In the ever-evolving landscape of workplace safety, understanding how to tackle workplace hazards effectively is essential.
This hierarchy of controls and safety guides is tailored to Canadian companies and workers. It will guide you through the complex journey of safeguarding your workplace.
At its core, the hierarchy of controls is a systematic approach to managing risks. It's not a one-size-fits-all solution but a personalized strategy that adapts to the unique challenges of your workplace.
As we dive into the topic, we'll break down the hierarchy into practical steps that resonate with the Canadian work environment.
From eliminating hazards at the source to equipping workers with the right protective gear, we'll explore the layers of control measures, ensuring a comprehensive understanding that empowers you to make informed decisions.
This isn't just about compliance; it's about cultivating a culture where safety is a shared commitment. So, join us if you're a manager seeking to enhance workplace safety or a worker keen on understanding your role in the bigger safety picture.
What is the Hierarchy of Controls?
The hierarchy of controls is a systematic approach to managing and reducing workplace hazards. This approach is widely used in occupational health and safety to minimize risk exposure by implementing the most effective control measures.
The hierarchy is structured in descending order of effectiveness, emphasizing eliminating hazards at the source whenever possible.
Understanding and applying this hierarchy is essential for ensuring a safe working environment in various industries, including construction, manufacturing, and healthcare.
Why Use the Hierarchy of Controls?
The hierarchy of controls is a fundamental concept in occupational health and safety management.
It provides a structured approach to hazard mitigation, prioritizing the most effective control measures to protect workers.
Here are several reasons why using the hierarchy of controls is crucial:
Maximizes Safety and Health Protection
- Effectiveness: The hierarchy ensures that the most effective measures (elimination and substitution) are considered first, providing the highest level of protection.
- Comprehensive Risk Reduction: By addressing and identifying hazards at their source, the hierarchy reduces the overall risk rather than just mitigating the symptoms.
Structured and Systematic Approach
-
Clarity and Consistency: The hierarchy offers a step-by-step method for evaluating and implementing safety controls, ensuring a consistent approach across workplaces and industries.
-
Prioritization: It helps prioritize control measures based on their effectiveness, ensuring that resources are used efficiently.
Proactive Hazard Management
-
Preventive Measures: The hierarchy encourages proactive measures that prevent hazards from entering the workplace by focusing on elimination and substitution first.
-
Long-term Solutions: Engineering controls and administrative controls provide sustainable, long-term solutions to hazard management, reducing the need for reliance on PPE.
Regulatory Compliance
-
Meeting Standards: Many occupational health and safety regulations and standards are based on the hierarchy of controls. Using this framework helps ensure compliance with legal requirements.
-
Documentation and Justification: The hierarchy provides a documented process for managing hazards, which can be crucial during inspections and audits.
Improved Workplace Culture
-
Safety Mindset: Implementing the hierarchy promotes a safety culture by demonstrating a commitment to worker protection and proactive hazard management.
-
Employee Involvement: Involving employees in hazard identification and control measures can enhance their engagement and adherence to safety protocols.
Cost-Effectiveness
-
Reducing Incidents: The hierarchy helps reduce costs associated with workplace incidents, such as medical expenses, compensation claims, and downtime, by preventing accidents and injuries through effective hazard control.
-
Long-term Savings: Investing in higher-order controls, like elimination and engineering controls, can lead to long-term savings compared to ongoing administrative controls and PPE costs.
Using the hierarchy of controls ensures that the most effective and sustainable hazard controls are implemented first, maximizing employee protection, enhancing compliance with regulations, and fostering a proactive safety culture.
The 5 Levels of the Hierarchy of Controls

Implementing the hierarchy of controls effectively requires a systematic approach, careful planning, and a thorough understanding of workplace hazards. Here are some essential tips to guide the process:
-
Identifying opportunities for elimination
-
Substitution
-
Implementing engineering solutions
-
Developing effective administrative controls
-
Selecting appropriate PPE
Let’s discuss these tips in detail so you can practically utilize them to create a safer work environment.
Level 1: Elimination
A powerful elimination strategy is the first level of the hierarchy of controls safety. This level involves identifying hazards and then outright removing or substituting them, ensuring that workers are not exposed in the first place.
Elimination is about addressing the root cause of a hazard, rendering it nonexistent within the workplace. This proactive approach aims to eradicate potential risks, creating a safer environment.
Examples of Elimination Strategies
Imagine a scenario where a hazardous chemical can be replaced with a less harmful alternative or where a hazardous task can be entirely automated, removing the need for human involvement. These are instances where elimination takes center stage.
