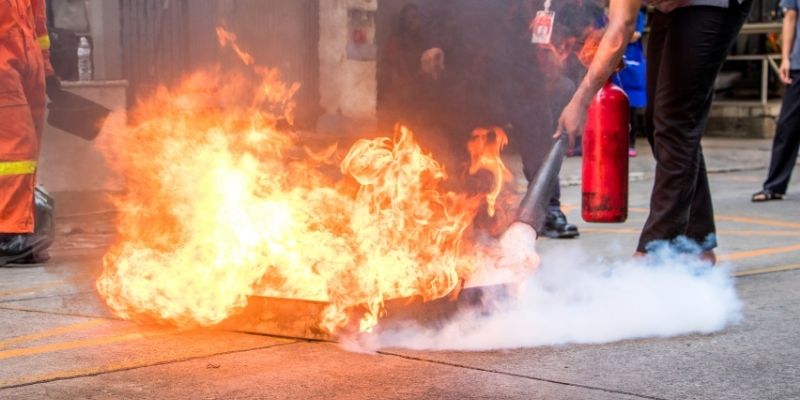
Reactive chemicals can undergo rapid and violent reactions when exposed to heat, light, water, or other chemicals.
These reactions can produce harmful byproducts, release energy in the form of heat or pressure, and pose significant hazards to health and safety.
Reactive chemicals are commonly found in various industrial and laboratory settings.
Characteristics and Risks
Reactive chemicals are characterized by their instability and tendency to react with other substances or environmental conditions.
These reactions can lead to explosions, fires, the release of toxic gases, and forming dangerous compounds.
Common examples of reactive chemicals include sodium metal, peroxides, cyanides, and ammonium nitrate.
The primary risk of reactive chemicals is their potential to cause sudden and catastrophic incidents. Uncontrolled reactions can result in severe injuries, fatalities, property damage, and environmental contamination.
Reactivity can be influenced by temperature, pressure, moisture, and the presence of catalysts or other chemicals.
Routes of Exposure
Chemical hazards can affect workers through various routes of exposure, each presenting unique risks and requiring specific safety measures to mitigate harm.
The primary routes of exposure include inhalation, skin contact, ingestion, and injection.
Inhalation
Inhalation is one of the most common routes of exposure to hazardous chemicals. When toxic substances are airborne as gases, vapors, dust, or aerosols, they can be breathed in and enter the respiratory system.
Inhalation can lead to immediate effects such as irritation of the eyes, nose, and throat, as well as more severe health issues like lung damage, respiratory diseases, and systemic toxicity.
Risks:
- Respiratory Irritation: Short-term exposure to irritant gases or vapors can cause coughing, shortness of breath, and respiratory tract irritation.
- Chronic Health Effects: Long-term exposure to certain chemicals, such as asbestos or silica dust, can lead to chronic respiratory diseases like asbestosis or silicosis.
- Systemic Toxicity: Some chemicals can enter the bloodstream through the lungs and affect other organs, leading to systemic health effects.
Control Measures:
- Ventilation: Ensure proper ventilation in work areas to reduce the concentration of airborne hazardous substances.
- Respiratory Protection: Use appropriate respiratory protective equipment (RPE), such as masks or respirators, when working with or around airborne chemicals.
- Monitoring: Regularly monitor air quality to detect the presence of hazardous chemicals and ensure that levels remain within safe limits.
Skin Contact
Skin contact is another significant route of exposure, especially for chemicals that are corrosive, irritant, or capable of being absorbed through the skin.
Chemicals can cause local effects such as burns, rashes, and dermatitis or be absorbed into the bloodstream, leading to systemic toxicity.
Risks
- Local Effects: Corrosive chemicals can cause severe burns and tissue damage on contact. Irritants can lead to rashes and dermatitis.
- Systemic Absorption: Chemicals that can penetrate the skin, such as certain solvents, pesticides, and pharmaceuticals, can enter the bloodstream and affect internal organs.
Control Measures
- Personal Protective Equipment (PPE): Wear appropriate PPE such as gloves, protective clothing, and face shields to prevent skin contact with hazardous chemicals.
- Hygiene Practices: Implement good hygiene practices, such as thoroughly washing hands and exposed skin after handling chemicals.
- Barrier Creams: Use barrier creams to provide additional protection against skin absorption.
