As the collection of goods is essential to any business, warehouse safety plays a crucial part in ascertaining the protection of your products. Warehouses are the center of inventory management, distribution, and logistics, making their smooth functioning critical for businesses.
Even with the constant activity and hustle, one aspect is essential: the safety of workers and the overall workplace environment – this is where our guide on “warehouse safety tips for the workplace” can be helpful.
Warehouses are regarded as the hub of activities, machinery, and personnel, making safety even more essential. Every element demands a heightened sense of precaution, from the towering shelves to the swift forklift movements.
Safety at the workplace is not only about compliance with regulations; it's about preserving the workforce's well-being.
As we explore warehouse safety improvement ideas, it becomes evident that prioritizing safety is the basis for protecting the inventory as well as personnel. So, let’s find out how to create a safer environment at the warehouse.
What is Warehouse Safety?
Warehouse safety is all about making sure workers stay safe while doing their jobs. In Canada, this is especially important because the warehouse industry has a higher rate of serious injuries compared to other jobs.
The Occupational Safety and Health Administration (OSHA) has highlighted this, showing that warehouses need to focus on safety to protect workers. By following safety guidelines and using the right equipment, we can prevent accidents and keep everyone safe at work.
Importance of Warehouse Safety
Keeping a warehouse safe is really important for protecting workers and making sure everything runs smoothly. Warehouses are busy places with lots of heavy equipment, tall shelves, and people moving around all the time. Because of this, there are many risks that can lead to accidents or injuries.
When safety is a priority, it helps everyone feel secure and do their jobs better. Simple rules, like wearing safety gear, keeping walkways clear, and using equipment correctly, can make a big difference in preventing accidents.
Make warehouse safety rules that fit the specific needs of your warehouse. For example, a cold storage area might need different rules than a regular warehouse. Regularly review and update safety rules based on new information, feedback from workers, and changes in laws.
When everyone works together to stay safe, it benefits not just the workers but the entire warehouse operation. By focusing on safety, we can create a better environment for everyone.
Warehouse Safety Statistics
- Forklift-related accidents in Canada cost businesses over $125 million each year just in direct compensation costs.
- The loading dock is a common area for accidents, with reports indicating that 25% of all workplace accidents occur in this location.
- According to the U.S. Bureau of Labor Statistics, In 2022, there were 1,053 fatalities in the transportation and warehousing industry, accounting for 19.2% of all fatal work injuries in the United States.
15 Effective Warehouse Safety Tips
Maintaining a secure warehouse environment is crucial for employees' well-being and operations' overall productivity. The following concise safety tips will help you create a safer workplace.
- Adequate training for all employees
- Proper use of personal protective equipment (PPE)
- Regular equipment maintenance and inspection
- Practical housekeeping and clutter reduction
- Implementation of proper signage and labeling
- Safe lifting techniques and material handling
- Emergency response protocols and drills
- Guidelines for operating machinery and vehicles
- Use of proper lighting and ventilation
- Safety training and educational programs
- Warehouse layout and housekeeping
- Fire safety and prevention
- Hazard communication and chemical safety
- Incident reporting and investigation
- Technology and automation for safety
By implementing these warehouse safety tips, you can create a workplace environment that prioritizes the well-being of employees and ensures the smooth operation of your warehouse facility.
1. Adequate Training for All Employees
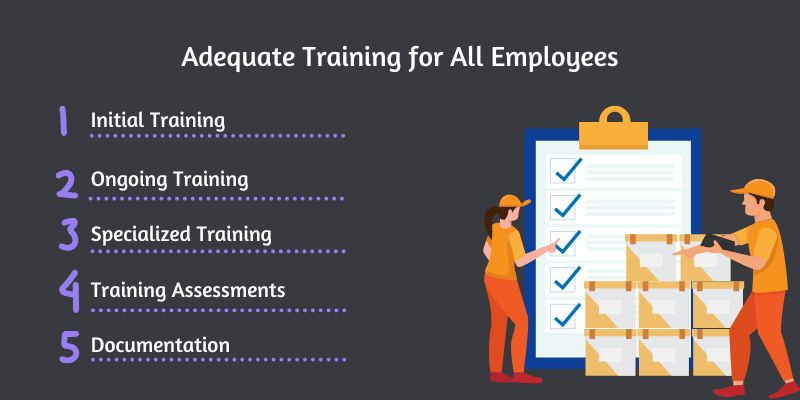
Adequate training is the cornerstone of a safe warehouse environment. Comprehensive training programs should cover all aspects of warehouse operations, including the correct use of equipment, hazard recognition, PPE, and emergency procedures.
