In the dynamic landscape of today's workplaces, prioritizing safety performance is not just a legal requirement but a fundamental responsibility.
Ensuring the well-being of employees is a shared commitment that goes beyond compliance, contributing to a thriving and productive work environment.
The importance of safety performance cannot be overstated. It directly impacts employees' physical and mental health, boosts morale, and enhances overall productivity.
A workplace with a strong safety culture fosters trust and loyalty among its team members, creating a sense of security that encourages collaboration and innovation.
This article is a guide on how to improve safety performance, offering practical insights and actionable strategies.
Whether you are an employer aiming to enhance safety protocols or an employee seeking ways to contribute to a safer workplace, this resource is designed to empower you with valuable information.
We will explore various facets of safety performance improvement, including understanding key safety metrics, implementing leading indicators, and fostering a safety culture through training and communication.
The article aims to provide accessible and straightforward advice, ensuring the principles discussed can be applied across diverse industries and organizational structures.
By the end of this guide, you will have gained valuable insights into creating a safer, healthier, and more resilient work environment.
Whether you are taking the first steps toward improving safety performance or refining existing practices, this resource is tailored to help you navigate toward a safer and more secure workplace for everyone.
Understanding Current Safety Performance
It's crucial to grasp the current state of safety performance in enhancing workplace safety. This involves a comprehensive evaluation through various methods.
Conducting Safety Audits and Assessments

Safety audits and assessments are fundamental tools for evaluating and enhancing safety performance in the workplace.
A safety audit systematically examines the organization's safety processes, policies, and practices. This comprehensive review aims to identify potential hazards, assess the effectiveness of existing safety measures, and ensure compliance with regulatory standards.
During safety assessments, trained professionals evaluate various aspects, including physical work environments, equipment conditions, and employee behaviors.
Organizations can proactively address safety gaps, implement corrective actions, and create a safer working environment by conducting these assessments.
The insights gained from audits and assessments empower organizations to make informed decisions about resource allocation and prioritize areas for improvement.
Analyzing Incident Reports and Trends
Analyzing incident reports and trends is a crucial component of improving safety performance. Incident reports provide valuable information about workplace accidents, near misses, and injuries.
By thoroughly examining these reports, organizations can identify patterns, root causes, and contributing factors compromising safety.
Trends in incident data reveal recurring issues or emerging risks that need attention. This analysis informs targeted interventions, training programs, and safety measures to prevent the recurrence of incidents.
Moreover, understanding trends allows organizations to adapt their safety protocols to evolving challenges, fostering a proactive safety culture.
Identifying Areas of Concern
Identifying areas of concern involves a proactive approach to recognizing potential safety hazards and vulnerabilities within the organization. This may include specific departments, types of work activities, or environmental conditions that pose increased risks.
Through thorough analysis and risk assessment, organizations can allocate resources strategically, implement targeted safety measures, and prioritize interventions based on the level of risk.
By addressing these areas of concern, organizations take significant steps toward creating a safer work environment, reducing accidents, and improving overall safety performance.
This proactive identification and mitigation of risks contribute to a culture of continuous improvement in workplace safety.
Improving Safety Performance at the Workplace
Ensuring and enhancing safety performance in the workplace is a multi-step process that involves various strategies and initiatives. It requires a concerted effort from management and employees to create a safety culture and continually improve safety standards.
This section explores critical aspects of this improvement process.
Establishing a Safety Culture

Establishing a safety culture within an organization is essential to improving safety performance. A safety culture is more than just a set of rules and procedures; it represents a shared mindset and commitment to prioritizing safety at all levels.
Leadership plays a crucial role in cultivating this culture by setting an example and communicating the importance of safety. When safety becomes a core value, employees are more likely to internalize safe practices and integrate them into daily activities.
A strong safety culture encourages open communication and collaboration among team members. It creates an environment where employees feel comfortable reporting safety concerns, near misses, or potential hazards without fear of reprisal.
