Ensuring a safe workplace is a shared responsibility beyond meeting regulatory standards. It is about fostering an environment where employees feel secure, supported, and confident in their well-being. To achieve this, measuring safety in the workplace becomes a pivotal practice.
Workplace safety is not just a legal requirement but a fundamental aspect of creating a positive and productive work environment. Prioritizing safety safeguards employees from potential hazards reduces the risk of accidents. It contributes to their overall health and job satisfaction.
Beyond these immediate benefits, a commitment to safety also enhances an organization's reputation. It fosters a culture of trust and reliability.
But how do you measure safety in the workplace?
Measuring safety is not merely a formality but a proactive strategy for continuous improvement. It involves assessing, quantifying, and analyzing various safety aspects to identify strengths, weaknesses, and areas for enhancement.
The primary purpose is to prevent incidents, injuries, and illnesses by identifying potential risks and implementing effective safety measures.
This process empowers organizations to adapt to evolving circumstances, comply with regulations, and, most importantly, prioritize the well-being of their workforce.
In this blog, we will dive into the practical aspects of measuring safety in the workplace. From key performance indicators to risk assessments, we will explore the tools and strategies that organizations can employ to gauge and elevate their safety standards.
By understanding how to measure safety effectively, companies can take proactive steps towards creating a workplace where safety is not just a goal but an integral part of their identity.
Critical Metrics for Workplace Safety
Workplace safety is a critical aspect of organizational well-being. Employers strive to create and maintain a safe environment for their workers. Specific key metrics are crucial in effectively measuring and enhancing safety performance.
These metrics provide insights into the overall safety landscape of a workplace. Here are some essential critical metrics for workplace safety:
-
Incident rate
-
Severity rate
-
Lost Time Injury Frequency Rate (LTIFR)
-
Near miss reporting
These key metrics provide a comprehensive understanding of a workplace's safety performance. Regularly monitoring and analyzing these metrics enable organizations to implement targeted safety improvements, fostering a safer and healthier work environment.
1. Incident Rate
The Incident Rate is a pivotal metric in assessing workplace safety, providing organizations with a quantitative measure of how frequently workplace injuries and illnesses occur.
Calculated as the number of incidents per full-time employee over a specified period, it offers a valuable snapshot of safety performance.
Importance of Incident Rate
The Incident Rate is a critical indicator, highlighting the frequency of workplace safety incidents.
A higher incident rate implies a greater prevalence of workplace injuries or illnesses, prompting organizations to investigate the root causes and implement targeted interventions.
This metric helps companies identify trends, patterns, and areas of concern, enabling them to allocate resources and implement preventive measures effectively.
Calculation and Interpretation
To calculate the Incident Rate, the number of recordable incidents (injuries or illnesses) is divided by the total hours worked by all employees. This standardized approach allows organizations of different sizes to compare safety performance on a consistent scale.
Here is the formula for calculating the incident rate.:
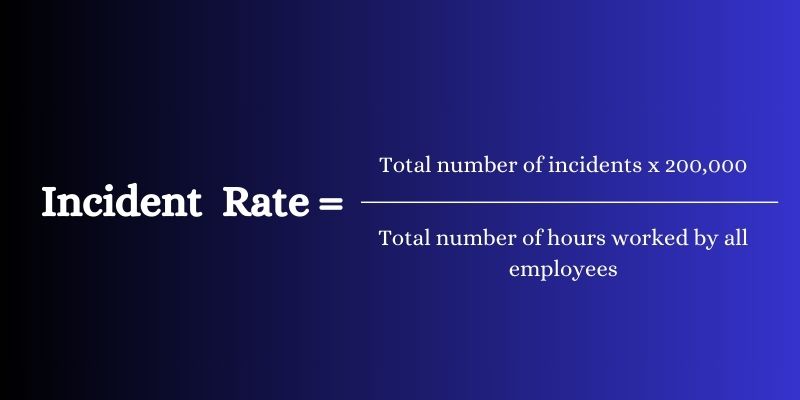
Utilization in Safety Management
Organizations leverage the Incident Rate to set benchmarks, establish safety goals, and track progress. A decreasing incident rate signifies improved safety measures and reduced workplace incidents, showcasing a commitment to fostering a safer work environment.