Identifying Opportunities for Elimination and Substitution is a critical first step in implementing the hierarchy of controls.
These steps offer the highest level of hazard control by removing or replacing the hazard entirely.
Here's how to identify and implement these opportunities effectively:
Conduct a Thorough Risk Assessment
-
Identify All Hazards: Conduct a comprehensive risk assessment to identify all potential hazards in the workplace. This includes physical, chemical, biological, and ergonomic hazards.
-
Evaluate Risk Levels: Assess the severity and likelihood of each hazard to prioritize which ones need to be addressed first.
Evaluate the Feasibility of Elimination
-
Question Necessity: Ask whether the task or process involving the hazard is necessary. If it can be eliminated without impacting productivity or quality, eliminating it should be the first option.
-
Innovative Solutions: Explore innovative solutions or alternative methods to eliminate the hazard. This might involve changing the design of a process or discontinuing the use of specific equipment or substances.
Benefits and Challenges
The primary benefit of elimination is its effectiveness—no exposure, no risk. However, it often comes with challenges related to feasibility and practicality. Some hazards may be intrinsic to specific processes, making complete elimination challenging.
Level 2: Substitution
Substitution, the second tier in the hierarchy of controls safety, revolves around replacing a hazardous substance or process with a safer alternative.
Unlike elimination, which aims to remove the hazard entirely, substitution involves finding a less harmful counterpart to mitigate risks.
Examples of Substitution Strategies
Consider a scenario where a toxic cleaning chemical is swapped for an environmentally friendly and less hazardous option. This could involve using a non-toxic substance for a particular manufacturing process in industrial settings.
Substitution emphasizes identifying and adopting alternatives that maintain productivity while reducing risk.
Consider Substitution Options
-
Safer Alternatives: Look for safer alternatives that can replace the hazardous element. This could involve using less toxic chemicals, quieter machinery, or ergonomically designed tools.
-
Research and Testing: Conduct research to identify potential substitutes and test them to ensure they provide the same functionality without introducing new hazards.
Engage with Suppliers and Manufacturers
-
Collaborate for Solutions: Work with suppliers and manufacturers to find or develop safer alternatives. They might offer products or solutions that you still need to consider.
-
Industry Best Practices: Stay informed about industry best practices and advancements that could offer new elimination or substitution opportunities.
Cost-Benefit Analysis
-
Evaluate Costs and Benefits: Perform a cost-benefit analysis to weigh elimination or substitution's financial and operational impacts. The long-term benefits, such as reduced injury rates and improved worker morale, often outweigh the initial costs.
-
Long-Term Perspective: Consider the long-term benefits of elimination and substitution, including reduced liability, compliance with regulations, and a safer workplace.
Implementation and Feedback
-
Pilot Programs: Implement pilot programs to test elimination or substitution measures on a small scale before full deployment. This allows for adjustments based on real-world feedback.
-
Gather Feedback: Collect feedback from employees and other stakeholders on the effectiveness and practicality of the new measures. Use this feedback to refine and improve the control measures.
Pros and Cons
The primary advantage of substitution lies in its ability to maintain the continuity of operations while minimizing risks.
However, challenges may arise in finding suitable substitutes that align with operational requirements. Additionally, there might be associated costs or concerns about the efficacy of substitutes.
Level 3: Engineering Controls
Implementing engineering solutions is a crucial step in the hierarchy of controls. These solutions focus on designing or modifying equipment, processes, and work environments to reduce or eliminate hazards.
These controls are considered more effective than administrative controls and personal protective equipment (PPE) because they are built into the system and do not rely on human behavior.
Identify Engineering Control Needs
-
Risk Assessment: Conduct a detailed risk assessment to identify areas where engineering controls can be applied. This involves analyzing processes, equipment, and workplace layouts to pinpoint potential hazards.
-
Prioritize High-Risk Areas: Focus on high-risk areas where the implementation of engineering controls can significantly impact safety.
Design and Modify Equipment
-
Guarding: Install physical guards on machinery to prevent contact with moving parts. This can include fixed barriers, interlocked guards, and adjustable shields.
-
Ventilation Systems: Implement local exhaust ventilation (LEV) systems to control airborne contaminants such as dust, fumes, and vapors. General ventilation systems can also help maintain air quality.
-
Noise Control: Reduce noise levels using engineering solutions, such as soundproofing materials, quieter machinery, and vibration-dampening techniques.
-
Automation: Where feasible, automate hazardous processes to reduce human exposure. Robotics and automated systems can perform tasks that would otherwise be dangerous for workers.