This proactive approach allows organizations to address issues before they escalate, contributing to a safer work environment.
Moreover, a safety culture emphasizes continuous improvement. It involves regularly evaluating and updating safety protocols based on lessons learned from incidents or near misses.
By fostering a culture of learning and adaptability, organizations can stay ahead of emerging safety challenges and continually enhance their safety performance.
Training and Education
Training and education are cornerstones of any effective safety improvement strategy. Ensuring that employees receive comprehensive safety training is vital for equipping them with the knowledge and skills to perform their tasks safely.
Training programs should cover various topics, including hazard identification, proper use of personal protective equipment (PPE), emergency response procedures, and adherence to safety protocols.
Continuous education is equally important to inform employees about evolving safety standards, best practices, and industry-specific regulations. Regular safety awareness campaigns and ongoing discussions further reinforce the importance of safety in the workforce.
By investing in training and education, organizations empower employees to contribute actively to a safer work environment.
Canada Safety Training offers some of the most comprehensive training programs. Here are some of them:
-
Fire Extinguisher Training
-
Hazard Recognition Training
-
Accident and Incident Investigation Training
-
Confined Space Awareness Training
-
Lockout Tagout Training
-
H2S Training Course
-
PPE Training
Enroll in these training sessions to become familiar with workplace hazards and learn how to prevent and manage them better!
Implementing Robust Safety Policies
Implementing robust safety policies is a foundational element in improving organizational safety performance. Safety policies are comprehensive documents outlining the specific safety procedures, rules, and expectations employees must follow.
These policies serve as a roadmap for creating a safe working environment and provide clear risk mitigation guidelines.
Effective safety policies should be tailored to the specific nature of the work conducted by the organization. They cover various aspects, including hazard identification, emergency response procedures, proper use of equipment, and protocols for reporting incidents.
Regularly reviewing and updating safety policies is essential to ensure they remain relevant and aligned with evolving industry standards and regulations.
Clear communication is critical to the successful implementation of safety policies. Organizations must ensure that all employees are familiar with the content of these policies, understand their importance, and receive adequate training to comply with them.
This involves incorporating safety policy discussions into orientation programs for new hires and conducting regular refresher courses for existing staff.
Implementing Safety Management Systems
Safety Management Systems (SMS) provide a systematic approach to managing organizational safety.
An SMS is a comprehensive framework that integrates safety policies, procedures, and risk management processes. It involves continuous monitoring, analysis, and improvement of safety performance to prevent incidents and enhance overall safety.
The implementation of an SMS typically involves several key components, including:
-
Policy and Planning: Establishing safety objectives, developing safety policies, and planning to integrate safety measures into daily operations.
-
Safety Risk Management: Identifying potential hazards, assessing risks, and implementing controls to mitigate or eliminate those risks.
-
Safety Assurance: Monitoring and evaluating safety performance, conducting safety audits and assessments, and ensuring compliance with safety standards.
-
Safety Promotion: Fostering a safety culture through training, communication, and promoting employee involvement in safety initiatives.
By adopting a Safety Management System, organizations with integrated online WHMIS training can systematically address safety concerns, identify areas for improvement, and enhance their overall safety performance.
SMS provides a proactive and structured approach to managing safety, emphasizing continuous learning and adaptation to emerging safety challenges.
Encouraging Incident Reporting

Encouraging incident reporting is a crucial aspect of improving safety performance in the workplace. An effective reporting system is an early warning mechanism, allowing organizations to identify and address potential hazards before they escalate into more significant incidents.
Creating a culture that values and encourages incident reporting fosters transparency and continuous improvement.
Employees must feel confident that reporting incidents, near misses, or unsafe conditions will not result in punitive measures. Establishing a non-punitive reporting culture promotes openness and provides valuable insights into the root causes of incidents.
Organizations can implement anonymous reporting mechanisms, confidential reporting channels, or other methods to assure employees that their concerns will be addressed constructively.
