Process Hazard Analysis (PHA) is a comprehensive method for identifying and assessing potential hazards associated with industrial processes.
It involves thoroughly examining each step and component within a process to determine any risks that could lead to accidents, injuries, or environmental damage.
According to the Canadian Occupational Safety, 993 workplace fatalities were reported in 2022, which calls for implementing Process Hazard Analysis.
WHMIS training plays a vital role in this process, equipping workers with the knowledge to recognize and understand potential hazards in the workplace.
WHMIS stands for the Workplace Hazardous Materials Information System, a comprehensive system designed to communicate information about hazardous materials used in Canadian workplaces.
PHA is critically important for industries involving complex processes, such as chemical manufacturing, oil refining, pharmaceuticals, and construction.
Companies can proactively identify and mitigate risks by conducting PHA before they escalate into serious incidents. By conducting a PHA, organizations can also pinpoint specific risks related to confined space entry, such as hazardous atmospheres, equipment failures, and human errors.
This helps prevent workplace accidents, injuries, and loss of life, protects assets, prevents environmental harm, and safeguards the organization's reputation.
Here are the primary purposes of PHA:
-
Identify potential hazards within a process, including equipment failures, human errors, and external factors like natural disasters.
-
Facilitates the evaluation of these hazards to determine their severity and likelihood of occurrence.
-
Provide the basis for developing and implementing effective risk management strategies, including engineering controls, administrative controls, and emergency response plans.
Process Hazard Analysis ensures various industries' safety, reliability, and regulatory compliance. It is focused on risk management, protects workers and the environment, and enhances operational efficiency.
Background of Process Hazard Analysis
Process Hazard Analysis (PHA) was first introduced during the Industrial Revolution when manufacturing processes became more complex and hazardous.
However, the formalization of PHA methodologies gained popularity in the mid-20th century with the rise of the chemical industry and the recognition of the need for systematic risk assessment.
Evolution of PHA Methodologies
Over time, PHA methodologies have evolved from essential checklists and qualitative assessments to more sophisticated and comprehensive approaches.
Early methods like What-If analysis and Hazard and Operability Studies (HAZOP) paved the way for techniques such as Fault Tree Analysis (FTA), Event Tree Analysis (ETA), and Quantitative Risk Assessment (QRA).
Each method offers unique advantages in identifying and analyzing process hazards.
Regulatory Requirements and Standards Related to PHA
As industrial accidents became more frequent and severe, governments around the world began implementing regulations and standards to ensure the safety of workers and the public.
These regulations often mandate using PHA as part of a broader process safety management framework.
For example, the Canadian Centre of Occupational Health and Safety (CCOHS) requires companies to conduct PHA under Canada's Process Safety Management (PSM) standard.
Similarly, international standards such as the American Petroleum Institute's API 750 and API 751 provide guidelines for conducting PHA in specific industries, such as petroleum refining.
Compliance with these regulations and standards is essential for companies to demonstrate their commitment to process safety and regulatory compliance.
Methods and Techniques of Process Hazard Analysis
Process Hazard Analysis (PHA) uses various methods and techniques to systematically identify, assess, and mitigate potential hazards associated with industrial processes.
Here, we are exploring some of the most widely used approaches:
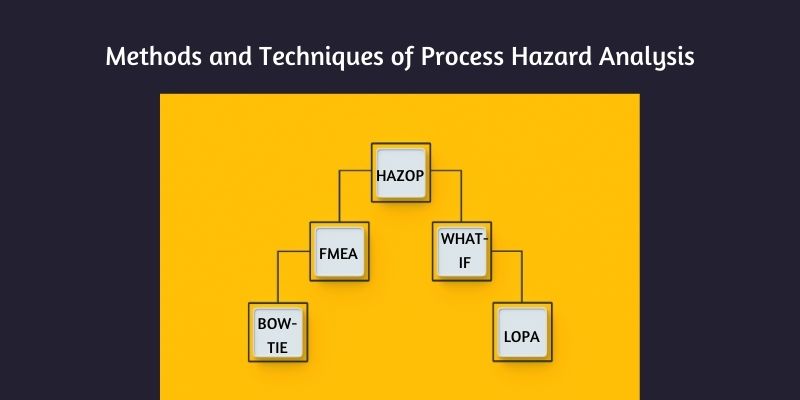
Let’s explore each of these approaches in detail to understand them better.
