Keeping equipment in good working condition is essential for safety and efficiency in any workplace.
Regular equipment inspection helps identify potential problems early, preventing accidents and on-time and costly repairs.
This equipment inspection guide provides a comprehensive overview of equipment inspection, covering everything you need to know to ensure your equipment remains safe and reliable.
According to a study by François Gauthier, equipment failures had a major effect on the number and severity of reported accidents: 272 out of 773 accidental events were related to equipment failure, where 13 had direct human consequences.
Whether you're a maintenance technician, equipment operator, or facility manager, this guide will help you understand the importance of equipment inspection and how to conduct thorough inspections effectively.
This guide will help you understand the key elements of an effective inspection program, from understanding the types of equipment inspections to learning the step-by-step process of conducting inspections.
By following the guidance provided in this guide, you'll be able to identify potential workplace hazards, detect equipment deficiencies, and take proactive measures to address issues before they escalate.
1. Pre-Inspection Preparation
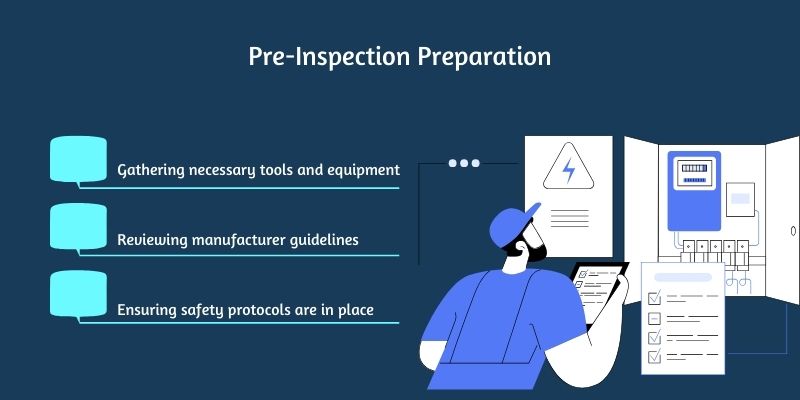
Proper preparation is crucial before conducting equipment inspections to ensure thoroughness, accuracy, and safety.
Pre-inspection preparation involves gathering necessary tools and equipment, reviewing manufacturer guidelines and specifications, and ensuring safety protocols are in place.
Gathering Necessary Tools and Equipment
Gathering the necessary tools and equipment is the first step in pre-inspection preparation. This may include inspection checklists, measuring devices, testing equipment, lubricants, and personal protective equipment (PPE) such as gloves, goggles, and safety harnesses.
PPE training can help workers assess whether the PPE equipment is working. Here are some of the PPE that require regular inspection.
-
Dangerous goods classes
-
Oil and gas industry
-
Hazardous chemicals
Having the right tools readily available ensures that inspectors can perform inspections efficiently and effectively.
Reviewing Manufacturer Guidelines and Specifications
Reviewing manufacturer guidelines and specifications ensures that recommended procedures and standards conduct inspections.
Manufacturers often provide detailed instructions on inspecting equipment, including specific inspection points, maintenance intervals, and acceptable tolerances.
By familiarizing themselves with manufacturer guidelines, inspectors can ensure that inspections are thorough and accurate, reducing the risk of oversight or error.
Ensuring Safety Protocols Are in Place
Ensuring safety protocols are in place is critical to protect inspectors from potential hazards during equipment inspections.
This may include conducting pre-inspection safety checks, such as verifying that equipment is properly locked out and tagged, ensuring adequate lighting and ventilation, and identifying potential hazards such as electrical, mechanical, or chemical risks.
Inspectors should also ensure that they are trained in proper safety procedures and that emergency response plans are in place in case of accidents or incidents.
By prioritizing pre-inspection preparation and following these steps, inspectors can ensure that equipment inspections are conducted safely, accurately, and efficiently, reducing the risk of accidents, equipment failures, and downtime in the workplace.