Regular communication and training programs reinforce the importance of incident reporting. Employees should be educated on the significance of reporting even minor incidents or near misses to capture valuable information that can contribute to preventive measures.
Recognition and acknowledgment of individuals who report incidents can further incentivize a proactive reporting culture.
Addressing Maintenance Issues Promptly
Addressing maintenance issues promptly is a fundamental strategy for enhancing safety performance. Malfunctioning equipment, damaged infrastructure, or overlooked maintenance needs can pose significant safety risks.
Timely identification and resolution of maintenance issues are critical to preventing accidents and ensuring the overall safety of the workplace.
Organizations should establish a robust maintenance management system that includes regular inspections, preventive maintenance schedules, and a prompt response to reported issues.
This system should cover all aspects of the workplace, including machinery, electrical systems, facilities, and other critical components.
Employee involvement plays a crucial role in addressing maintenance issues. Frontline workers are often the first to notice signs of wear and tear or malfunctioning equipment.
Creating a culture where employees are encouraged to report maintenance concerns promptly can contribute to early interventions and prevent potential safety incidents.
Regular training programs for maintenance personnel can enhance their skills in identifying, assessing, and addressing maintenance issues.
Additionally, organizations can leverage technology, such as predictive maintenance tools and monitoring systems, to proactively identify potential issues before they result in equipment failure or safety hazards.
Evaluating and Improving Emergency Response Procedures

Evaluating and continuously improving emergency response procedures is a crucial element of enhancing safety performance in the workplace.
While prevention is critical, having effective emergency response measures is equally important to mitigate the impact of unforeseen incidents.
Regular assessments and drills of emergency response procedures are essential to identify areas for improvement. This includes evaluating the response time, the effectiveness of communication systems, and the coordination among different response teams.
Organizations can simulate various emergency scenarios to ensure employees are well-prepared to handle real-life situations.
After each assessment, gathering feedback from participants and stakeholders involved in emergency response is vital. This feedback loop provides valuable insights into the strengths and weaknesses of the existing procedures.
It also offers an opportunity to incorporate lessons from past incidents or near misses, enabling organizations to adapt and improve their emergency response protocols.
Technological advancements, such as simulation software and virtual reality training, can enhance the realism of emergency response drills.
These tools allow organizations to create immersive training experiences, helping employees develop the skills to respond effectively to emergency scenarios.
Acknowledging and Rewarding Safe Practices
Acknowledging and rewarding safe practices is a positive reinforcement strategy that can significantly improve workplace safety performance.
Recognizing employees for their commitment to safety creates a culture where safe behaviors are expected and celebrated.
Organizations can implement various recognition programs to highlight and reward individuals or teams that consistently prioritize safety. This could include safety awards, certificates, or public acknowledgment during team meetings.
Tangible rewards, such as gift cards or bonus incentives, can motivate employees to engage in safe practices actively.
Leadership plays a crucial role in fostering a culture of recognition. When leaders consistently acknowledge and reward safe behaviors, it sends a powerful message that safety is a top priority.
This, in turn, encourages other team members to follow suit and actively contribute to the overall safety culture.
Furthermore, integrating safety recognition into performance evaluations and key performance indicators (KPIs) reinforces the importance of safety as a fundamental aspect of job performance.
By aligning safety achievements with professional growth and advancement, organizations can incentivize employees to prioritize safety in their daily activities.