1. HAZOP (Hazard and Operability Study)
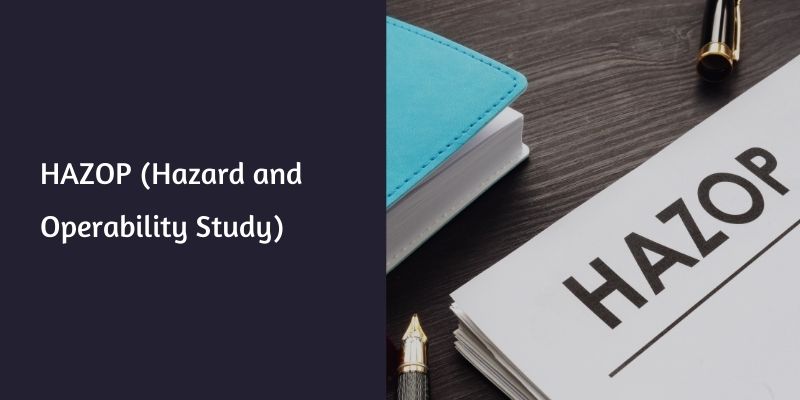
HAZOP is a systematic technique for identifying potential hazards and operability issues.
It involves a team systematically examining each process component, guided by guidelines to assess the deviations from the intended operation.
HAZOP identifies potential hazards and suggests preventive or mitigative measures by exploring deviations in parameters such as flow, temperature, pressure, and composition.
2. FMEA (Failure Modes and Effects Analysis)
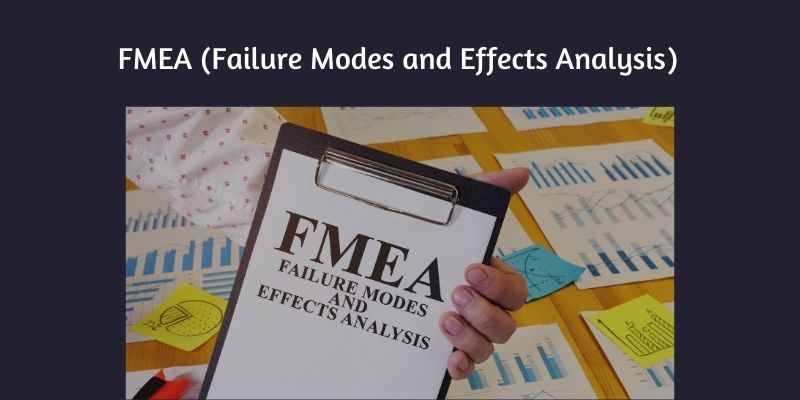
FMEA is a proactive technique for identifying and prioritizing potential failure modes within a system, process, or product.
It evaluates each component or step in a process to determine how it could fail, the effects of the failure, and the likelihood of occurrence.
By quantifying failure modes' severity, occurrence, and detectability, FMEA helps prioritize actions to mitigate risks and enhance reliability.
3. What-if Analysis
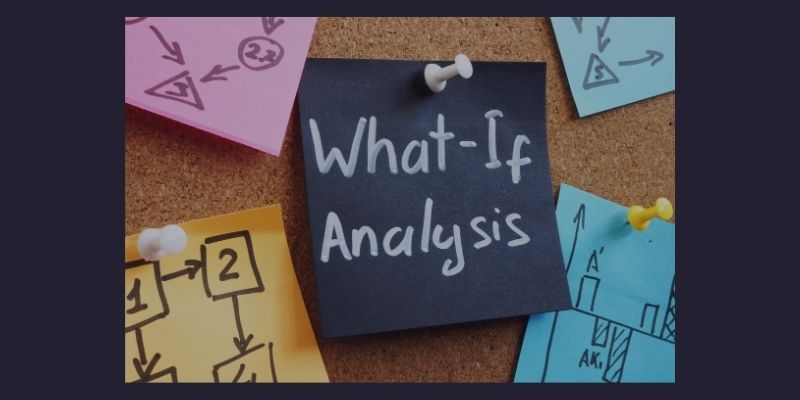
What-if analysis is a technique to explore hypothetical scenarios and their consequences.