The Incident Rate is a foundational metric that forms the basis of a data-driven safety management approach, empowering organizations to proactively address safety challenges and promote the well-being of their workforce.
2. Severity Rate
The Severity Rate is a crucial metric in workplace safety, offering insights into the seriousness of injuries and illnesses within an organization.
Unlike the Incident Rate, which focuses on frequency, the Severity Rate dives into the severity or impact of each incident. This metric aids organizations in understanding the gravity of safety incidents and their implications for employee well-being.
Significance of Severity Rate
While the Incident Rate quantifies the number of incidents, the Severity Rate provides a more nuanced perspective by considering the days lost or the severity of the injuries.
It allows organizations to prioritize safety efforts based on the potential impact of incidents, emphasizing the importance of prevention and effective response.
Calculation and Interpretation
The Severity Rate is calculated by dividing the number of days lost due to workplace injuries or illnesses by the total number of hours worked. The formula is expressed as follows:
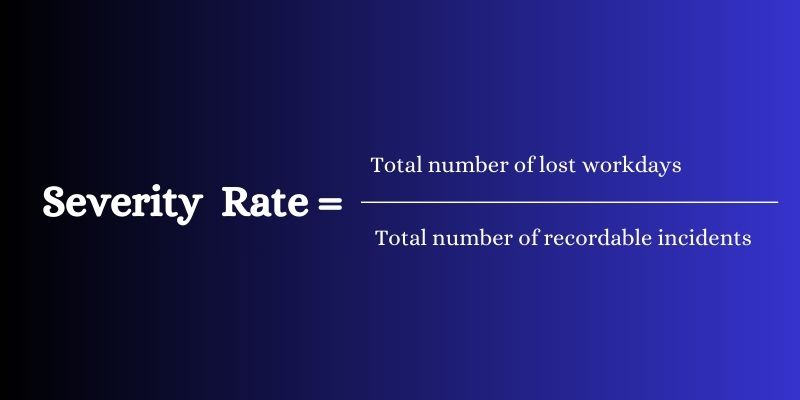
This calculation provides a rate, offering a standardized measure that facilitates comparisons across different organizations.
Application in Safety Management
Organizations leverage the Severity Rate to gain insights into the impact of workplace incidents on productivity and employee well-being.
A lower Severity Rate indicates that incidents, when they occur, result in fewer days lost, reflecting a proactive approach to managing injuries and illnesses.
This metric informs safety strategies, helping organizations prioritize measures to reduce the severity of incidents and enhance employee recovery processes.
The Severity Rate complements the Incident Rate, contributing to a comprehensive understanding of workplace safety.
By focusing on the frequency and severity of incidents, organizations can tailor safety initiatives to address specific challenges and cultivate a safer work environment.
3. Lost Time Injury Frequency Rate (LTIFR)
The Lost Time Injury Frequency Rate (LTIFR) is a critical metric organizations use to assess the frequency of workplace injuries resulting in lost workdays.
It provides valuable insights into the effectiveness of safety measures. It helps organizations identify areas for improvement in their safety programs.