Ingestion
Hazardous chemical ingestion can occur if workers inadvertently consume food or drink contaminated with chemicals or fail to wash their hands before eating or smoking.
Ingested chemicals can cause gastrointestinal irritation, systemic toxicity, and other health effects.
Risks
- Gastrointestinal Irritation: Ingesting corrosive or irritant chemicals can cause burns, pain, and damage to the mouth, throat, esophagus, and stomach.
- Systemic Toxicity: Once ingested, chemicals can be absorbed into the bloodstream and affect internal organs, leading to systemic health effects.
Control Measures
- Hygiene Practices: Ensure workers wash their hands thoroughly before eating, drinking, or smoking. Prohibit food and drink consumption in areas where chemicals are used or stored.
- Safe Storage: Store chemicals properly to prevent accidental contamination of food and beverages.
Injection
Injection is a less common but potentially severe route of exposure to hazardous chemicals.
Injection can occur through accidental punctures by contaminated needles, sharp objects, or high-pressure equipment that injects chemicals into the skin.
This route can lead to localized injury and systemic exposure if the chemical enters the bloodstream.
Risks
- Local Injury: Chemical injections can cause immediate pain, swelling, and tissue damage at the entry site.
- Systemic Toxicity: If the chemical enters the bloodstream, it can be transported to other body parts, leading to systemic health effects.
Control Measures
- Needle Safety: Use safety-engineered needles and sharps disposal containers to reduce the risk of accidental punctures.
- Proper Equipment Handling: Train workers to safely handle and maintain high-pressure equipment to prevent accidental injection injuries.
- First Aid: Ensure that first aid procedures are in place to address accidental injections promptly and effectively.
Understanding the various routes of exposure and implementing appropriate control measures is crucial for protecting workers from chemical hazards in the workplace. By addressing these risks proactively, employers can create a safer and healthier work environment.
Regulatory Standards and Compliance
Canadian regulatory standards and compliance are crucial for ensuring workplace safety, particularly in managing chemical hazards.
Adherence to these regulations helps protect workers, avoid legal repercussions, and promote a safe working environment.
Let’s explore critical Canadian regulatory bodies, relevant standards, their importance, and steps organizations can take to achieve compliance.
Key Regulatory Bodies and Standards
Canadian Centre for Occupational Health and Safety (CCOHS)
Workplace Hazardous Materials Information System (WHMIS): WHMIS is Canada's national standard for hazard communication. It ensures workers receive information about hazardous products through labels, pictograms, Safety Data Sheets (SDS), and employee training. WHMIS is aligned with the Globally Harmonized System of Classification and Labelling of Chemicals (GHS), ensuring consistency and clarity in hazard communication.
Provincial and Territorial Regulations
Each province and territory in Canada has its own occupational health and safety legislation that complements federal regulations.
These regulations may include specific requirements for managing hazardous substances, safety training, and workplace inspections. Employers must know and comply with these local regulations and federal standards.
Environmental Protection Regulations
Canadian Environmental Protection Act (CEPA): CEPA provides a framework for protecting the environment and human health from risks posed by chemicals and pollutants. It includes provisions for assessing and managing toxic substances, pollution prevention, and environmental emergencies.
Transportation of Dangerous Goods (TDG) Regulations
TDG regulations govern the transportation of hazardous materials by road, rail, air, and marine modes.
These regulations aim to ensure the safe and secure transportation of dangerous goods and prevent accidents and incidents during transit.
Significance of Compliance
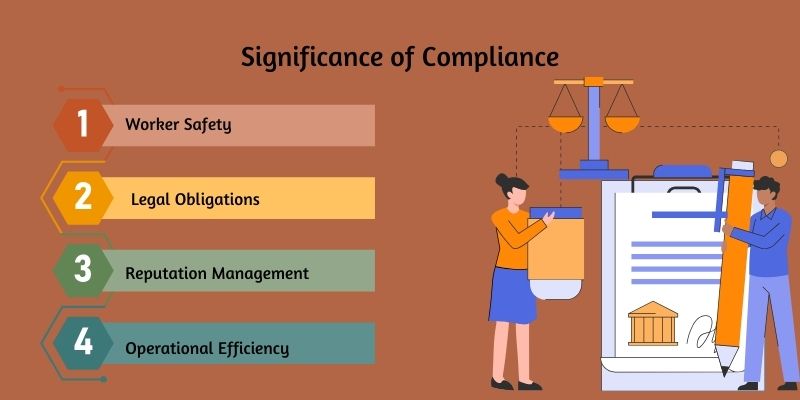
Compliance with regulatory standards is essential for several reasons:
- Worker Safety: Adhering to regulations helps protect workers from exposure to hazardous chemicals, reducing the risk of accidents, injuries, and illnesses.