Incident Investigation and Analysis
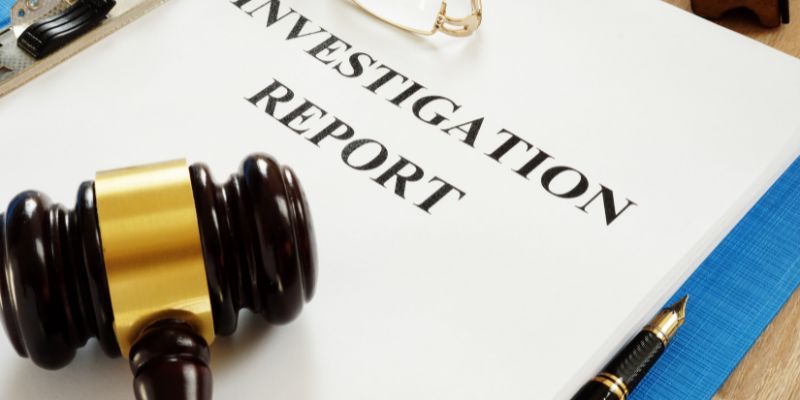
Incident investigation and analysis are critical processes in improving safety performance. They help organizations understand the root causes of accidents and incidents, enabling them to prevent future occurrences.
By systematically examining the circumstances of an incident, companies can identify underlying issues and implement corrective actions to enhance workplace safety.
Importance of Incident Investigation
The primary goal of incident investigation is to prevent recurrence. When an incident occurs, it is essential to investigate it thoroughly, regardless of whether it resulted in injury, property damage, or a near miss.
Each incident provides valuable information about potential hazards and weaknesses in safety procedures.
Understanding these factors helps develop strategies to mitigate risks and improve overall safety performance.
Steps in Conducting an Incident Investigation
- Immediate Response and Secure the Scene: The first step after an incident is to ensure the safety of all personnel and secure the area to prevent further harm. This involves providing medical assistance and isolating the scene to preserve evidence.
- Form an Investigation Team: An investigation team should be assembled, including representatives from safety, management, and workers with knowledge of the area and processes involved. Having a diverse team ensures a comprehensive analysis.
- Collect Information: Gathering information is crucial for understanding the incident. This includes:
- Witness statements: Interviewing those involved and any bystanders to get their accounts of what happened.
- Physical evidence: Examining the scene for evidence such as equipment, materials, and environmental conditions.
- Documentation: Reviewing relevant documents like maintenance records, safety protocols, and training logs.
- Analyze the Data: The collected data should be analyzed to identify the events leading to the incident. This involves looking at:
- Immediate causes: The direct actions or conditions that led to the incident.
- Root causes: Underlying factors that contributed to the incident, such as inadequate training, poor maintenance, or systemic issues in safety management.
- Determine Corrective Actions: The investigation team should recommend corrective actions to address the identified root causes based on the analysis. These actions may include:
- Revising safety procedures and protocols.
- Implementing additional training programs.
- Improving maintenance schedules.
- Enhancing communication and reporting mechanisms.
- Implement and Monitor Corrective Actions: Once corrective actions are identified, they must be implemented promptly. This requires assigning responsibilities, setting timelines, and ensuring resources are available. Monitoring the effectiveness of these actions is essential to ensure they have the desired impact on safety performance.
- Continuous Improvement and Learning: Incident investigation and analysis should be part of a broader safety management system focused on continuous improvement. Lessons learned from incidents should be communicated across the organization to prevent similar occurrences in other areas.
Understanding how to conduct a workplace investigation can help you know what steps to take after an incident.
Benefits of Effective Incident Investigation
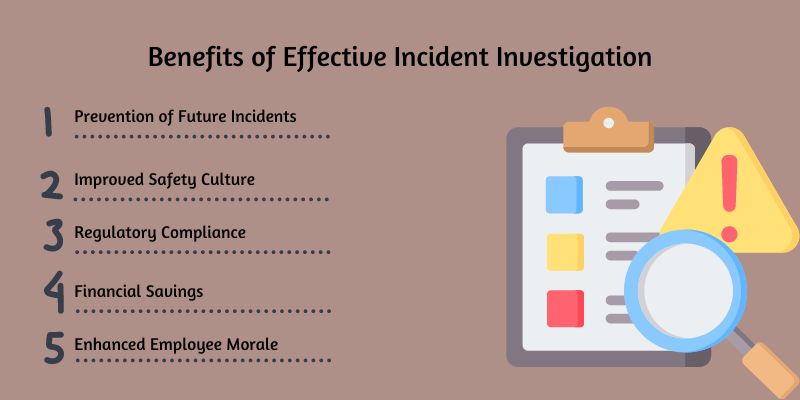
- Prevention of Future Incidents: Organizations can prevent similar incidents by identifying and addressing root causes, reducing the likelihood of injuries and property damage.
