Operating cranes is difficult itself, but if you are trying to do it without proper crane safety training or equipment - the chances of accidents get pretty high. The complexities of controlling and moving heavy loads need proper attention.
Crane accidents can result in catastrophic consequences, affecting the operator and those working in the vicinity. This highlights the critical need for adhering to strict safety measures.
Today, we are exploring crane operation safety tips that need to be considered while operating cranes.
Whether you're an experienced crane operator or a newcomer to the field, these safety tips are designed to enhance your knowledge and vigilance.
By incorporating these safety practices into your routine, you contribute to a safer working environment for yourself and those around you.
14 Crane Operation Safety Tips To Ascertain Worker Safety
Crane operations demand careful execution and crane operator awareness to ensure the safety of both workers and the surrounding environment.
Here are 10 crucial safety tips that enhance crane operation practices, minimizing risks and promoting a secure work environment.
- Conducting a thorough pre-operation inspection
- Importance of proper training and certification
- Clear communication and coordination among team members
- Ensuring proper rigging and attachment of loads
- Evaluating ground stability and load-bearing capacity
- Proper use of standardized hand signals
- Maintaining proper distancing from power lines and other hazards
- Implementing proper barricades and signage
- Establishing exclusion zones and restricted areas
- Conducting routine inspections for wear and tear
- Using Outriggers and Stabilizers
- Ground Support Personnel Roles
- Implementing Tag-out Systems
- Preventing Load Swing
By adhering to these safety tips, workplaces can significantly minimize risks, create a secure environment, and improve workplace safety.
1. Conducting a Thorough Pre-operation Inspection
Before operating a crane, conducting a comprehensive pre-operation inspection is necessary. This involves carefully examining various components, mechanisms, and systems of the crane to ensure they function correctly.
By checking the crane's hydraulics, electrical systems, controls, and safety features, operators can identify potential issues that might compromise safety during operation.
Identifying and addressing problems before initiating any lifting tasks significantly reduces the risk of accidents and equipment failures. This proactive approach enhances safety and prevents accidents that lead to injuries or property damage.
2. Importance of Proper Training and Certification
Proper training and certification of crane operators are fundamental to safe crane operations.
Certified operators have the knowledge and skills to operate cranes efficiently and safely. They understand crane mechanics, load capacities, proper rigging techniques, and safety protocols.
Comprehensive training also covers emergency procedures and effective communication strategies.
Certified operators are better equipped to assess risks, make informed decisions, and respond appropriately to challenging situations. This ultimately contributes to accident prevention and creates a safer working environment for everyone involved in crane operations.
3. Clear Communication and Coordination Among Team Members
.png)
Clear communication and effective coordination between crane operators, ground personnel, and other team members are essential during crane operations.
Standardized hand signals and proper radio communication protocols ensure that instructions are accurately conveyed and understood.
Precise communication helps prevent misunderstandings and reduces the likelihood of accidents caused by misinterpreted signals.
Strong communication also allows for timely adjustments in case of unexpected circumstances, promoting a collaborative safety culture across the work site.
4. Ensuring Proper Rigging and Attachment of Loads
.png)
Proper rigging and attachment of loads are critical factors in crane operation safety. Before lifting any load, ensuring that it is correctly rigged and securely attached is essential.
Appropriate slings, chains, hooks, other rigging equipment, and proper load-securing techniques prevent loads from becoming unstable or falling during lifting.
Adhering to proper rigging practices, operators minimize the risk of load-related accidents and ensure that materials are lifted and transported safely.
5. Evaluating Ground Stability and Load-Bearing Capacity
Evaluating ground stability and load-bearing capacity is crucial before positioning a crane and initiating any lifting operation.
Different types of terrain may have varying load-bearing capacities, and inadequate ground stability can lead to crane tipping or sinking, resulting in accidents.
Proper ground assessment helps operators choose appropriate crane positioning and support measures to ensure stability during lifting tasks. It also prevents overloading the ground or crane, reducing the risk of equipment damage, injuries, and accidents.
