In the competitive food industry, ensuring safety is focused on protecting the well-being of those who prepare and handle the food.
One crucial aspect of this safety mindset is WHMIS, which is short for Workplace Hazardous Materials Information System.
But what exactly is WHMIS?
WHMIS is a system designed to keep workers safe by providing necessary information about hazardous materials they may encounter on the job. This information includes labels, safety data sheets, and WHMIS training programs.
WHMIS compliance is essential in the food industry, as employees handle a variety of substances that could pose health risks if not handled properly. From cleaning chemicals to food additives, various materials fall under WHMIS regulations.
Ensuring WHMIS compliance means that workers are equipped with the knowledge and resources to identify potential hazards, understand the WHMIS symbols, take appropriate precautions, and respond effectively in emergencies.
WHMIS compliance is a crucial safeguard against accidents, injuries, and health risks in the fast-paced environment of restaurants, cafes, and food processing facilities.
By understanding and adhering to WHMIS regulations, businesses in the food industry can demonstrate their commitment to prioritizing the well-being of their employees and customers alike.
So, let's explore the importance of WHMIS compliance in the food industry and understand how businesses can ensure they're meeting these essential safety standards.
4 Common WHMIS Violations in the Food Industry
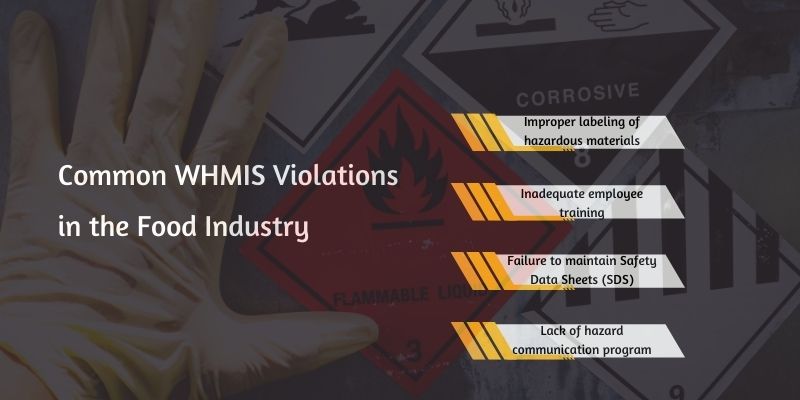
Compliance with WHMIS regulations is essential in the food industry to ensure the safety of workers and customers.
However, despite its importance, several common violations occur within this sector. Let's explore these violations in detail:
1. Improper Labeling of Hazardous Materials
One of the most common WHMIS violations in the food industry is improper labeling hazardous materials.
This includes failing to affix appropriate WHMIS labels on containers for hazardous substances, such as cleaning chemicals or food additives.
Improper labeling can lead to confusion among workers, increasing the risk of accidents or exposure to harmful substances.
2. Inadequate Employee Training
Another frequent violation is inadequate employee training on WHMIS requirements and procedures.
Many businesses in the food industry need to provide comprehensive training to their employees on identifying hazardous materials, interpreting WHMIS labels and safety data sheets, and following proper safety protocols.
With adequate WHMIS training and certification, workers may be able to handle hazardous materials safely, increasing the likelihood of accidents or injuries.
3. Failure to Maintain Safety Data Sheets (SDS)
Failure to maintain up-to-date Safety Data Sheets (SDS) is another common WHMIS violation. SDS contains crucial information about the hazards associated with specific substances and recommended safety precautions and emergency response procedures.
In the food industry, businesses must keep SDS readily accessible to employees and ensure they are regularly updated with accurate information.
Neglecting to maintain SDS can hinder workers' ability to assess risks associated with hazardous materials.
4. Lack of Hazard Communication Program
Lastly, a common WHMIS violation in the food industry is the need for a comprehensive hazard communication program.
A hazard communication program outlines how employers will communicate information about hazardous materials to their employees, including training requirements, methods for communicating hazards, labeling procedures, and SDS management.
With a well-defined hazard communication program, businesses may be able to communicate vital safety information effectively to their workforce, increasing the likelihood of accidents or incidents involving hazardous materials.
3 Consequences of WHMIS Violations
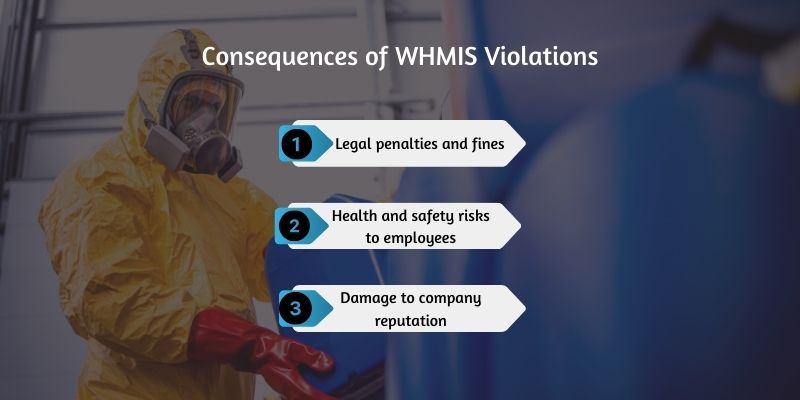
Violating WHMIS regulations can have serious repercussions for businesses operating in the food industry. Let's delve into the consequences:
1. Legal Penalties and Fines
One of the most immediate consequences of WHMIS violations is the risk of facing legal penalties and fines.