- Improved Safety Culture: A thorough investigation process demonstrates a commitment to safety, encouraging employees to report hazards and participate in safety programs.
- Regulatory Compliance: Proper incident investigation and documentation help organizations comply with regulatory requirements, avoiding fines and legal issues.
- Financial Savings: Preventing incidents reduces medical expenses, compensation claims, and lost productivity costs.
- Enhanced Employee Morale: Employees feel safer and more valued when they see that their organization is committed to addressing safety concerns.
Incident investigation and analysis are vital tools for improving safety performance in the workplace.
By systematically examining the causes of incidents and implementing corrective actions, organizations can prevent future occurrences, enhance their safety culture, and ensure regulatory compliance.
Safety Monitoring and Reporting Tools
Safety monitoring and reporting tools are crucial in enhancing workplace safety and improving safety performance. These tools provide a systematic way to track, analyze, and report safety-related incidents, hazards, and near misses.
By utilizing technology and structured processes, organizations can gain valuable insights into their safety practices, identify areas for improvement, and foster a proactive safety culture.
Here, we delve into the importance of these tools and how they can be effectively utilized.
Importance of Safety Monitoring and Reporting Tools
Safety monitoring and reporting tools are essential for several reasons:
- Real-time Data Collection: These tools enable the collection of real-time data on safety incidents, hazards, and near misses. This timely information is critical for immediate response and mitigation, helping to prevent minor issues from escalating into major incidents.
- Improved Accuracy and Consistency: Automated tools ensure data is collected consistently and accurately. This reduces the chances of human error and provides a reliable basis for analysis and decision-making.
- Enhanced Analysis and Insights: Advanced reporting tools can analyze large volumes of data to identify trends, patterns, and root causes of safety incidents. This helps organizations to understand the underlying factors contributing to safety issues and develop targeted interventions.
- Regulatory Compliance: Many industries are subject to stringent safety regulations. Monitoring and reporting tools help organizations maintain compliance by ensuring all incidents are documented, reported, and investigated according to regulatory requirements.
- Proactive Safety Management: Organizations can adopt a proactive approach to safety management by continuously monitoring safety metrics and analyzing data. This involves identifying potential hazards and implementing preventive measures before incidents occur.
Key Features of Safety Monitoring and Reporting Tools
- Incident Reporting Systems: These systems allow employees to report safety incidents, hazards, and near misses quickly. They typically include user-friendly interfaces, mobile applications, and anonymous reporting options to encourage participation.
- Data Analytics and Dashboards: Advanced analytics tools can process and visualize safety data, providing dashboards and reports highlighting key safety metrics. These insights help management make informed decisions and prioritize safety initiatives.
- Automated Alerts and Notifications: Monitoring tools can send automated alerts and notifications to relevant personnel when safety incidents are reported. This ensures a swift response to emerging issues and helps mitigate risks promptly.
- Risk Assessment Modules: Some tools include modules for conducting risk assessments. These modules guide users through identifying hazards, evaluating risks, and implementing control measures.
- Integration with Other Systems: Effective safety monitoring tools can integrate with other systems, such as HR, maintenance, and compliance software. This integration provides a holistic view of safety performance and streamlines data management.
Best Practices for Implementing Safety Monitoring and Reporting Tools
- Select the Right Tool: Choose a tool that meets your organization's needs. Consider factors such as ease of use, scalability, integration capabilities, and support services.
- Train Employees: Provide comprehensive training on using the reporting tools. Ensure they understand the importance of reporting incidents and how to use the system effectively.