- Initial Training: New employees should undergo thorough orientation and training sessions, introducing them to the warehouse's safety protocols. This includes instruction on safely operating forklifts, pallet jacks, and other machinery and the proper methods for lifting and moving heavy items.
- Ongoing Training: Safety training should not be a one-time event. Regular refresher courses and training updates are essential to ensure all employees know the latest safety practices and regulations. This can be achieved through periodic safety meetings, workshops, and e-learning modules.
- Specialized Training: Certain roles may require specialized training. For example, employees transporting hazardous materials must be trained in safe handling, storage, and disposal procedures, as well as in the use of protective equipment and emergency response techniques. Hence, they need to be trained in all these aspects.
- Training Assessments: Regular assessments and drills can help gauge the effectiveness of the training programs. These assessments should identify knowledge gaps and areas for improvement, ensuring that employees are fully prepared to handle any safety issues.
- Documentation: Keeping detailed records of all training sessions and certifications is crucial. This ensures compliance with regulatory requirements, helps track employee progress, and identifies those needing additional training.
2. Proper Use of Personal Protective Equipment (PPE)

Personal Protective Equipment (PPE) is critical to workplace safety in a warehouse setting.
Proper use of PPE can prevent a wide range of injuries, from minor cuts and bruises to more severe incidents involving hazardous materials or machinery.
- Identification of PPE Needs: The first step in implementing effective PPE use is to conduct a thorough risk assessment to identify the hidden hazards in the workplace, especially in the warehouse. This will help determine the types of PPE required, such as gloves, safety glasses, hard hats, high-visibility vests, and steel-toed boots.
- Employee Training on PPE: Employees must be trained on their PPE's correct use, maintenance, and limitations. This includes appropriately wearing, adjusting, removing equipment, and inspecting it for damage before use.
- Availability and Accessibility: Ensure that PPE is readily available and easily accessible to all employees. It should also be stored clean and organized, with sufficient quantities to meet the workforce's needs.
- Maintenance and Replacement: Regular inspection and maintenance of PPE are essential to ensure its effectiveness. Employees should be encouraged to report damaged or worn-out equipment, and procedures should be in place for the timely replacement of such items.
- Compliance and Enforcement: Establish clear policies regarding the mandatory use of PPE and enforce these policies consistently. Supervisors and safety officers should monitor compliance and take corrective action to ensure all employees adhere to PPE requirements.
- Comfort and Fit: Proper fit and comfort of PPE are vital for ensuring employees wear it consistently. Providing PPE in various sizes and allowing employees to select equipment that fits them well can significantly improve compliance and overall safety.
3. Regular Equipment Maintenance and Inspection
Regular maintenance and inspection of equipment are crucial for ensuring the safety and efficiency of warehouse operations.
Neglecting this can lead to equipment failures, accidents, and costly downtime. Here's a detailed look at how regular maintenance and inspection can enhance warehouse safety:
- Routine Inspections: Schedule routine inspections of all equipment, including forklifts, pallet jacks, conveyor belts, and shelving units. These inspections should be conducted by qualified personnel who can identify potential issues before they become serious problems. Regular checks help ensure that all equipment is functioning correctly and safely.
- Preventive Maintenance: Implement a preventive maintenance program that includes regular servicing and repairs. This proactive approach can help avoid unexpected equipment breakdowns and extend the lifespan of machinery. Preventive maintenance tasks include lubricating moving parts, replacing worn-out components, and performing software updates on automated systems.
- Documentation and Record-Keeping: Maintain detailed records of all maintenance and inspection activities. This documentation helps track the history of each piece of equipment, ensuring that it receives timely care. Keeping accurate records also aids in compliance with regulatory requirements and can be helpful during audits or inspections.
- Employee Training: Train employees on the proper use and essential maintenance of the equipment they operate. This includes instructing them on performing pre-use inspections, reporting issues, and understanding potential equipment failure signs. Well-trained employees can help identify problems early, reducing the risk of accidents.