- Legal Obligations: Failure to comply with regulations can result in legal penalties, fines, and sanctions from regulatory bodies.
- Reputation Management: Maintaining compliance demonstrates a commitment to safety and can enhance the organization's reputation among employees, customers, and the public.
- Operational Efficiency: Effective chemical management can prevent disruptions, minimize waste, and improve operational efficiency.
Steps to Achieve Compliance
Understanding Regulations: Organizations must stay informed about relevant federal, provincial, and territorial regulations and standards.
This includes industry-specific requirements and updates to existing regulations.
- Risk Assessment and Management: Conduct thorough risk assessments to identify chemical hazards and implement appropriate control measures. This includes regular monitoring and evaluation of chemical processes and storage.
- TDG Training: Provide comprehensive TDG training on chemical hazards, safe handling procedures, and emergency response. Ensure that employees understand their roles and responsibilities in maintaining safety.
- Documentation and Record-Keeping: Maintain accurate records of chemical inventories, safety data sheets, training logs, and incident reports. Proper documentation is crucial for demonstrating compliance during inspections and audits.
- Safety Data Sheets (SDSs): Ensure that SDSs for all hazardous chemicals are readily accessible to employees. SDSs provide detailed information on chemical properties, hazards, and protective measures.
- Labeling and Signage: Label all chemical containers with appropriate hazard warnings and information. Use signage to indicate areas where hazardous chemicals are stored or used.
- Personal Protective Equipment (PPE): Provide appropriate PPE for employees and ensure proper use. Regular inspections, maintenance, and PPE training are conducted to ensure effectiveness.
- Emergency Preparedness: Develop and implement emergency response plans for chemical spills, leaks, and other incidents. Conduct regular drills and training to ensure employees are prepared to respond effectively.
Continuous Improvement
Compliance is an ongoing process that requires continuous improvement. Organizations should regularly review and update their safety programs, policies, and procedures to ensure they remain effective and compliant with evolving regulations.
Engaging employees in safety initiatives and building a safety culture can further enhance compliance efforts and promote a safer working environment.
Canadian regulatory standards and compliance are vital in managing chemical hazards and ensuring workplace safety.
By understanding and adhering to these regulations, organizations can protect their workers, avoid legal penalties, and maintain a safe and efficient work environment.
Best Practices to Control Chemical Hazards
Managing chemical hazards in the workplace is crucial for ensuring the safety and health of employees. Effective control measures help prevent accidents, injuries, and illnesses from exposure to hazardous chemicals.
Implementing best practices not only complies with regulatory requirements but also creates a safe working environment and enhances operational efficiency.
Here is an overview of best practices for controlling chemical hazards, focusing on preventive and protective measures.
1. First Aid Measures for Chemical Exposure
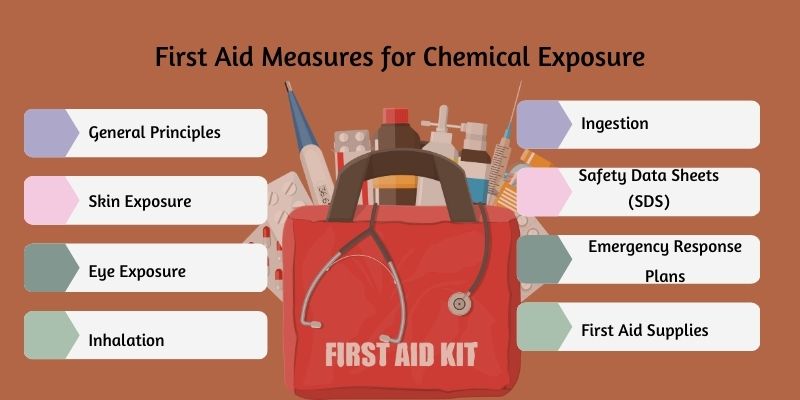
In the event of chemical exposure, immediate and appropriate first aid measures are essential to mitigate harm and prevent further injury.