2. Visual Inspection
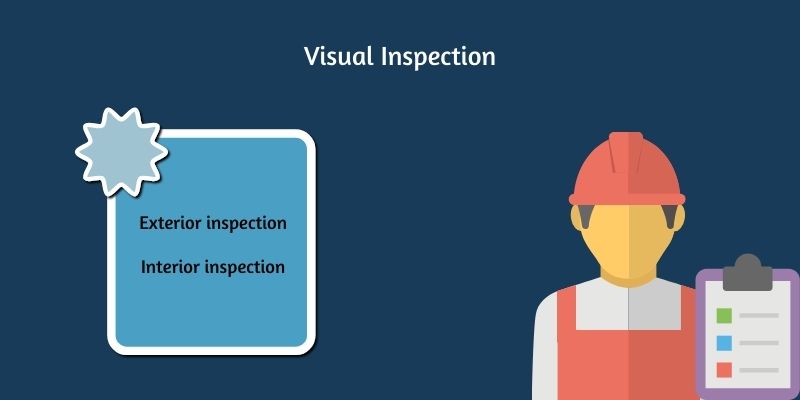
Visual inspection is a fundamental aspect of equipment maintenance and safety. It involves thoroughly examining equipment components and surfaces for signs of damage, wear, or deterioration.
Visual inspection is typically the first step in the inspection process. It provides valuable insights into the equipment's overall condition.
Exterior Inspection
The exterior inspection focuses on assessing the equipment's outer surface for any visible damage, defects, or irregularities. Inspectors should examine all exterior components, including body panels, casings, guards, and covers, looking for signs of cracks, dents, scratches, or corrosion.
Any damage to the exterior of the equipment could indicate underlying issues that may compromise its functionality or safety.
Checking for Physical Damage
During the visual inspection, inspectors should pay close attention to any physical damage to the equipment. This includes inspecting for cracks, fractures, punctures, or deformation of structural components.
Physical damage can weaken the integrity of the equipment and increase the risk of failure or malfunction, posing safety hazards to operators and bystanders.
Identifying and addressing physical damage early through visual inspection can prevent further deterioration and potential accidents.
Examining for Signs of Wear and Tear
In addition to physical damage, inspectors should examine the equipment for signs of wear and tear resulting from normal usage or aging.
This may include worn or frayed cables, loose or missing fasteners, faded or peeling paint, or worn-out seals and gaskets. Wear and tear are natural occurrences in equipment over time.
Still, excessive or uneven wear could indicate issues with maintenance, lubrication, or operating conditions that must be addressed to prevent equipment failure.
Inspectors can identify potential issues early by conducting a thorough visual inspection, allowing for timely maintenance and repairs to keep the equipment in optimal condition and ensure the safety of operators and personnel.
Visual inspection is a critical preventive maintenance measure that helps minimize downtime, extend equipment lifespan, and maintain workplace productivity.
Interior Inspection
Interior inspection involves examining the internal components and systems of equipment to assess their condition, functionality, and integrity.
This comprehensive inspection is essential for detecting hidden issues affecting equipment performance, reliability, and safety.
Assessing Components for Proper Functioning
During the interior inspection, inspectors thoroughly assess the functionality of internal components and systems to ensure they are operating as intended.
This may include inspecting mechanical, electrical, hydraulic, or pneumatic systems and control mechanisms, sensors, and actuators.
Inspectors should check for any signs of malfunction, abnormal operation, or unusual noises that may indicate underlying problems.
Proper functioning of internal components is critical for the overall performance and safety of the equipment.
Looking for Signs of Leaks or Corrosion
During the interior inspection, inspectors also look for signs of leaks or corrosion, which can compromise the integrity and functionality of equipment components.
Leaks in hydraulic or pneumatic systems, coolant leaks, oil leaks, or fuel leaks can indicate faulty seals, worn-out hoses, or damaged fittings that must be addressed promptly to prevent fluid loss, contamination, or environmental hazards.
Similarly, corrosion or rust on metal components can weaken their structural integrity and lead to premature failure or malfunction.
Inspectors should carefully inspect all interior surfaces, pipes, fittings, and connections for any signs of leaks or corrosion and take appropriate corrective actions.
By conducting a thorough interior inspection, inspectors can identify potential issues that may not be visible during external inspections. This allows for timely maintenance and repairs to prevent equipment downtime, accidents, and costly repairs.
Interior inspection is an essential component of overall equipment maintenance and safety management, helping to ensure the reliability, performance, and longevity of equipment in industrial and commercial settings.
3. Functional Inspection
Functional inspection involves testing the operational functionality of equipment components and systems to ensure they are performing as intended.
This critical step in the inspection process verifies that the equipment can safely and efficiently carry out its intended tasks.
Testing Equipment Operation
During the functional inspection, inspectors systematically test the operation of equipment components and systems to verify their functionality. This may involve activating controls, switches, and buttons to start, stop, or adjust equipment operation.
Inspectors observe the equipment's response to these inputs, checking for any abnormal sounds, vibrations, or movements that may indicate underlying issues.