- Third-Party Inspections: Consider having periodic inspections conducted by third-party experts. These professionals can provide an unbiased assessment of the equipment's condition and offer recommendations for improvements or repairs, adding an extra layer of safety and assurance.
4. Effective Housekeeping and Clutter Reduction
Maintaining a clean and organized warehouse is fundamental to preventing accidents and ensuring a safe working environment.
Practical housekeeping involves more than just cleaning; it includes systematic organization and clutter reduction to minimize hazards.
- Clear Aisles and Walkways: Ensure that all aisles and walkways are clear of obstructions. This includes removing pallets, boxes, and other items that can pose tripping hazards or block emergency exits.
- Organized Storage: Implement an organized storage system that categorizes items based on their size, weight, and frequency of use. Store items properly using shelving units, racks, and bins, and store heavy items at lower levels to prevent injuries from lifting.
- Regular Cleaning Schedule: Establish a regular cleaning schedule that includes sweeping, mopping, and dusting. Pay special attention to areas prone to spills, such as loading docks and storage areas for liquids. Regular cleaning helps prevent slip-and-fall accidents and maintains a healthy working environment.
- Waste Management: Set up designated areas for waste disposal and recycling. Ensure that waste bins are emptied regularly and that hazardous materials are disposed of according to safety guidelines. Proper waste management reduces the risk of contamination and environmental hazards.
- Spill Control: Establish spill prevention and control procedures, including readily accessible spill kits. Train employees to respond to spills quickly and effectively to minimize risks and prevent accidents.
- Clutter-Free Zones: Designate specific areas for storing tools and equipment when not in use. Implement a "clean as you go" policy to encourage employees to maintain a tidy workspace throughout their shifts. Clutter-free zones reduce the risk of accidents and improve overall efficiency.
5. Implementation of Proper Signage and Labeling
Proper signage and labeling are essential for communicating hazards, providing directions, and ensuring that employees are aware of safety protocols in the warehouse.
Effective use of signs and labels can significantly reduce accidents and improve overall safety.
- Hazard Identification: Use clear and visible signs to identify hazardous areas, such as those with moving machinery, high noise levels, or dangerous chemicals. Signs should be placed at eye level, and universally recognized symbols and colors should convey the message quickly and effectively.
- Safety Instructions: Post safety instructions and reminders in strategic locations throughout the warehouse. This includes guidelines for safe lifting techniques, emergency procedures, and the proper use of PPE. Having these reminders readily available helps reinforce safety practices.
- Directional Signage: Implement directional signage to guide employees and visitors through the warehouse. Marked exits, emergency routes, and assembly points ensure everyone knows where to go in an emergency. Directional signs also help with efficient navigation and workflow.
- Labeling of Materials and Equipment: Label all materials, equipment, and storage areas accurately. This includes identifying hazardous substances with appropriate warning labels, indicating weight limits on shelving units, and marking tools and machinery with usage instructions. Proper labeling prevents misuse and helps employees handle items safely.
- Maintenance of Signage: Regularly inspect all signs and labels to ensure they are in good condition and legible. Replace any damaged or faded signs promptly to maintain clear communication. Signs that are difficult to read or missing can lead to confusion and accidents.
- Training on Signage: Educate employees on the meaning of different signs and labels used in the warehouse. Ensure that new hires receive thorough hazard identification training on warehouse signage as part of their orientation. Understanding the purpose and importance of signage helps employees follow safety protocols consistently.
6. Safe Lifting Techniques and Material Handling
Safe lifting techniques and material handling are essential practices to prevent injuries and ensure efficiency in the workplace.
Proper methods protect employees from musculoskeletal injuries and create a more organized and safer working environment.
Proper Lifting Techniques

- Plan the Lift: Evaluate the object's weight and stability before lifting. Determine if assistance or equipment is needed. Ensure the path is clear of obstacles.
- Correct Posture: Stand with feet shoulder-width apart to provide a stable base. Bend at the knees, not the waist, to lower your body to the object's level. Keep your back straight and maintain a natural curve.
- Grip and Lift: Use a firm grip with both hands. Tighten your core muscles to support your spine. Lift using your legs, not your back, by straightening your knees while keeping the object close to your body.