6. Proper Use of Standardized Hand Signals
.png)
Effective communication between crane operators and ground personnel relies on standardized hand signals. These signals provide a consistent and easily understandable way to convey instructions and warnings.
Proper training ensures that all team members are familiar with these signals. This allows precise and concise communication even in noisy or obstructed work environments.
By following standardized hand signals, operators can accurately interpret commands, leading to smoother and safer crane operations.
7. Maintaining Proper Distancing From Power Lines and Other Hazards
Maintaining a safe distance from power lines and other potential hazards is crucial during crane operations. Contact between a crane and power lines can result in electrocution and equipment damage.
Operators should always know their surroundings and follow the recommended clearance distances from power lines. Hazard recognition training can also help the worker assess the risks of possible hazards and implement preventive approaches.
Similarly, being vigilant about potential hazards such as other machinery, structures, or personnel helps prevent accidents and ensures the safety of everyone on the worksite.
8. Implementing Proper Barricades and Signage
Proper barricades and signage are essential for maintaining a safe crane operation environment. Barricades help create a clear boundary around the crane's operating area, preventing unauthorized personnel from entering potentially hazardous zones.
Additionally, clear and visible signage informs everyone in the surrounding area about the ongoing crane operation, potential dangers, and required safety precautions. This practice helps minimize the risk of unauthorized access and reduces the likelihood of accidents or injuries.
9. Establishing Exclusion Zones and Restricted Areas
Establishing exclusion zones and restricted areas is fundamental to crane operation safety. These zones are designated areas where only authorized personnel are allowed during crane operations.
Creating these zones helps minimize the risk of collisions, accidents, and injuries. Exclusion zones also prevent unauthorized individuals from entering potentially hazardous areas, reducing the chance of accidents caused by interference or distractions.
Operators and other personnel can work in a controlled and secure environment by strictly adhering to exclusion zones and restricted areas.
10. Conducting Routine Inspections for Wear and Tear
.png)
Regular inspections for wear and tear are vital to crane operation safety. Over time, equipment can experience wear and deterioration due to heavy usage and exposure to various elements.
Conducting routine inspections allows operators and maintenance personnel to identify any signs of damage, malfunction, or deterioration in the crane's components.
Timely detection of issues enables prompt repairs or replacements, reducing the risk of sudden operational failures.
By consistently maintaining the crane in optimal condition through routine inspections, operators enhance safety and prevent accidents caused by equipment failures.
11. Using Outriggers and Stabilizers
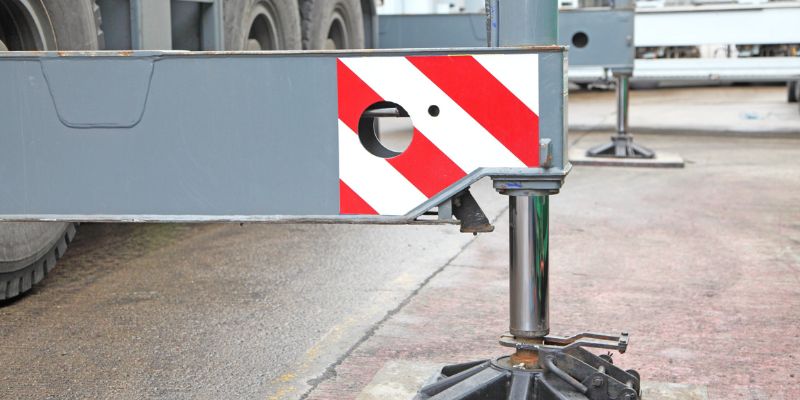
Using outriggers and stabilizers is crucial for ensuring crane operation safety. They provide a stable crane base, preventing tipping and enhancing the machine's overall balance.
Properly using these components is essential for safe lifting operations, especially when working on uneven or soft ground.