Testing equipment operation allows inspectors to assess the overall performance and responsiveness of the equipment in real-world conditions.
Running Diagnostics if Applicable
In some cases, running diagnostics may be necessary to assess the condition and performance of equipment components more thoroughly. Diagnostics tools and software can provide the following:
-
Valuable insights into the health of electrical, mechanical, hydraulic, or pneumatic systems.
-
Identifying potential issues such as sensor malfunctions.
-
Error codes.
-
System faults.
Inspectors may use diagnostic equipment to conduct comprehensive tests, analyze data, and diagnose problems accurately, allowing for targeted maintenance and repairs.
Checking for Proper Functionality of Moving Parts
Inspectors also check for the proper functionality of moving parts during the functional inspection, ensuring that all mechanical components operate smoothly and safely.
This may include inspecting belts, chains, gears, bearings, shafts, and other moving parts for signs of wear, misalignment, or damage.
Inspectors verify that moving parts are adequately lubricated, aligned, and tensioned to reduce friction, minimize wear, and prevent premature failure.
Proper functionality of moving parts is essential for the equipment's overall performance, reliability, and safety during operation.
By conducting a thorough functional inspection, inspectors can verify that equipment components and systems are operating correctly and reliably, reducing the risk of equipment failures, accidents, and downtime in the workplace.
Functional inspection is an essential aspect of preventive maintenance and safety management. It ensures that equipment remains in optimal condition and continues to meet performance requirements in industrial and commercial settings.
Verifying Calibration and Accuracy
Verifying calibration and accuracy is critical to functional inspection, especially for equipment that relies on precise measurements or readings to perform its intended functions.
Calibration ensures that equipment instruments and sensors are accurately calibrated to provide reliable and accurate measurements, ensuring the quality and consistency of results.
Using Calibration Tools if Necessary
Using calibration tools may be necessary to verify the accuracy of equipment measurements and ensure proper calibration.
Calibration tools, such as calipers, micrometers, gauges, or calibration software, allow inspectors to compare equipment readings against known reference standards and adjust calibration settings as needed.
Inspectors may perform calibration checks periodically or whenever there are indications of measurement inaccuracies or discrepancies.
Ensuring Measurements Meet Required Standards
During the verification process, inspectors ensure that equipment measurements meet required standards and specifications.
This involves comparing measured values against predetermined tolerance limits, industry standards, or regulatory requirements to ensure compliance and reliability.
Inspectors verify that measurements are within acceptable limits and that deviations from standard values are identified and addressed promptly to prevent equipment operation errors or inaccuracies.
Verifying calibration and accuracy is essential for ensuring the reliability, precision, and consistency of equipment measurements. This is critical for maintaining product quality, meeting regulatory requirements, and ensuring safety in various industries.
By using calibration tools, ensuring measurements meet required standards, and addressing any calibration issues promptly, inspectors can verify the accuracy of equipment measurements and ensure the quality and integrity of results.
This helps to minimize the risk of errors, improve operational efficiency, and enhance overall productivity in industrial and commercial settings.
4. Documentation
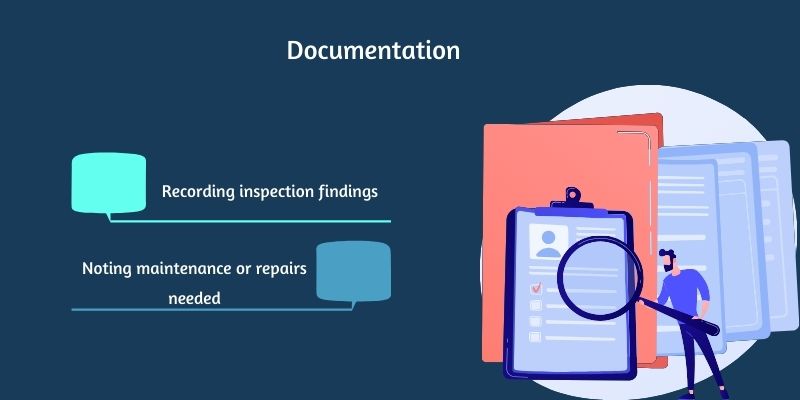
Documentation plays a crucial role in the equipment inspection process by providing a record of inspection findings, facilitating communication, and ensuring accountability.
Proper documentation helps track equipment maintenance history, identify trends or patterns, and support decision-making for maintenance planning and resource allocation.
Recording Inspection Findings
Recording inspection findings involves documenting observations, measurements, and assessments.