- Encourage a Reporting Culture: Foster a culture where employees feel comfortable reporting safety incidents and hazards without fear of retribution. Encourage transparency and emphasize the role of reporting in improving workplace safety.
- Review and Analyze Data regularly: Review the data collected by the monitoring tools regularly to identify trends and patterns. Use this information to develop and implement targeted safety interventions.
- Update and Maintain the System: Continuously update and maintain the monitoring tools to ensure they remain effective. This includes regularly updating software, training new employees, and refining reporting processes based on feedback.
- Use Data for Continuous Improvement: Use the insights from data analysis to drive continuous improvement in safety practices. Implement corrective actions, review their effectiveness, and make adjustments to improve workplace safety.
Benefits of Safety Monitoring and Reporting Tools
- Enhanced Safety Performance: These tools help organizations improve their safety performance, reduce incidents, and create a safer work environment by providing real-time data and insights.
- Increased Accountability: Automated reporting systems increase accountability by documenting and addressing safety incidents. This transparency helps build trust and accountability among employees.
- Better Resource Allocation: Data-driven insights enable organizations to allocate resources more effectively. For example, they can prioritize safety training, maintenance activities, and safety interventions based on identified risks.
- Improved Employee Engagement: When employees see that their reports are taken seriously and lead to tangible improvements, they are more likely to engage with safety programs and contribute to a positive safety culture.
- Cost Savings: Proactive safety management can prevent incidents and reduce their severity, leading to significant cost savings by avoiding medical expenses, compensation claims, and downtime.
By implementing these tools and following best practices, organizations can enhance their safety performance, comply with regulatory requirements, and build a culture of safety that protects employees and promotes organizational success.
Safety in Physical Layout and Design
Ensuring safety through a workplace's physical layout and design is critical to maintaining a secure and efficient environment.
The organization of space, choice of materials, and overall design can significantly influence the safety and well-being of employees.
A well-planned physical layout can prevent accidents, reduce hazards, and promote a smoother workflow.
Here's an in-depth look at the key considerations and strategies for achieving safety in physical layout and design.
Importance of Physical Layout and Design
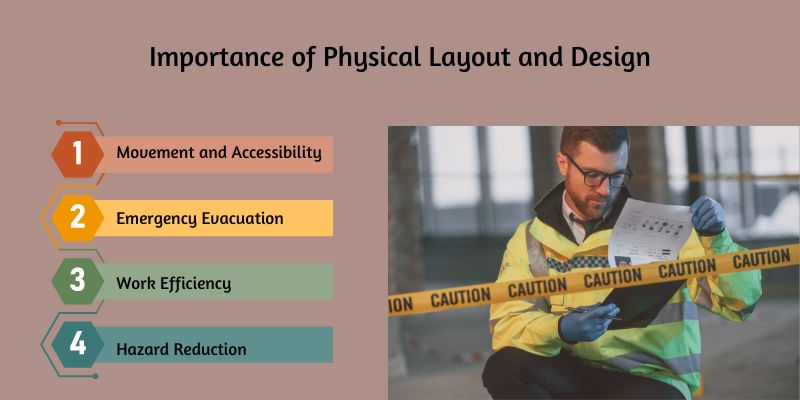
The physical layout and design of a workplace impact several crucial factors, including:
- Movement and Accessibility: A well-designed layout ensures that pathways are clear and employees can move around safely and efficiently, reducing the risk of trips, slips, and falls.
- Emergency Evacuation: A clear and logical layout ensures that employees can evacuate quickly and safely. Well-marked exits, wide pathways, and easily accessible emergency equipment are essential.
- Work Efficiency: A thoughtfully arranged space enhances productivity by minimizing unnecessary movement and making it easier for employees to access tools and materials.
- Hazard Reduction: Identifying and mitigating potential hazards through design, such as proper ventilation, adequate lighting, and appropriate placement of machinery and equipment, significantly improves safety.