It involves posing "what-if" questions to a team of experts to stimulate discussion and identify potential hazards or vulnerabilities in a process.
This qualitative approach helps uncover risks that may be hidden through routine assessments and encourages creative thinking about potential solutions.
4. Bow-tie Analysis
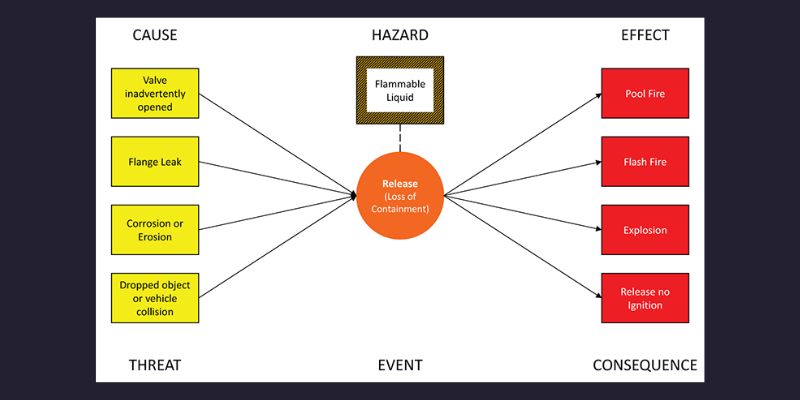
Bow-tie analysis is a visual risk assessment technique that explores the relationships between hazards, preventive measures, and consequences.
It uses a diagram resembling a bow tie to illustrate the causes of a potential incident (the "bow") and the preventive and mitigating barriers (the "wings").
By mapping out these elements, bow-tie analysis helps organizations understand the effectiveness of existing safeguards and identify areas for improvement.
5. Layer of Protection Analysis (LOPA)
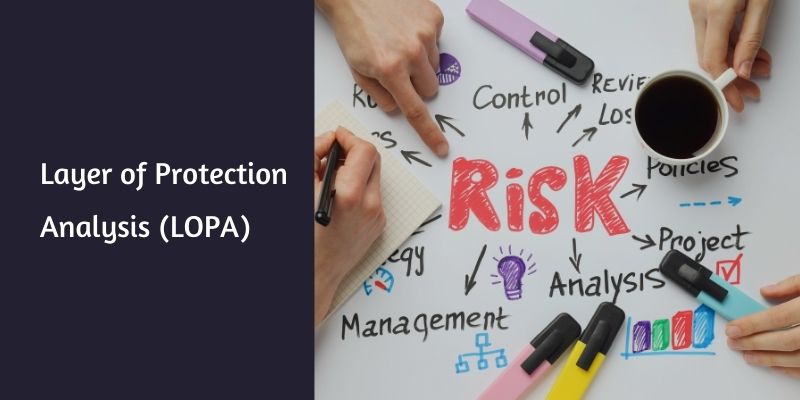
LOPA is a semi-quantitative technique used to assess the adequacy of layers of protection against process hazards.
It involves identifying potential scenarios leading to undesirable consequences, quantifying their likelihood and severity, and evaluating the effectiveness of existing safeguards.
LOPA helps organizations determine whether additional risk reduction measures are necessary to achieve an acceptable level of risk.
Each method and technique offers a unique understanding of hazards and risk management, allowing organizations to design their approach to suit their needs and challenges.