Inspectors should accurately record equipment conditions, identified issues or defects, inspection dates, and any corrective actions taken.
This information provides a comprehensive snapshot of equipment status and performance over time, serving as a valuable reference for future inspections and maintenance activities.
Using Standardized Forms or Software
Using standardized forms or software helps streamline the documentation process and ensure consistency in recording inspection data.
Standardized inspection forms provide a structured format for recording essential information, including equipment identification details, inspection criteria, inspection results, and recommendations for corrective actions.
Alternatively, inspection software solutions offer digital platforms for capturing, storing, and analyzing inspection data, allowing for easier data retrieval, analysis, and reporting.
Documenting Any Issues or Discrepancies Found
Documenting any issues or discrepancies during the inspection is critical for identifying maintenance needs and implementing timely corrective actions.
Inspectors should document observed defects, malfunctions, abnormalities, and potential causes and recommend corrective measures to accurately identify the causes of accidents.
This documentation helps prioritize maintenance tasks, allocate resources effectively, and minimize the risk of equipment failures or downtime.
Organizations can establish a documentation system that supports effective equipment maintenance and compliance with regulatory requirements by recording inspection findings, using standardized forms or software, and documenting any issues or discrepancies found.
Documentation is a valuable tool for tracking equipment performance, identifying maintenance needs, and promoting continuous improvement in equipment reliability and safety.
Noting Maintenance or Repairs Needed
Noting maintenance or repairs needed is a crucial step in the equipment inspection process, as it helps identify issues or deficiencies that require attention to ensure the continued safe and reliable operation of equipment.
During inspections, inspectors should carefully document any observed maintenance needs or repair requirements, including immediate concerns and potential future issues.
This may involve noting defects, malfunctions, abnormal wear, or other signs of deterioration that could impact equipment performance or safety.
Organizations can proactively address issues by documenting maintenance needs before they escalate into costly repairs or equipment failures, minimizing downtime and ensuring operational continuity.
Prioritizing Tasks Based on Urgency
Prioritizing tasks based on urgency is essential for effective maintenance planning and resource allocation.
Not all maintenance needs identified during inspections may require immediate attention, and it's important to prioritize tasks based on their impact on equipment performance, safety, and production processes.
Inspectors should assess the urgency of maintenance needs by considering safety risks, regulatory compliance requirements, equipment criticality, and potential consequences of failure.
Tasks that pose imminent safety hazards or significant operational risks should be prioritized for immediate action. At the same time, less critical maintenance needs may be scheduled for later attention based on available resources and workload.
Assigning Responsibility for Addressing Issues
Assigning responsibility for addressing issues ensures accountability and accountability in addressing maintenance needs identified during inspections.
Once maintenance needs are noted and prioritized, organizations should assign responsibility to appropriate personnel or teams to address each issue promptly and effectively.
This may involve assigning tasks to maintenance technicians, engineers, or supervisors with the necessary skills, expertise, and resources to perform the required maintenance or repairs.
Clear assignment of responsibility helps ensure that maintenance tasks are completed promptly and that all necessary actions are taken to address identified issues and maintain equipment reliability and safety.
Additionally, assigning responsibility helps track progress, monitor the completion of tasks, and ensure that no maintenance needs fall through the cracks, contributing to overall efficiency and effectiveness in equipment maintenance management.
5. Post-Inspection Procedures
Post-inspection procedures are essential for effectively communicating inspection findings to relevant stakeholders and taking appropriate action to address any identified issues or concerns.
These procedures facilitate collaboration, decision-making, and follow-up actions to ensure safe and reliable equipment operation.
Communicating Findings to Relevant Stakeholders
Communicating inspection findings to relevant stakeholders is critical for ensuring transparency, accountability, and informed decision-making.
Inspectors should promptly share inspection reports, findings, and recommendations with all equipment maintenance and operation stakeholders, including supervisors, maintenance personnel, equipment owners, and safety officers.
Clear and comprehensive communication ensures that all parties know the equipment's condition, maintenance needs, and any safety risks identified during the inspection. This enables them to take appropriate actions and allocate resources accordingly.
Notifying Supervisors or Equipment Owners
Notifying supervisors or equipment owners of inspection findings is essential for obtaining authorization and supporting necessary maintenance or repair activities.
Inspectors should promptly inform supervisors or equipment owners of any critical issues, safety concerns, or maintenance needs identified during the inspection.
This allows supervisors to assess the situation's urgency, allocate resources, and make informed decisions about prioritizing and scheduling maintenance tasks.