Outriggers are extendable arms attached to the crane's chassis. When deployed, they increase the crane's footprint, distributing the load more evenly and reducing the risk of tipping. Before extending the outriggers, it's essential to assess the ground conditions.
The area should be free of obstacles, and the ground should be firm and level. Additional support, such as cribbing or mats, may be required to distribute the load and prevent the outriggers from sinking if the ground is soft or unstable.
When deploying the outriggers, it is essential to extend them fully and lock them in place. Partial extension can compromise stability and increase the risk of accidents.
Operators should use a spirit level or an inclinometer to ensure the crane is level once the outriggers are deployed. A level crane is crucial for safe lifting operations, as even slight tilts can significantly impact the crane's stability under load.
Stabilizers work similarly to outriggers but typically provide additional support in specific directions. They are instrumental when working in tight spaces where full outrigger deployment isn't possible.
Proper use of stabilizers involves ensuring they are extended fully and locked securely. Regular inspection and maintenance of outriggers and stabilizers are essential to ensure they are in good working condition and free of defects that could compromise their effectiveness.
Crane operators and ground support personnel should receive thorough training on the proper deployment and use of these components.
They should also be trained to recognize and respond to potential issues, such as soft ground or obstacles that could impede the safe deployment of outriggers and stabilizers.
Proper assessment of ground conditions, full extension and locking of outriggers, regular maintenance, and thorough training are all essential components of using these devices safely and effectively.
12. Ground Support Personnel Roles
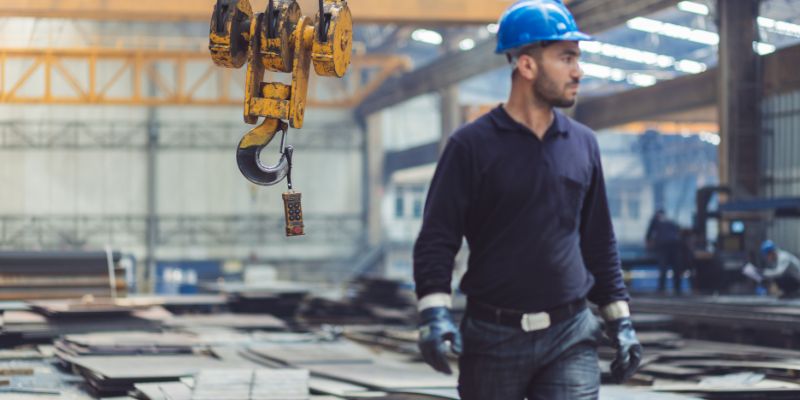
Ground support personnel play a crucial role in ensuring the safety and efficiency of crane operations. These individuals are responsible for various tasks that contribute to the safe lifting and moving of loads.
Understanding and properly executing their roles can significantly reduce the risk of accidents and improve overall safety.
One of the primary responsibilities of ground support personnel is to assist with the setup and positioning of the crane. This includes helping to deploy outriggers and stabilizers, ensuring the crane is level, and verifying that the work area is clear of obstacles.
Ground support personnel must thoroughly understand the crane's operational parameters and the specific requirements of the lifting operation.
Communication is another critical aspect of ground support personnel's roles. They act as the crane operator's eyes and ears, providing guidance and information that the operator may not be able to see from the cab.
Ground support personnel can relay important information about the load, surroundings, and potential hazards using standard hand signals or radio communication. Effective communication helps prevent misunderstandings and ensures the operator can make informed decisions.
Load rigging is another critical responsibility of ground support personnel. Proper rigging is essential for safe lifting operations.
Ground support personnel must ensure loads are securely attached to the crane's hook using the appropriate rigging techniques and equipment.
They must inspect the rigging gear for wear or damage and replace any defective equipment. Proper load rigging helps prevent dangerous load shifts and drops.
Monitoring the work area for potential hazards is another important task. Ground support personnel must constantly be aware of their surroundings, looking for obstacles, overhead power lines, or other hazards that could interfere with the lifting operation.