Regulatory agencies, such as Occupational Health and Safety (OHS) authorities, enforce WHMIS compliance and have the authority to issue fines and penalties to businesses found in violation of the regulations.
These fines can be substantial, depending on the severity of the violation and the jurisdiction in which the business operates. In addition to financial penalties, businesses may face legal action, injunctions, or other enforcement measures.
2. Health and Safety Risks to Employees
Another significant consequence of WHMIS violations is the increased risk of health and safety hazards to employees.
Failure to comply with WHMIS regulations means that workers may not have access to crucial information about the hazards associated with the substances they handle, leading to a greater risk of accidents, injuries, or exposure to harmful materials.
This can result in short-term health effects such as skin irritation, respiratory problems, or chemical burns, as well as long-term health issues like occupational diseases or chronic health conditions.
3. Damage to Company Reputation
WHMIS violations can tarnish a company's reputation and credibility. Customers, suppliers, and stakeholders expect businesses to prioritize safety and compliance with regulatory standards.
When a business violates WHMIS regulations, it can erode trust among customers and stakeholders, leading to a loss of business opportunities, negative publicity, and damage to the company's brand reputation.
Restoring trust and rebuilding reputation after a WHMIS violation can be challenging and time-consuming, requiring significant resources and effort from the business.
How to Avoid WHMIS Violations in the Food Industry
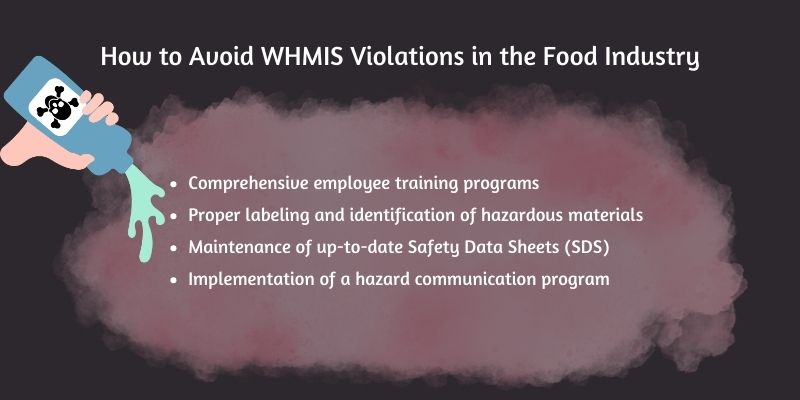
Maintaining compliance with WHMIS regulations is essential for ensuring the safety of employees and customers in the food industry. Here are key strategies to avoid WHMIS violations:
1. Comprehensive Employee Training Programs
WHMIS training is a cornerstone of compliance in the food industry. It is crucial to provide employees with comprehensive training on WHMIS requirements, procedures, and safe handling practices for hazardous materials.
WHMIS training has various benefits, as it equips employees with the knowledge and skills necessary to identify hazards, interpret WHMIS labels and Safety Data Sheets (SDS), and respond appropriately in case of emergencies.
Training should be conducted regularly, with new employees receiving training upon hire and existing employees receiving refresher training at least annually. You can find more information in our related blog if you're wondering how long WHMIS training is good for.
Training methods should be varied to accommodate different learning styles, including in-person sessions, online courses, and hands-on demonstrations.
2. Proper Labeling and Identification of Hazardous Materials
Proper labeling and identification of hazardous materials are essential to WHMIS compliance. Employers must ensure that all hazardous substances in the workplace are appropriately labeled with WHMIS-compliant labels.
These labels should include pictograms, hazard statements, and preventive measures to convey the nature of the hazards and necessary safety precautions to workers.
Additionally, employers should train employees to interpret WHMIS labels and recognize the hidden workplace hazards associated with different substances.
3. Maintenance of Up-To-Date Safety Data Sheets (SDS)
Safety Data Sheets (SDS) provide vital information about the hazards of chemicals in the workplace and the measures to be taken to ensure safety. Employers must ensure that SDS are readily accessible to employees and up-to-date with accurate information.
This includes regularly reviewing and updating SDS as necessary to reflect changes in chemical compositions, hazard classifications, or safety precautions.
Employees should be trained to access and interpret SDSs to obtain essential information about the hazards of chemicals they work with.
4. Implementation of a Hazard Communication Program
A robust hazard communication program is essential for effectively communicating information about hazardous materials in the workplace.
This program should include clear communication channels for reporting hazards, procedures for labeling and identifying hazardous materials, and protocols for emergency response.
Employers should train employees to report hazards, follow proper labeling procedures, and respond to emergencies such as spills or exposures.
Employers can implement a comprehensive hazard communication program to ensure that workers are aware of the hazards in their work environment and are equipped to handle them safely.
Final Words
Maintaining WHMIS compliance in the food industry is necessary for ensuring the safety and well-being of employees, customers, and the overall success of businesses.
By adhering to WHMIS regulations, businesses can effectively mitigate the risks of hazardous materials commonly found in food processing, handling, and preparation environments.
Comprehensive employee training programs play a vital role in WHMIS compliance, equipping workers with the knowledge and skills to safely identify, handle, and respond to hazardous materials.
By regularly reviewing and updating SDS, employers can effectively communicate important safety information to their workforce and facilitate informed decision-making.
By providing clear communication channels for reporting hazards, labeling procedures, and emergency response protocols, businesses can empower employees to play an active role in maintaining a safe and healthy work environment.
WHMIS compliance is a legal obligation. By prioritizing safety and investing in WHMIS training and hazard communication programs, businesses can create safer workplaces, protect their employees, and uphold their reputation as responsible food industry members.