Open communication between inspectors and supervisors facilitates collaboration. It ensures that inspection findings are addressed promptly and effectively to minimize risks and disruptions in equipment operation.
Discussing Recommended Actions or Repairs
Discussing recommended actions or repairs with relevant stakeholders enables collaborative decision-making.
It ensures appropriate measures are taken to address identified issues. Inspectors should engage in discussions with supervisors, maintenance personnel, and other stakeholders to review inspection findings, discuss recommended actions or repairs, and develop a plan for addressing maintenance needs.
This may involve evaluating different options, considering cost-effectiveness, and prioritizing tasks based on urgency and available resources.
By involving stakeholders in the decision-making process, organizations can ensure that maintenance activities are aligned with operational priorities, budget constraints, and safety objectives, leading to more efficient and effective equipment maintenance management.
By following post-inspection procedures, organizations can ensure that inspection findings are communicated effectively, decision-making is informed, and necessary actions are taken to address maintenance needs promptly.
Effective post-inspection procedures contribute to equipment's overall reliability, safety, and performance, enhancing operational efficiency and minimizing risks in industrial and commercial settings.
Scheduling Follow-up Inspections or Maintenance
Scheduling follow-up inspections or maintenance is essential for maintaining the reliability and safety of equipment over time.
After completing an initial inspection and addressing any immediate maintenance needs, organizations should establish a schedule for regular follow-up inspections or preventive maintenance activities.
These follow-up inspections allow inspectors to monitor the condition of equipment, identify any new issues or deterioration, and address maintenance needs proactively before they escalate into more significant problems.
The frequency of follow-up inspections may vary depending on equipment criticality, usage patterns, environmental conditions, and regulatory requirements.
By scheduling follow-up inspections at regular intervals, organizations can ensure that equipment remains in optimal condition, minimize the risk of unexpected failures or downtime, and extend equipment lifespan.
Setting Timelines for Addressing Identified Issues
Setting timelines for addressing identified issues is essential for prioritizing maintenance tasks and ensuring timely resolution of equipment issues.
After completing an inspection and documenting maintenance needs, organizations should establish clear timelines or deadlines for addressing each identified issue based on its urgency and criticality.
Timelines should consider safety risks, operational impact, regulatory compliance requirements, and resource availability. Urgent or critical issues that pose immediate safety hazards or operational risks should be addressed promptly, typically within a short timeframe.
Less critical issues may have longer timelines based on their impact on equipment performance and production processes.
By setting timelines for addressing identified issues, organizations can prioritize maintenance activities effectively, allocate resources efficiently, and ensure that maintenance needs are addressed promptly to prevent equipment failures or disruptions in operations.
Planning for Ongoing Equipment Upkeep
Planning for ongoing equipment upkeep involves developing a comprehensive maintenance strategy and schedule to ensure equipment's continued reliability and performance over its lifecycle.
This includes addressing immediate maintenance needs and implementing proactive maintenance practices to prevent issues from occurring in the first place.
Organizations should develop a maintenance plan that outlines routine maintenance tasks, such as lubrication, cleaning, calibration, and inspections, as well as preventive maintenance activities, such as component replacements, system upgrades, and predictive maintenance techniques.
By planning for ongoing equipment upkeep, organizations can optimize equipment performance, minimize the risk of unexpected failures or downtime, and maximize return on investment in equipment assets.
Additionally, ongoing equipment upkeep helps extend equipment lifespan, improve operational efficiency, and enhance overall productivity in industrial and commercial settings.
Conclusion
Practical equipment inspection is a foundation of maintenance management, ensuring equipment safety, reliability, and longevity in various industries.
Throughout this equipment inspection guide, we've explored the importance of equipment inspection and highlighted key considerations for each step.
Equipment inspection is a proactive measure to identify potential issues, defects, or hazards before they escalate into costly repairs, accidents, or downtime.
Organizations can mitigate risks, optimize equipment performance, and maintain compliance with regulatory standards by conducting thorough inspections.
Inspectors perform visual, functional, and interior inspections during the inspection, verify calibration, and note any needed maintenance or repairs.
Post-inspection procedures include:
-
Communicating findings to relevant stakeholders.
-
Scheduling follow-up inspections or maintenance.
-
Planning for ongoing equipment upkeep.
Effective communication, timely action, and proactive planning are essential for addressing maintenance needs promptly and maintaining equipment reliability over time.
Incorporating these best practices into equipment inspection processes can help organizations enhance safety, minimize downtime, and optimize operational efficiency.