Modify Work Environment
-
Ergonomic Design: Redesign workstations and tools to improve ergonomics, reducing the risk of musculoskeletal disorders. This includes adjustable workstations, anti-fatigue mats, and tools designed to minimize strain.
-
Safe Layout: Design the workplace layout to enhance safety. This might involve creating clear pathways, installing proper lighting, and ensuring emergency exits are easily accessible.
Implement Engineering Controls
-
Installation: Properly install the engineering controls, ensuring they are integrated into the workplace without disrupting operations. Work with qualified professionals to ensure that installations meet safety standards.
-
Testing and Commissioning: Test the engineering controls to verify their effectiveness after installation. Make necessary adjustments to optimize performance and ensure that they function as intended.
-
Maintenance and Monitoring
-
Regular Inspections: Regularly inspect and maintain engineering controls to ensure they remain effective. This includes checking for wear and tear, recalibrating systems, and replacing components.
-
Performance Monitoring: Continuously monitor the performance of engineering controls. Use sensors, alarms, and other monitoring tools to detect failures or inefficiencies.
Employee Training and Involvement
-
Training Programs: Train employees on engineering controls' purpose and proper use. Ensure they understand how to operate and maintain these controls correctly.
-
Feedback and Reporting: Encourage employees to report any issues or suggestions related to engineering controls. Their feedback can help identify areas for improvement and ensure that controls remain effective.
Continuous Improvement
-
Review and Update: Regularly update engineering controls to incorporate new technologies and methodologies. Stay informed about advancements in safety engineering and best practices.
-
Incident Analysis: After any incident, analyze what happened and determine if additional or improved engineering controls could prevent similar occurrences.
Organizations can significantly reduce the risk of accidents and injuries by focusing on designing and modifying equipment and work environments.
Examples of Engineering Controls
Imagine the installation of machine guards in a manufacturing facility to prevent accidental contact with moving parts or implementing local exhaust ventilation systems to remove harmful fumes from the air.
These modifications aim to redesign the work environment for enhanced safety.
Level 4: Administrative Controls
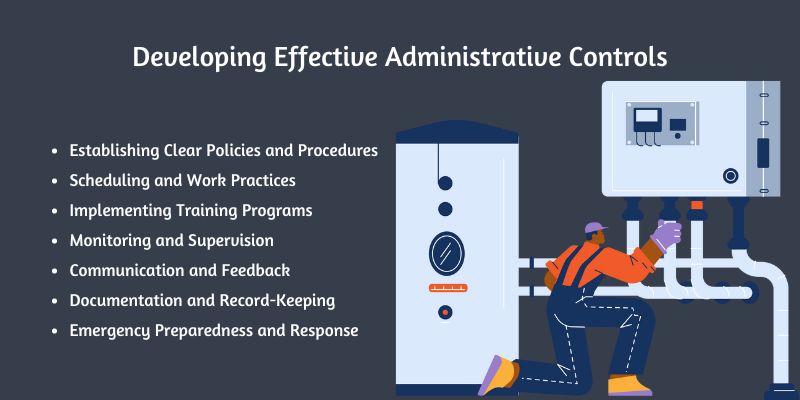
Administrative controls are policies, procedures, and practices designed to reduce exposure to hazards.
When combined with other control measures, they are crucial in creating a safer work environment.
Let’s explore how to develop and implement adequate administrative controls, with a strong emphasis on training.
Establishing Clear Policies and Procedures
-
Written Procedures: Develop clear, written procedures for all tasks and processes, especially those involving potential hazards. This includes step-by-step instructions and safety protocols.
-
Standard Operating Procedures (SOPs): Create SOPs for routine and non-routine tasks, ensuring they are easily accessible to all employees. Regularly review and update these documents to reflect any changes in processes or regulations.
Scheduling and Work Practices
-
Work Schedules: Implement work schedules that minimize exposure to hazards. This might include rotating workers to limit time spent in hazardous areas or scheduling high-risk tasks during times of low activity.
-
Rest Breaks: Ensure that workers take regular rest breaks to prevent fatigue, which can increase the risk of accidents.
Implementing Training Programs
-
Initial Training: Provide comprehensive hazard recognition training to new employees on workplace hazards, safety procedures, and emergency protocols. Ensure they understand the importance of following safety guidelines.
-
Ongoing Training: Conduct regular training sessions to update all employees on new hazards, procedures, and safety regulations. Use various training methods, such as classroom instruction, hands-on practice, and e-learning modules.
-
Refresher Courses: Schedule periodic refresher courses to reinforce key safety concepts and practices. This helps to keep safety knowledge current and top-of-mind for all employees.