Understanding the correct procedures and having the necessary supplies readily available can significantly affect the outcome of such incidents. Here, we detail the steps and considerations for first aid in cases of chemical exposure.
General Principles
- Stay Calm and Act Quickly: Remaining calm and responding promptly is crucial in any emergency. Quick and decisive action can significantly reduce the severity of the injury.
- Protect Yourself: Before assisting others, ensure your safety using appropriate personal protective equipment (PPE) to avoid secondary contamination.
Skin Exposure
- Immediate Rinsing: If chemicals come into contact with the skin, rinse the affected area with copious amounts of water for at least 15 to 20 minutes. If a safety shower is available, use it.
- Remove Contaminated Clothing: Carefully remove any contaminated clothing to prevent further exposure. Avoid spreading the chemical to other parts of the body.
- Use Mild Soap: After thoroughly rinsing, gently wash the affected area with soap and water. Do not scrub the skin, as this can exacerbate the injury.
- Seek Medical Attention: If irritation persists or the chemical is known to cause serious harm, seek medical attention immediately.
Eye Exposure
- Flush Eyes Immediately: If chemicals splash into the eyes, flush them immediately with water for at least 15 to 20 minutes. Use an eyewash station if available.
- Hold Eyelids Open: Ensure that the eyelids are held open to irrigate the entire eye surface thoroughly and under the eyelids.
- Remove Contact Lenses: If the person is wearing contact lenses, remove them after the initial flushing period to ensure complete eye rinsing.
- Seek Medical Help: After flushing, seek immediate medical attention to assess and treat any potential eye damage.
Inhalation
- Move to Fresh Air: If someone inhales harmful chemical vapors or gases, move them to an area with fresh air immediately.
- Loosen Tight Clothing: Loosen tight clothing around the neck and chest to aid breathing.
- Monitor Breathing: If the person has difficulty breathing, is unconscious, or exhibits symptoms such as dizziness or headache, seek medical attention immediately.
- Provide Oxygen: If trained to do so and necessary equipment is available, provide supplemental oxygen until medical help arrives.
Ingestion
- Do Not Induce Vomiting: Do not induce vomiting unless instructed to do so by medical personnel or poison control.
- Rinse Mouth: Have the person rinse their mouth thoroughly with water. Avoid swallowing the rinse water.
- Identify the Chemical: Try to identify the ingested chemical and provide this information to medical personnel. Keep the chemical container or label for reference.
- Seek Immediate Medical Attention: Contact poison control or seek emergency medical assistance immediately. Follow their instructions carefully.
Use of Safety Data Sheets (SDS)
- Refer to SDSs: Safety Data Sheets provide specific first aid measures for each chemical. Ensure that SDS for all chemicals in the workplace are accessible and reviewed regularly.
- Train Employees: Regularly train employees to read and use SDS information during emergencies.
Emergency Response Plans
- Develop and Implement Plans: Create comprehensive emergency response plans that include procedures for chemical exposure incidents. Ensure all employees are familiar with these plans.
- Regular Drills and Training: Conduct regular emergency drills and first aid training to ensure employees are prepared to respond effectively in case of chemical exposure.
First Aid Supplies
- Maintain Well-Stocked First Aid Kits: Ensure that first aid kits are well-stocked with supplies appropriate for treating chemical exposures. This includes eyewash solutions, sterile bandages, and neutralizing agents.
- Accessibility: Position first aid kits and emergency showers/eyewash stations in easily accessible locations throughout the workplace.
2. Safe Disposal of Chemicals
Proper disposal of chemicals is crucial to protect human health and the environment from potential hazards.
Incorrect disposal can lead to soil and water contamination, harm to wildlife, and significant legal and financial consequences.
Here's a detailed look at best practices for safely disposing of chemicals:
Identify and Classify Chemicals
- Inventory Management: Keep an accurate inventory of all chemicals used in the workplace. This includes understanding their chemical properties, potential hazards, and disposal requirements.
- Labeling: Ensure all chemical containers contain their contents and associated hazards. This will help identify the appropriate disposal method.
Follow Regulatory Guidelines
- Local and Federal Regulations: Adhere to local, provincial, and federal chemical disposal regulations. In Canada, this includes compliance with regulations set by Environment and Climate Change Canada (ECCC) and other relevant bodies.