Critical Considerations for Safety in Physical Layout and Design
- Clear Pathways and Traffic Flow: Design the layout to ensure pathways are wide and free from obstructions. This includes keeping aisles clear and ensuring that doors and exits are easily accessible. To prevent collisions, designate specific routes for different types of traffic, such as forklifts and pedestrians.
- Proper Lighting: Adequate lighting is crucial for visibility and safety. Ensure all work areas, corridors, and emergency exits are well-lit. Use natural light where possible and supplement with artificial lighting that does not cause glare or shadows.
- Ventilation and Air Quality: Good ventilation helps maintain air quality, preventing the buildup of harmful substances and ensuring a comfortable environment. This is especially important in areas with chemicals, dust, or fumes. Use appropriate ventilation systems and ensure regular maintenance.
- Ergonomic Design: Ergonomics play a significant role in preventing injuries and improving comfort: design workstations and equipment to minimize strain and repetitive movements. Adjustable chairs, desks, and proper tool placement can reduce the risk of musculoskeletal disorders.
- Material Selection: Choose safe, durable, and appropriate materials for the work environment. Non-slip flooring, fire-resistant materials, and easy-to-clean surfaces create a safer workplace. Avoid materials that can cause allergies or are hazardous.
- Emergency Equipment and Signage: Install emergency equipment, such as fire extinguishers, first aid kits, and eye wash stations, in inaccessible locations. Use clear and visible signage to indicate the location of emergency exits, equipment, and assembly points.
- Separation of Hazardous Areas: Designate and isolate areas with specific risks, such as chemical storage or machinery operation zones. Use barriers, signage, and restricted access to keep employees safe from these hazards.
- Noise Control: Excessive noise can lead to hearing loss and increased stress levels. Use sound-absorbing materials, barriers, and proper equipment maintenance to control noise levels. Design quiet areas for breaks and concentration tasks.
Strategies for Implementing Safety in Physical Layout and Design
- Conduct a Risk Assessment: Conduct a thorough risk assessment before designing or rearranging a workplace to identify potential hazards and areas for improvement. Engage employees in this process to gain insights into their daily experiences and concerns.
- Involve Safety Experts and Designers: Collaborate with safety experts, ergonomists, and designers to create a layout that meets safety standards and enhances efficiency. Their expertise can help identify potential issues and develop practical solutions.
- Regular Review and Updates: Review the physical layout and design of the workplace regularly to ensure it meets safety standards and accommodates any changes in operations or personnel. Based on feedback and incident reports, make necessary adjustments.
- Employee Training and Awareness: Train employees to maintain a safe physical environment. Encourage them to report hazards and suggest improvements.
By focusing on these critical areas and strategies, organizations can create a safer, more efficient workplace that minimizes risks and promotes employee well-being. The physical layout and design are foundational to building a safety and operational excellence culture.
Environmental Controls
Environmental controls are crucial for maintaining a safe and healthy workplace. These controls involve managing the workplace environment to reduce or eliminate exposure to hazards.
Adequate environmental controls protect workers from harmful substances, improve comfort and productivity, and ensure compliance with health and safety regulations.
Here's an in-depth look at the critical aspects of environmental controls and their implementation.
Importance of Environmental Controls
Environmental controls are vital for several reasons:
- Health and Safety: Controlling environmental factors like air quality, temperature, and noise levels helps prevent work-related illnesses and injuries, ensuring a healthier workforce.
- Compliance: Adhering to regulations set by organizations such as OSHA (Occupational Safety and Health Administration) and EPA (Environmental Protection Agency) is mandatory. Proper environmental controls help meet these standards.
- Productivity and Comfort: A well-controlled environment enhances employee comfort and productivity. Workers are more likely to perform well when not exposed to extreme temperatures, poor air quality, or excessive noise.
Critical Components of Environmental Controls

- Air Quality Management: Use proper ventilation systems to ensure good indoor air quality. This includes HVAC (heating, ventilation, and air conditioning) systems that filter and circulate air effectively. Regularly maintaining these systems is crucial to prevent the buildup of dust, mold, and other pollutants.