Implementation of Process Hazard Analysis
Process Hazard Analysis (PHA) ensures safety in industrial processes. Here's a breakdown of its implementation:
Steps Involved in Conducting a PHA
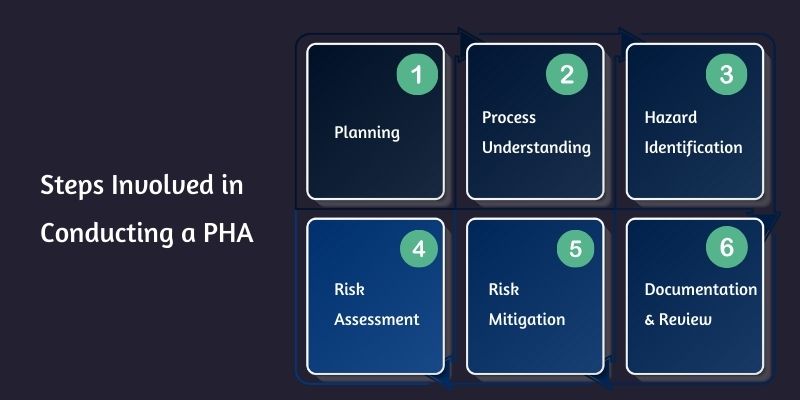
Here are the steps involved in conducting a Process Hazard Analysis (PHA):
-
Planning: Define the PHA scope, objectives, and team composition.
-
Process Understanding: Gather relevant information about the process, including design documents, operating procedures, and previous incident reports.
-
Hazard Identification: Identify potential hazards associated with the process using techniques such as HAZOP, FMEA, and What-if analysis.
-
Risk Assessment: To prioritize risks evaluate the severity, likelihood, and consequences of identified hazards.
-
Risk Mitigation: Develop and implement measures to eliminate or mitigate identified hazards, including engineering controls, administrative controls, and procedural changes.
-
Documentation and Review: Document the PHA findings, recommendations, and action plans and periodically review and update them as needed.
Role of Multidisciplinary Teams in PHA
Multidisciplinary teams bring together individuals with diverse expertise, including process engineers, safety professionals, operators, and maintenance personnel.
Their varied perspectives and knowledge enhance the effectiveness of PHA by ensuring comprehensive hazard identification, thorough risk assessment, and practical risk mitigation strategies.
Training for Process Hazard Analysis
Professionals involved in PHA should undergo specialized Hazard Recognition Training to develop the necessary skills and knowledge.
This training covers hazard identification techniques, risk assessment principles, PHA methodologies, and regulatory requirements.
Additionally, certification and qualification programs exist to validate practitioners' proficiency in conducting PHA.
Furthermore, incorporating confined space training makes sure that professionals are well-prepared to identify and manage the unique hazards associated with confined spaces.
Certification and Qualification Requirements for PHA Practitioners
Certification programs, such as those offered by professional organizations like the Chemical Institute of Canada (CIC) or the Institute of Hazardous Materials Management (IHMM), establish standards for PHA practitioners.
These programs typically require candidates to demonstrate proficiency through examinations and fulfill continuing education requirements to maintain certification.
Continuous Professional Development in PHA
Continuous professional development is essential for PHA practitioners to stay ahead of emerging technologies, best practices, and regulatory updates.
Participation in workshops, conferences, and online courses helps practitioners enhance their skills, exchange knowledge with peers, and stay informed about the latest developments in process safety.
Tools and Software Used in PHA
Various tools and software applications, including PHA software packages, risk assessment matrices, and process simulation tools, are available to facilitate PHA.
These tools improve data collection, analysis, and documentation processes, improving the efficiency and accuracy of PHA.
Challenges in Implementing PHA
Despite its importance, implementing PHA can present several challenges, including resource constraints, lack of expertise, resistance to change, and difficulty prioritizing risks.
Overcoming these challenges requires commitment from management, adequate training and support for personnel, and a culture that prioritizes safety and continuous improvement.
By addressing these challenges and adhering to best practices in PHA implementation, organizations can enhance their process safety performance, minimize risks, and protect the well-being of workers and the environment.
Final Words
Understanding Process Hazard Analysis (PHA) is about protecting lives, assets, and the environment.
Organizations can systematically identify, assess, and mitigate risks in their industrial processes by implementing different methodologies, such as HAZOP, FMEA, and What-if analysis, supported by advanced tools and software.
The role of multidisciplinary teams, with comprehensive training and continuous professional development, is crucial in ensuring the effectiveness of PHA efforts.
However, challenges in PHA implementation, such as resource constraints and resistance to change, highlight the need for commitment from all levels of an organization.
Overcoming these challenges requires creating a culture of safety where every individual contributes to risk identification and mitigation.
The investment in PHA is an investment in the well-being of employees, the protection of assets, and the sustainability of businesses.