- Safety Data Sheets (SDSs): Refer to the SDS for each chemical to understand specific disposal instructions and regulatory compliance requirements.
Use Approved Disposal Methods
- Hazardous Waste Collection Services: Partner with licensed hazardous waste disposal companies to ensure chemicals are disposed of safely and legally.
- On-Site Treatment: Some chemicals can be neutralized or treated on-site before disposal to reduce their hazard level.
- Recycling and Reuse: Recycling or reuse chemicals to minimize waste. This can include returning unused chemicals to suppliers or using them in other processes.
Training and Awareness
- Employee Training: Regularly train employees on proper chemical disposal procedures, including identifying hazardous waste and using disposal equipment.
- Signage and Instructions: Post clear instructions and signage near disposal areas to guide employees in following correct disposal protocols.
Record Keeping
- Documentation: Maintain detailed records of all chemical disposal activities, including quantities, disposal methods, and the waste disposal company's details.
- Audits and Inspections: Conduct regular audits and inspections to ensure compliance with disposal protocols and regulatory requirements.
3. Chemical Segregation
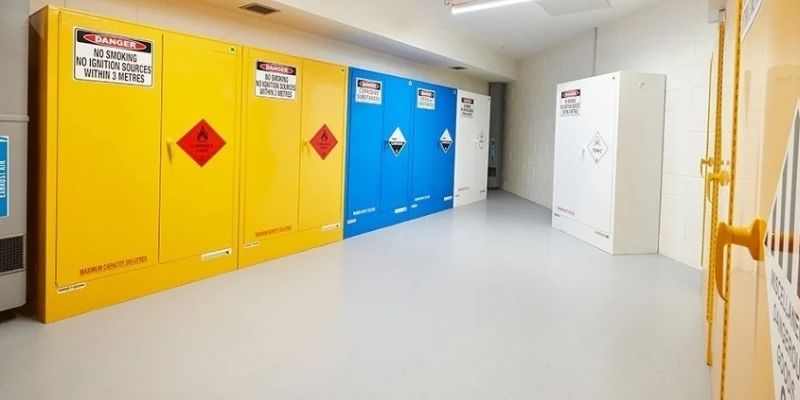
Proper segregation of chemicals is essential to prevent dangerous reactions, contamination, and environmental damage. Different chemicals have different storage and handling requirements to ensure safety.
Here's a detailed explanation of the best practices for chemical segregation:
Understand Chemical Compatibility
- Compatibility Charts: Chemical compatibility charts can identify which chemicals can be stored together and which should be kept apart. These charts are often available from regulatory bodies or chemical suppliers.
- Segregation by Hazard Class: Segregate chemicals based on their hazard class, such as flammable, corrosive, toxic, and reactive substances. This prevents reactions that could lead to fires, explosions, or the release of toxic gases.
Proper Storage Solutions
- Separate Storage Areas: Designate specific storage areas for different types of chemicals—for example, store flammables in a fire-resistant cabinet and corrosives in a separate, ventilated area.
- Secondary Containment: Use secondary containment systems, such as spill trays and bunds, to prevent leaks from spreading to other areas.
Labeling and Signage
- Clear Labeling: Label all chemical containers with their contents and associated hazards. Use color-coded labels or signs to indicate different hazard classes.
- Warning Signs: Post warning signs in storage areas to inform employees about the presence of hazardous chemicals and the required safety precautions.
Training and Procedures
- Employee Training: Regularly train employees on chemical segregation principles, compatibility charts, and emergency procedures.
- Standard Operating Procedures (SOPs): Develop and enforce SOPs for chemical storage and handling to ensure consistent and safe practices.
Regular Inspections
- Routine Checks: Regularly inspect chemical storage areas to ensure compliance with segregation protocols and identify and address potential hazards.
- Audit Records: Keep records of inspections and any corrective actions taken to maintain a safe working environment.