LTIFR is calculated by taking the total number of lost time injuries within a specified period and dividing it by the total number of hours worked. The formula is expressed as follows:
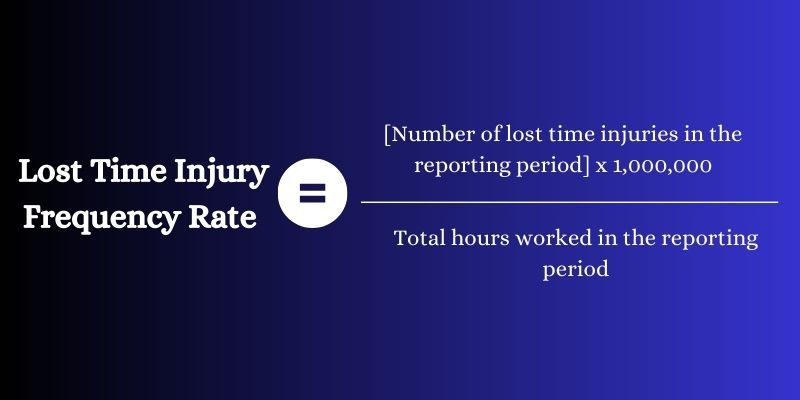
The multiplication by 1,000,000 is a standardizing factor representing the rate per one million hours worked. This standardization allows for meaningful comparisons across organizations with varying workforce sizes and working hours.
Interpretation and Significance
A higher LTIFR indicates a higher frequency of lost time injuries, suggesting that the workplace may have safety issues that need attention. Conversely, a lower LTIFR signifies a safer work environment with fewer injuries, leading to lost workdays.
Application in Safety Management
Organizations use LTIFR to track their safety performance over time and benchmark against industry standards. It helps safety professionals and management assess the impact of safety initiatives and make data-driven decisions to enhance workplace safety.
Continuous Improvement
A declining LTIFR over time is a positive indicator, suggesting that safety measures effectively prevent injuries. However, organizations must remain vigilant and continuously improve their safety programs to drive LTIFR even lower, aiming for zero lost time injuries.
LTIFR is a critical metric for organizations committed to ensuring the well-being of their workforce. Organizations can proactively address safety concerns and create a safer and healthier work environment by measuring the frequency of injuries resulting in lost workdays.
4. Near Miss Reporting
Near-miss reporting is a crucial component of workplace safety management, focusing on incidents that could have resulted in injuries, illnesses, or damage but, fortunately, did not.
It involves reporting and investigating situations where a potential hazard or unsafe condition was identified, allowing organizations to proactively address safety concerns before they escalate into more severe incidents.
A near miss is an unplanned event that, under slightly different circumstances, could have resulted in harm or damage.
Near-miss reporting encourages employees to communicate and document these incidents, fostering a safety culture that values proactive hazard identification and prevention.
Reporting Process
The near-miss reporting process typically involves:
-
Observation: Employees observe and recognize a situation that could have led to an incident.
-
Reporting: Employees report the near miss through a designated reporting system, describing the incident and the contributing factors.
-
Investigation: Safety professionals investigate the reported near misses to identify root causes and contributing factors.
-
Analysis: The organization analyzes the data collected from near-miss reports to identify trends and patterns, helping to address underlying safety issues.
Benefits of Near Miss Reporting
Here are the main benefits of near-miss reporting:
-
Proactive Hazard Identification: Near-miss reporting allows organizations to identify and address potential hazards before they result in actual harm.
-
Continuous Improvement: Analyzing near misses provides valuable insights for improving safety processes and preventing future incidents.
-
Employee Engagement: Involving employees in the reporting process fosters a sense of ownership in safety, encouraging a proactive approach to hazard prevention.
Encouraging a Reporting Culture
To enhance near-miss reporting, organizations should create a non-punitive reporting culture where employees feel comfortable reporting incidents without fear of reprisal. Communication, training, and feedback mechanisms are crucial in promoting a robust reporting culture.
Near-miss reporting is a proactive approach to enhance workplace safety by identifying and mitigating potential hazards.
Emphasizing the reporting and investigating near misses contributes to a safer work environment, fostering a culture of continuous improvement in safety practices.
How to Measure Safety in the Workplace
Measuring safety in the workplace is crucial to ensure a healthy and secure environment for employees.
Several methods can be used to measure workplace safety, including safety audits, inspections, incident tracking, and employee feedback.
By systematically evaluating these elements, organizations can identify gaps in their safety protocols and take proactive measures to address them.
Safety Audits and Inspections
Safety audits and inspections are essential tools for measuring and improving workplace safety.