-
Specialized Training: Provide specialized training for tasks that require specific safety measures, such as working with hazardous materials, operating heavy machinery, or entering confined spaces.
Monitoring and Supervision
-
Active Supervision: Ensure supervisors monitor work practices and adhere to safety procedures. This includes regular walkthroughs, spot checks, and direct observation.
-
Behavioral Safety Programs: Implement programs that focus on safe behavior. Recognize and reward employees who follow safety procedures and are committed to workplace safety.
Communication and Feedback
-
Safety Meetings: Hold regular safety meetings to discuss hazards, incidents, and improvements. Encourage open communication and participation from all employees.
-
Feedback Mechanisms: Establish channels for employees to provide feedback on safety practices and report hazards. This can include suggestion boxes, safety hotlines, or digital reporting systems.
-
Incident Reporting: Develop a straightforward procedure for reporting incidents and near-misses. Analyze reports to identify patterns and areas for improvement.
Documentation and Record-Keeping
-
Training Records: Maintain accurate records of all training sessions, including attendance and content covered. This helps track compliance and identify any gaps in training.
-
Incident Logs: Keep detailed logs of all safety incidents, including near-misses. Use this data to identify trends and develop targeted interventions.
-
Inspection Reports: Document findings from safety inspections and audits. Use these reports to track the implementation of corrective actions.
Emergency Preparedness and Response
-
Emergency Plans: Develop and implement comprehensive emergency response plans. Ensure all employees know these plans and their roles in an emergency.
-
Drills and Exercises: Conduct regular emergency drills and exercises to test the effectiveness of emergency plans and improve response times.
Combining these measures with engineering controls and other safety strategies creates a comprehensive approach to hazard management, protecting employees and improving overall workplace safety.
Examples of Administrative Controls
Implementing training programs to educate workers about potential hazards, establishing clear protocols for specific tasks, and organizing regular safety meetings fall under administrative controls. These measures aim to create awareness and foster a workplace safety culture.
Level 5: Personal Protective Equipment (PPE)
.jpg)
Personal Protective Equipment (PPE) serves as the last line of defense in the hierarchy of controls, protecting workers from residual hazards that cannot be eliminated, substituted, or controlled through engineering and administrative measures.
Selecting appropriate PPE is crucial for ensuring worker safety and compliance with regulations.
Hazard Assessment
-
Identify Hazards: Conduct a thorough hazard assessment to identify all potential risks in the workplace. This includes physical, chemical, biological, and ergonomic hazards.
-
Evaluate Exposure: Determine the level of exposure to each identified hazard. Assess the severity and likelihood of exposure to ensure the PPE selected provides adequate protection.
Types of PPE
-
Head Protection: Helmets and hard hats protect against head injuries from falling objects, bumps, and electrical hazards.
-
Eye and Face Protection: Safety glasses, goggles, and face shields protect against chemical splashes, flying debris, and radiant energy from welding or cutting operations.
-
Hearing Protection: Earplugs and earmuffs reduce the risk of hearing loss from high noise levels.
-
Respiratory Protection: Masks and respirators protect against inhalation of harmful dust, fumes, vapors, and gases.
-
Hand Protection: Gloves protect against cuts, abrasions, chemical exposure, and extreme temperatures.
-
Foot Protection: Safety boots and shoes protect against impacts, punctures, chemical exposure, and electrical hazards.
-
Body Protection: Coveralls, vests, and suits protect against chemical splashes, heat, and radiation.
-
Fall Protection: Harnesses and lanyards protect against falls from heights.
Selection Criteria
-
Suitability for the Task: Ensure the PPE is appropriate for the specific task and environment. For instance, gloves suitable for chemical handling might differ from those needed for handling sharp objects.
-
Fit and Comfort: Proper fit is essential for effectiveness. Ill-fitting PPE can cause discomfort and reduce the likelihood of consistent use. Conduct fit tests and provide a range of sizes to accommodate all employees.
-
Compliance with Standards: Ensure the selected PPE complies with relevant safety standards and regulations, such as those set by OSHA (Occupational Safety and Health Administration) or CCOHS (Canadian Centre for Occupational Health and Safety).
-
Durability and Maintenance: Choose PPE that is durable and easy to maintain. Regularly inspect, clean, and replace PPE as needed to ensure it remains effective.
-
Proper Use: Train employees on the correct use of PPE, including how to don, doff, adjust, and wear it properly. Demonstrate the correct procedures and provide hands-on practice.
-
Maintenance and Storage: Educate workers on maintaining and storing PPE correctly. Proper maintenance extends the life of PPE and ensures it provides adequate protection.