They should also monitor weather conditions, as wind, rain, and other environmental factors can impact crane stability and load control.
Safety briefings and meetings ensure that all ground support personnel know their roles and responsibilities.
Regular briefings before lifting operations can help identify potential hazards, review safety procedures, and ensure everyone is on the same page.
Continuous training and education are also essential to update ground support personnel on the latest safety practices and regulations.
Ground support personnel are vital to crane operation safety. Their roles include assisting with setup, ensuring effective communication, proper load rigging, monitoring the work area, and participating in safety briefings.
13. Implementing Tag-out Systems
Implementing tag-out systems is an essential safety measure in crane operations to prevent accidental energization or movement of machinery during maintenance or repairs.
A tag-out system involves placing a tag on the crane's controls or power sources to indicate that the equipment is out of service and should not be operated.
A tag-out system primarily aims to protect workers performing maintenance or repairs on the crane.
Tag-out systems prevent unauthorized or accidental equipment activation by indicating that it is out of service, which could result in serious injuries or fatalities.
Developing a tag-out procedure is the first step in implementing an effective system. This procedure should outline the steps to be taken when tagging out equipment, including who is authorized to apply and remove tags, how to apply tags properly, and how to verify that the equipment is safely de-energized.
The procedure should be documented and made easily accessible to all personnel involved in crane operations.
All crane operations, maintenance, or repair employees should receive comprehensive training on the tag-out procedures. This training should cover the importance of the tag-out system, how to apply and remove tags, and the consequences of failing to follow the procedures.
Regular refresher training ensures all personnel remain knowledgeable about the system.
Communication plays a vital role in the effectiveness of tag-out systems. Clear communication protocols should ensure all personnel know when equipment is tagged out and why.
This can include using visual aids, such as tags with clear and concise information, and maintaining a log of tagged-out equipment.
Effective communication helps prevent misunderstandings and ensures that everyone is aware of the current status of the equipment.
Regular tag-out system audits and inspections are necessary to ensure its continued effectiveness.
These audits should verify that tags are being applied and removed correctly, that the tag-out procedures are followed, and that all necessary training has been completed.
Any issues identified during audits should be addressed promptly to prevent potential safety hazards.
Reporting and documentation are also essential aspects of a tag-out system. Any incidents or near misses involving tagged-out equipment should be reported and documented to identify areas for improvement.
Keeping detailed records of tag-out activities, including the dates and times tags were applied and removed, helps maintain accountability and provides a reference for future audits.
Implementing a tag-out system is crucial for ensuring the safety of crane operations. An effective tag-out system includes a well-developed procedure, comprehensive training, clear communication, regular audits, and thorough documentation.
Tag-out systems protect workers and help maintain a safe working environment by preventing equipment's unauthorized or accidental activation.
14. Preventing Load Swing
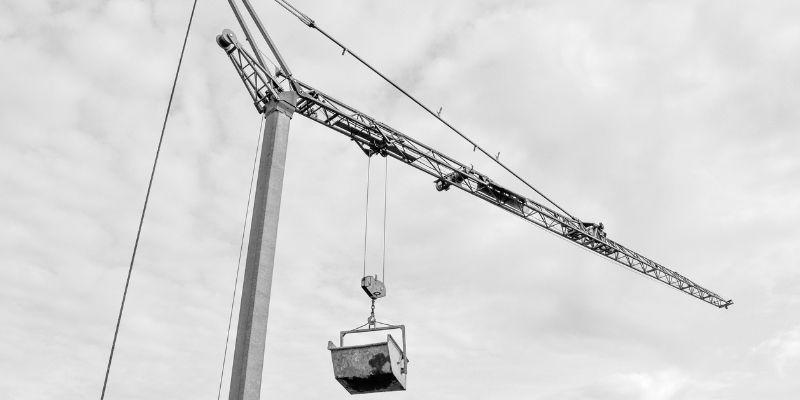
Preventing load swing is critical to crane operation safety, as uncontrolled load movement can lead to accidents, injuries, and damage to equipment.