Their primary purpose is to systematically review safety policies, procedures, and practices to ensure they are effective and compliant with regulatory standards.
Audits and inspections help identify potential hazards, assess risk management strategies, and verify that safety measures are correctly implemented.
The scope of these activities can vary, from comprehensive audits that cover the entire organization to targeted inspections that focus on specific areas or processes.
Conducting Safety Audits
Safety audits involve thoroughly examining the workplace to assess the effectiveness of safety programs and compliance with regulations. The process typically includes:
-
Planning: Define the audit's scope, objectives, and schedule. Identify the areas to be audited and the evaluation criteria.
-
Documentation Review: Examine existing safety policies, procedures, training records, and incident reports.
-
Site Inspection: Physically inspect the workplace to identify hazards and verify the implementation of safety measures.
-
Interviews: Engage with employees and management to gather insights about safety practices and culture.
-
Evaluation: Analyze findings to assess compliance and the effectiveness of current safety protocols.
-
Reporting: Document the audit results, highlighting areas of compliance and those needing improvement. Provide actionable recommendations.
-
Follow-Up: Monitor the implementation of recommended actions to ensure continuous improvement.
Benefits of Inspections
Regular safety inspections offer numerous benefits, including:
-
Hazard Identification: Inspections help identify potential hazards that might not be evident during routine operations. This proactive approach can prevent accidents before they occur.
-
Regulatory Compliance: Regular inspections ensure the workplace complies with occupational health and safety regulations, avoiding legal penalties and enhancing the organization's reputation.
-
Employee Awareness: Involving employees in the inspection process raises their awareness of safety issues and encourages a safety culture. It empowers them to recognize and report hazards.
-
Continuous Improvement: Inspections provide ongoing feedback on the effectiveness of safety measures, allowing for continuous improvement and adaptation to new risks or changes in the workplace.
-
Accident Reduction: By identifying and addressing hazards, inspections can significantly reduce the incidence of workplace accidents and injuries, leading to a safer work environment.
Organizations can effectively measure and enhance workplace safety by incorporating regular safety audits and inspections into their safety management systems. This ensures a healthier and more secure environment for all employees.
Employee Training and Awareness
Employee training and awareness are critical components of workplace safety. Training equips employees with the knowledge and skills to recognize and avoid hazards, follow safety procedures, and respond appropriately in emergencies.
Obtaining a WHMIS certificate Ontario also ensures that employees are well-informed about the safe handling of hazardous materials, further enhancing workplace safety.
Awareness ensures that safety remains a top priority and that employees are constantly vigilant about potential risks.
Implementing Effective Training Programs
-
Needs Assessment: Identify specific training needs based on job roles, risk assessments, incident history, and regulatory requirements.
-
Curriculum Development: Develop a comprehensive training curriculum that covers general safety principles, specific operational hazards, emergency procedures, and the proper use of personal protective equipment (PPE).
-
Regular Updates: Regularly update training programs to incorporate new regulations, technologies, and changes in the workplace.
-
Engaging Methods: Utilize various training methods, including classroom sessions, online modules, hands-on practice, and simulations to cater to different learning styles.
-
Assessment and Feedback: Evaluate the effectiveness of training through assessments and gather feedback to improve future training sessions.
-
Continuous Education: Promote ongoing education and refresher courses to keep safety knowledge current and relevant.
Measuring Training Effectiveness
-
Pre- and Post-Training Assessments: Conduct assessments before and after training sessions to measure knowledge gains and identify areas needing further improvement.
-
Behavioral Observations: Monitor employees' adherence to safety practices and procedures in the workplace to assess the impact of training on their behavior.
-
Incident Tracking: Analyze the frequency and severity of incidents and near-misses to determine if improved training correlates with reduced workplace accidents.
-
Employee Feedback: Collect employee feedback regarding the training programs to understand their effectiveness and identify potential gaps.
Benefits of Training and Awareness
-
Increased Competence: Well-trained employees are more competent and confident in handling safety procedures and equipment.