- Temperature and Humidity Control: Maintain a comfortable temperature and humidity level to prevent heat stress or hypothermia. Use air conditioning, heating systems, and humidifiers/dehumidifiers as needed. Monitor and adjust settings based on seasonal changes and specific workplace requirements.
- Noise Control: Excessive noise can cause hearing loss and increase stress. Implement noise control measures such as soundproofing, using quieter machinery, and providing hearing protection. Designate quiet zones for tasks that require concentration.
- Lighting: Adequate lighting is essential for safety and productivity. Ensure that work areas are well-lit with natural and artificial light. Use diffused lighting and adjustable fixtures to avoid glare and shadows.
- Chemical Exposure Control: Manage the use and storage of hazardous chemicals to prevent exposure. Use fume hoods, exhaust systems, and proper storage containers. Ensure that Material Safety Data Sheets (MSDS) are accessible and that employees are trained in handling chemicals safely.
- Waste Management: Properly dispose of waste materials to prevent contamination and environmental damage. Implement recycling programs and ensure that hazardous waste is disposed of according to regulations.
- Pest Control: Prevent infestations by maintaining cleanliness and using pest control measures. Regular inspections and proper waste management can reduce the risk of pests.
Strategies for Implementing Environmental Controls
- Conduct Environmental Assessments: Regularly assess the workplace to identify environmental hazards. Use the findings to develop and implement control measures. Involve employees in the assessment process to gain insights and address concerns.
- Develop and Implement Policies: Establish clear policies for environmental control that outline procedures and responsibilities. Ensure these policies are communicated to all employees and regularly reviewed and updated.
- Use Engineering Controls: Implement engineering solutions such as ventilation systems, soundproofing, and ergonomic design to control environmental factors. Regular maintenance and upgrades are necessary to keep these systems effective.
- Provide Training and Awareness Programs: Train employees on the importance of environmental controls and how to use them. Raise awareness about the potential hazards and the measures to mitigate them.
- Monitor and Review: Continuously monitor environmental conditions and the effectiveness of control measures. Use sensors and monitoring equipment to track air quality, temperature, and noise levels. Review and adjust strategies based on data and employee feedback.
- Emergency Preparedness: Plan for environmental emergencies such as chemical spills, fires, or extreme weather conditions. Ensure that employees know the procedures and that necessary equipment and supplies are readily available.
Focusing on these components and strategies can help organizations create a safer, healthier, and more productive work environment. Adequate environmental controls are essential for protecting employees, ensuring regulatory compliance, and maintaining operational efficiency.
Final Words
Fostering a robust safety performance in the workplace is an ongoing commitment that requires a versatile approach.
Understanding the current safety performance through audits, assessments, and incident trend analysis provides a solid foundation for improvement initiatives. It allows organizations to pinpoint areas of concern and tailor interventions to specific needs.
Improving safety performance establishes a strong safety culture where employees create a safe work environment. Training and education initiatives ensure employees have the knowledge and skills to contribute to a safety-first mindset.
Implementing robust safety policies and management systems provides the structural framework for maintaining a safe workplace, with an added layer of effectiveness achieved through integrating online safety courses and certificates.
Addressing maintenance issues promptly, encouraging incident reporting, and continuously evaluating and improving emergency response procedures are vital components of this comprehensive strategy.
Furthermore, acknowledging and rewarding safe practices creates a positive feedback loop that reinforces the importance of safety at all levels of the organization.
By integrating safety recognition into performance evaluations and KPIs, organizations send a clear message that safety is not just a priority but an integral part of professional growth.
Organizations must embrace a continuous improvement mindset to improve safety performance. Regular assessments, feedback loops, and incorporating of technological advancements contribute to an adaptive and evolving safety strategy.
As organizations invest in the well-being of their workforce, the dividends manifest in increased productivity, reduced incidents, and an overall healthier and safer work environment.