Load swing occurs when a suspended load moves unexpectedly due to wind, sudden crane movements, or improper rigging.
Implementing strategies to prevent load swings is essential for maintaining control and ensuring safe lifting operations.
Proper load rigging is the first step in preventing load swing. Ensuring that the load is securely attached to the crane's hook using appropriate rigging techniques and equipment is crucial.
The rigging should be evenly distributed to prevent the load from shifting during lifting.
Ground support personnel should inspect the rigging gear for any wear or damage and replace any defective equipment. Proper rigging helps maintain load stability and reduces the risk of swing.
Controlling the crane's movements is another essential factor in preventing load swing. Operators should use smooth and gradual movements when lifting, lowering, or moving loads.
Sudden or jerky movements can cause the load to swing uncontrollably, increasing the risk of accidents. Using a crane with precision controls can help operators make fine adjustments and maintain better control over the load.
Monitoring weather conditions is essential, as wind is a significant factor that can cause load swings.
Operators should know the wind speed and direction and adjust their lifting operations accordingly. In high-wind conditions, it may be necessary to delay lifting operations or use additional measures, such as guy lines or tag lines, to stabilize the load.
Guy lines are ropes or cables attached to the load to provide additional control, while tag lines are used by ground support personnel to guide and stabilize the load during lifting.
Implementing load stabilization devices, such as anti-sway systems or load-dampening devices, can also help prevent load swings. These devices are designed to reduce the movement of suspended loads.
Anti-sway systems use sensors and control algorithms to detect and counteract load swing while load-dampening devices use mechanical means to absorb and dissipate energy from the load's movement.
These technologies can significantly enhance the stability of suspended loads and reduce the risk of swing.
Planning and coordination are also essential for preventing load swings. Before lifting operations begin, a detailed plan should be developed that considers all potential hazards and establishes strategies for mitigating them.
This plan should include an assessment of the load, the crane's capacity, the lifting path, and the environmental conditions.
Coordination between the crane operator, ground support personnel, and other on-site workers is crucial to ensure everyone knows the plan and responds appropriately to any changes or issues.
Preventing load swing is a critical aspect of crane operation safety that requires proper rigging, controlled crane movements, monitoring weather conditions, implementing stabilization devices, thorough training, clear communication, and careful planning and coordination.
By taking these measures, crane operators and ground support personnel can maintain better control over suspended loads, reduce the risk of accidents, and ensure safe and efficient lifting operations.
Crane Operation Safety Tips - FAQS
Why is crane operation safety important?
Crane operation safety is important because it prevents accidents, injuries, and equipment damage, ensuring the well-being of operators, workers, and bystanders while maintaining efficient and productive operations.
How can I ensure safe crane operation?
To ensure safe crane operation, follow thorough pre-operation checks, provide proper training, maintain clear communication, adhere to rigging procedures, assess ground stability, use standardized hand signals, maintain distance from hazards, implement proper barricades and signage, establish exclusion zones and conduct routine equipment inspections.
What should I check during a pre-operation inspection?
During a pre-operation inspection of a crane, check for any visible damage, ensure proper functioning of all controls and safety devices, assess wire ropes and chains for wear and tear, inspect hydraulic systems, verify proper load capacity information, and examine the overall structural integrity of the crane.
Final Words
As highlighted in this comprehensive guide on "Crane Operation Safety Tips," the significance of fool-proof safety measures cannot be underestimated. The operation of cranes involves coordination, extensive training, and adherence to strict protocols to ensure the well-being of both the crane operators and those working in the vicinity.
By following the ten safety tips outlined here, crane operators and their teams can significantly minimize the risks of this challenging task.
So, whether you're a seasoned crane operator or new to the field, remember that safety isn't just a requirement—it's a commitment to the well-being of everyone involved.
For further training and resources to enhance your crane operation safety knowledge, consider exploring Canada Safety Training!