-
Reduced Accidents: Proper training reduces the likelihood of accidents and injuries by ensuring employees know how to operate safely.
-
Compliance: Training helps ensure compliance with occupational health and safety regulations, reducing the risk of legal issues.
-
Empowerment: Training empowers employees to take proactive steps in maintaining a safe work environment and encourages a culture of safety awareness.
Canada Safety Training offers some of the most comprehensive training programs. Here are some of them:
-
Fire Extinguisher Training
-
Emergency Response Procedure
-
Hazard Recognition Training
-
Accident and Incident Investigation Training
-
Confined Space Awareness Training
-
Lockout Tagout Training
-
H2S Training Course
-
PPE Training
Promoting awareness fosters a safety-conscious culture where employees actively contribute to maintaining a secure work environment through informed decision-making and adherence to safety guidelines.
By systematically measuring and improving training and awareness programs, organizations can enhance their overall safety performance and create a safer, more productive workplace.
Building a Positive Safety Culture
Building a positive safety culture is essential for sustaining workplace safety. A strong safety culture promotes shared values, beliefs, and behaviors, prioritizing safety and leading to proactive risk management and continuous improvement.
Critical Elements of a Positive Safety Culture
-
Leadership Commitment: Leaders must demonstrate a genuine commitment to safety through their actions, decisions, and resource allocation.
-
Employee Involvement: Engage employees at all levels in safety initiatives, encouraging them to take ownership of safety practices and contribute ideas for improvement.
-
Open Communication: Foster open and transparent communication about safety issues, allowing employees to report hazards and incidents without fear of retaliation.
-
Recognition and Reward: Implement systems to recognize and reward safe behaviors and contributions to safety improvements.
-
Continuous Improvement: Encourage continuous improvement where safety processes and policies are regularly reviewed and enhanced.
Measuring Safety Culture
-
Safety Climate Surveys: Conduct regular surveys to gauge employees' perceptions of safety practices, leadership commitment, and overall safety culture.
-
Observation and Audits: Perform regular safety observations and audits to assess the adherence to safety practices and identify areas for improvement.
-
Incident Analysis: Analyze safety incidents and near-misses to understand the root causes and cultural factors that may have contributed.
-
Employee Feedback: Collect feedback through focus groups or suggestion systems to gain insights into the safety culture.
-
Safety Participation Metrics: Track employee participation in safety meetings, training sessions, and safety initiatives to measure engagement levels.
Technology in Safety Measurement
Technology enhances workplace safety by providing tools for monitoring, reporting, and analyzing safety data. It helps in early hazard detection, compliance tracking, and real-time communication of safety information.
Key Technologies for Safety Measurement
-
Wearable Devices: Equip employees with wearable devices that monitor vital signs, detect hazardous exposures, and provide real-time alerts.
-
Safety Management Software: Utilize software platforms for incident reporting, safety audits, compliance tracking, and data analysis.
-
IoT Sensors: Deploy Internet of Things (IoT) sensors to monitor environmental conditions such as air quality, temperature, and noise levels.
-
Mobile Apps: Implement mobile applications for easy reporting of hazards, incidents, and safety observations by employees.
Measuring Safety with Technology
-
Real-Time Monitoring: Use IoT and wearable devices to monitor real-time safety conditions, ensuring immediate response to potential hazards.
-
Data Analytics: Analyze data collected from safety management software and IoT devices to identify trends, predict risks, and develop targeted interventions.
-
Digital Reporting: Implement digital reporting systems to streamline the collection and analysis of safety incidents and near-misses, improving response times and data accuracy.
-
Performance Metrics: Use technology platforms to track key performance indicators (KPIs) such as incident rates, response times, and compliance levels.
-
Training Effectiveness: Use e-learning platforms and training software to measure the effectiveness of safety training programs through assessments and progress tracking.
Regulatory Compliance
Regulatory compliance ensures that workplaces adhere to established safety standards and legal requirements, reducing the risk of accidents and legal penalties.