-
Limitations of PPE: Make employees aware of the limitations of their PPE. They should understand that PPE does not eliminate hazards but reduces the risk of injury.
Monitoring and Enforcement
Regular inspections ensure PPE is used correctly and in good condition. Look for signs of wear and tear that could compromise safety.
-
Compliance Checks: Enforce compliance with PPE policies through regular monitoring and disciplinary actions if necessary. Encourage a safety culture where PPE use is a standard practice.
-
Feedback and Improvement: Solicit feedback from employees on the comfort and functionality of their PPE. Use this feedback to make improvements and address any concerns.
Organizations can significantly reduce the risk of injuries by conducting thorough hazard assessments, choosing PPE that fits well and meets safety standards, and educating employees on its correct use and maintenance.
Implementing the Hierarchy of Controls in the Workplace
Practical training and hazard communication strategies are essential to successfully implement the hierarchy of controls safety in the workplace. This involves educating employees about the different control levels and fostering a culture where safety is a shared responsibility.
Regular communication channels, such as safety meetings and toolbox talks, play a crucial role in reinforcing the importance of adhering to control measures.
Training and Communication Strategies

Practical hazard recognition training and communication strategies are pivotal in implementing the hierarchy of controls safety within the workplace.
Employee education is crucial, involving comprehensive training programs to ensure a thorough understanding of the different control levels and their applications.
Regular toolbox talks and safety meetings provide opportunities for open communication, addressing questions, and reinforcing safety messages.
Here are some of the training that can help the workers ascertain their safety at the workplace:
-
Benzene Awareness Program
-
H2S Training Course
-
Aerial Lift Training
-
Fall Arrest Training
-
Lockout Tagout Training
-
Confined Space Awareness Training
Establishing clear communication channels, both visual and digital, further ensures that employees are well-informed about control measures, updates to safety protocols, and any changes in the workplace that may impact safety.
Integrating the hierarchy of controls into daily practices and encouraging proactive safety approaches contribute to creating a safety-conscious work culture.
Implementing feedback mechanisms allows organizations to gather insights from employees, facilitating continuous improvement and refinement of safety protocols.
Steps to Assess and Prioritize Controls
Assessing and prioritizing controls is crucial in implementing the hierarchy of controls safety. This involves a comprehensive examination of hidden workplace hazards, identification and evaluation of risks, and consideration of the feasibility of control measures.
Through a systematic approach, organizations can prioritize interventions based on their effectiveness in addressing specific hazards. This step ensures a targeted and focused implementation of control measures, maximizing the impact of safety efforts.
Creating a Comprehensive Safety Plan
Creating a comprehensive safety plan involves integrating the principles of the hierarchy of controls safety into the broader safety framework of the organization.
This includes developing written procedures, establishing incident reporting and emergency response protocols, and regularly reviewing and updating the plan.
WHMIS certification is a crucial component of this safety plan, ensuring that employees are equipped with the knowledge and skills to handle hazardous materials safely.
By incorporating a hierarchy of controls safety into safety protocols, organizations can create a resilient and proactive approach to mitigating risks, fostering a safer and healthier work environment.
FAQs
How do I determine which control measures to use?
To determine which control measures to use, conduct a thorough hazard assessment, evaluate the severity and likelihood of each hazard, and apply the hierarchy of controls, prioritizing elimination, substitution, engineering controls, administrative controls, and PPE in that order.
What are the challenges of using the Hierarchy of Controls?
Challenges of using the Hierarchy of Controls include balancing cost and feasibility, overcoming resistance to change, and ensuring each control measure's effectiveness and proper implementation.
Conclusion
The hierarchy of controls safety guides organizations toward creating safer and healthier workplaces as it helps the workers understand how to control and handle hazardous material.
As we've explored the complexities of this systematic approach, it becomes evident that the success of its implementation lies in a holistic strategy that encompasses training, communication, assessment, and planning.
Training and communication strategies emerge as the basis of success, ensuring that employees are aware of the hierarchy of controls safety and actively engaged in its application.
Regular toolbox talks, safety meetings, and clear communication channels facilitate a safe and secure workplace culture.
The steps to assess and prioritize controls bring a pragmatic dimension to the hierarchy of controls safety, grounding it in the specific realities of the workplace. This systematic evaluation allows organizations to tailor control measures to address the most pressing hazards effectively.
By doing so, they optimize their efforts, focusing resources where they can make the most significant impact.
Organizations implementing the hierarchy of controls safety pave the way for a culture where safety isn't just a priority – it's a shared value. The result is a workplace where employees thrive, confident in the knowledge that their well-being is a paramount concern.