4. Spill Prevention and Control
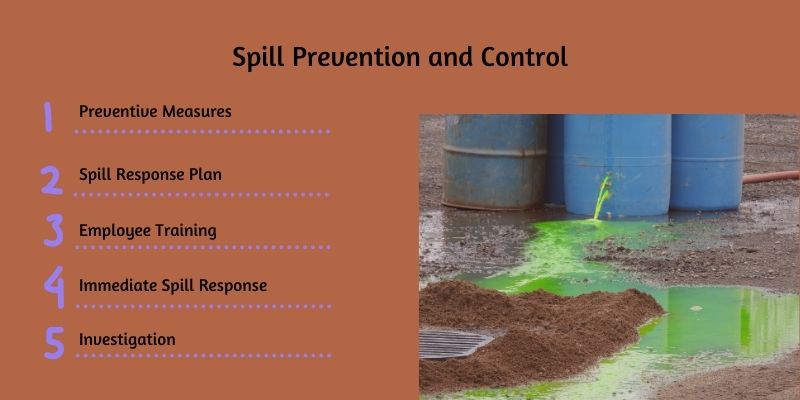
Preventing and controlling chemical spills is critical to maintaining a safe workplace and protecting the environment.
Effective spill prevention and control strategies minimize the risk of exposure and contamination. Here's a detailed look at these strategies:
Preventive Measures
- Proper Storage: Store chemicals in appropriate containers that are in good condition and compatible with the chemical. Ensure containers are adequately sealed when not in use.
- Secondary Containment: To contain leaks and spills, use secondary containment systems like spill trays, bunds, and sump pallets.
- Regular Maintenance: Inspect and maintain storage containers, piping, and equipment to prevent leaks and spills. Repair or replace any damaged or deteriorating equipment promptly.
Spill Response Plan
- Develop a Plan: Create a comprehensive spill response plan outlining the steps to take during a spill. This plan should include roles and responsibilities, emergency contact information, and specific response procedures for different types of chemicals.
- Spill Kits: Equip the workplace with spill kits containing absorbents, neutralizers, personal protective equipment (PPE), and tools for cleaning up spills. Ensure spill kits are easily accessible and located near areas where spills are most likely.
Employee Training
- Spill Response Training: Train employees on the spill response plan, the use of spill kits, and proper cleanup procedures. Conduct regular drills to ensure readiness.
- PPE Use: Ensure employees are trained on the correct use of PPE to protect themselves during spill response and cleanup activities.
Immediate Spill Response
- Contain the Spill: In the event of a spill, contain it immediately using absorbent materials or barriers to prevent it from spreading. Use appropriate PPE to protect against exposure.
- Neutralize if Necessary: Use neutralizing agents to render it harmless before cleanup if the spilled chemical is corrosive or reactive.
- Clean Up and Dispose: Clean up the spill thoroughly and dispose of contaminated materials according to regulatory requirements. Ensure all waste is handled and disposed of safely.
Reporting and Investigation
- Report the Spill: Report significant spills to the appropriate regulatory authorities as required. Document the incident, including the cause, response actions taken, and any injuries or environmental impact.
- Investigate and Improve: Conduct a thorough investigation to determine the root cause of the spill and implement corrective actions to prevent recurrence. Review and update the spill response plan as necessary.
FAQs
How can I find out if my workplace is following chemical safety regulations?
To determine if your workplace follows chemical safety regulations, review the company's compliance with local and federal guidelines and check for regular safety audits and inspections.
What are the critical components of an emergency response plan for chemical spills?
Critical components of an emergency response plan for chemical spills include:
- Immediate containment and cleanup procedures.
- Proper use of spill kits and PPE.
- Clear roles and responsibilities for response actions.
Conclusion
Chemical safety in the workplace is not merely a regulatory requirement but a fundamental responsibility ensuring employees' well-being and the work environment's integrity.
The handling and management of chemicals demand meticulous attention to detail, and each practice, from maintaining a chemical inventory to providing adequate personal protective equipment, plays an indispensable role in safeguarding against potential hazards.
By adhering to these chemical safety practices, organizations can create a safe and healthy workplace that prioritizes the health and safety of their employees.
It's a proactive approach that prevents accidents and injuries and promotes a culture of awareness and responsibility.
Moreover, chemical safety practices extend beyond compliance; they are a cornerstone of sustainable business operations.
By minimizing chemical-related incidents, organizations reduce downtime, protect their reputation, and save costs associated with accidents and environmental damage.
As we move forward, staying updated with the latest safety regulations and embracing technological advancements will further enhance chemical safety. Chemical safety is a shared responsibility involving everyone, from management to employees.
By working together, we can deal with hidden workplace hazards that are productive and safe environments where individuals can thrive without compromising their well-being.