In Canada, compliance with occupational health and safety regulations is essential for maintaining a safe work environment.
Key Regulatory Bodies and Standards
-
Occupational Health and Safety (OHS) Legislation: Compliance with federal, provincial, and territorial OHS legislation is mandatory. Key regulations include the Canada Labour Code and specific provincial acts.
-
Workplace Hazardous Materials Information System (WHMIS): Compliance with WHMIS standards ensures proper labeling, handling, and dissemination of information about hazardous materials.
-
Canadian Centre for Occupational Health and Safety (CCOHS): Following CCOHS guidelines and best practices helps enhance workplace safety.
Measuring Compliance
-
Regular Audits and Inspections: Conduct regular safety audits and inspections to ensure compliance with OHS regulations and identify areas for improvement.
-
Compliance Checklists: Use detailed checklists to verify that all regulatory requirements are being met, from hazard assessments to safety training and record-keeping.
-
Incident Reporting: Maintain accurate records of all incidents and near-misses, reporting them to the appropriate regulatory bodies as required.
-
Training Records: Keep comprehensive records of all safety training provided to employees, ensuring that it meets regulatory standards and is up to date.
-
Regulatory Audits: Prepare for and undergo audits by regulatory authorities, ensuring all documentation and practices comply with legal requirements.
Benefits of Compliance
-
Reduced Legal Risk: Ensures the organization is not exposed to legal penalties or fines for non-compliance.
-
Enhanced Safety: Adherence to regulations helps maintain a safer work environment by following best practices and standards.
-
Improved Reputation: Demonstrates a commitment to safety and regulatory compliance, enhancing the organization's reputation among employees, customers, and stakeholders.
-
Operational Efficiency: Compliance often leads to better-organized safety practices and procedures, improving overall operational efficiency.
Organizations can effectively measure and improve workplace safety by focusing on these elements, ensuring a safer and more productive work environment.
How to Measure Safety in the Workplace (FAQs)
How do you monitor safety in the workplace?
Monitoring safety in the workplace involves:
-
Conducting regular safety audits and inspections.
-
Using real-time data from IoT devices.
-
Tracking incident reports and compliance metrics.
What role do safety audits and inspections play in ensuring workplace safety?
Safety audits and inspections identify potential hazards, ensure compliance with safety regulations, and promote a culture of continuous improvement in workplace safety.
How often should safety audits and inspections be conducted?
Safety audits and inspections should be conducted regularly, typically every quarter, or more frequently if required by industry standards or specific workplace conditions.
Conclusion
Ensuring safety in the workplace demands a comprehensive and proactive approach. Understanding how to measure safety in the workplace is essential to ascertain the safety of the personnel.
The case studies underscore the effectiveness of tailored strategies in mitigating risks and fostering a secure work environment.
From implementing targeted employee training programs to integrating cutting-edge technology for real-time monitoring, each case study demonstrates the positive impact of deliberate safety measures.
Incorporating online safety certifications into employee training adds an extra layer of validation, ensuring that individuals possess the necessary knowledge and skills to uphold the highest safety standards.
Companies that invest in creating a safety-conscious culture driven by leadership initiatives and collaborative efforts witness tangible improvements in incident rates and overall safety metrics.
The outlined vital metrics, such as incident rates, severity rates, Lost Time Injury Frequency Rate (LTIFR), and near-miss reporting, serve as vital indicators of workplace safety.
Organizations can leverage these metrics to assess their safety performance, identify areas for improvement, and establish a baseline for continuous enhancement.
As companies navigate the complex landscape of workplace safety, the amalgamation of training, technology, and cultural transformation emerges as a potent formula for success.
By embracing these insights and case study examples, organizations can meet regulatory requirements and create workplaces where employees thrive in an atmosphere of security and well-being.
Ultimately, the commitment to measuring and enhancing safety in the workplace is an investment that pays dividends in employee satisfaction, productivity, and long-term success.