- Avoid Twisting: To prevent strain, turn your whole body by moving your feet rather than twisting your torso. Use your legs to shift direction.
- Set Down Safely: Lower the object by bending your knees and maintaining a straight back. Place the object gently down to avoid sudden movements.
Material Handling Equipment
- Use Proper Tools: For heavy or bulky items, employ equipment like forklifts, pallet jacks, and cranes. Ensure that employees are trained in their operations.
- Maintain Equipment: Regularly inspect and maintain material handling equipment to ensure it is in safe working condition.
- Ergonomic Solutions: Implement ergonomic tools and aids, such as adjustable-height workstations and conveyor belts, to reduce manual lifting and repetitive strain.
7. Emergency Response Protocols and Drills
Effective emergency response protocols and drills are critical for ensuring preparedness and minimizing the impact of workplace emergencies.
Implementing these measures helps ensure employees know how to respond quickly and effectively to various situations.
Developing Emergency Response Protocols
- Identify Potential Emergencies: Assess potential workplace emergencies, such as fires, chemical spills, natural disasters, or medical emergencies.
- Create Detailed Plans: Develop comprehensive response plans for each type of emergency. Include steps for evacuation, communication, and containment. Assign roles and responsibilities to employees.
- Emergency Contacts: Maintain a list of emergency contacts, including local emergency services, and ensure it is readily accessible to all employees.
Conducting Drills
- Regular Drills: Schedule regular emergency drills to practice response procedures. Include scenarios for different types of emergencies to ensure readiness for various situations.
- Evaluate and Improve: After each drill, evaluate performance and identify areas for improvement. Gather feedback from participants to refine and enhance the response plans.
- Communicate Procedures: Communicate emergency procedures to all employees. Use visual aids, such as evacuation maps and emergency contact lists, to reinforce the information.
Special Considerations
- Training for Specific Roles: Provide additional training for employees with specific roles in emergency response, such as first aid responders or fire wardens.
- Accessibility: Ensure that emergency plans and procedures are accessible to all employees, including those with disabilities. Provide necessary accommodations to ensure everyone can participate in drills and follow protocols.
8. Guidelines for Operating Machinery and Vehicles
Safe operation of machinery and vehicles is essential to prevent accidents and ensure smooth workplace operations. Adhering to guidelines helps protect operators and others in the vicinity from harm.
Machinery Operation Guidelines

- Training and Certification: Ensure all operators are properly trained and certified for their machinery. Provide hands-on training and assessments to verify competence.
- Pre-Operation Checks: Conduct thorough inspections of machinery before use. Check for any signs of wear, damage, or malfunction. Address any issues before operating the equipment.
- Follow Manufacturer Instructions: Follow the manufacturer's operating instructions, including load limits, operational procedures, and safety warnings.
- Safe Operation Practices: Operate machinery at safe speeds and avoid distractions. Keep hands and body parts clear of moving parts. Use safety guards and devices as required.
Vehicle Operation Guidelines
- Vehicle Inspections: Perform pre-operation inspections of vehicles, including checking fluid levels, brakes, lights, and tires. Ensure the vehicle is in safe working condition before use.
- Driving Practices: Follow defensive driving practices, such as maintaining a safe following distance, obeying speed limits, and avoiding aggressive maneuvers. Adjust driving based on weather and road conditions.
- Load Securing: Ensure loads are properly secured to prevent shifting or falling. Use appropriate restraints and tie-downs for different types of cargo.
- Vehicle Maintenance: Regularly maintain and service vehicles according to manufacturer recommendations. Address any mechanical issues promptly to prevent breakdowns or accidents.
Safety Protocols
- Emergency Procedures: Familiarize operators with emergency procedures for machinery and vehicle failures. Include steps for shutting down equipment safely and reporting issues.
- PPE Requirements: When operating machinery and vehicles, you must wear appropriate personal protective equipment (PPE), such as safety glasses, gloves, and hearing protection.
- Incident Reporting: Report any incidents involving machinery and vehicles to supervisors. Use these reports to improve safety practices and prevent future occurrences.
9. Use of Proper Lighting and Ventilation
Proper lighting and ventilation are essential to workplace safety. Let's explore how they can benefit employees and employers.
Proper Lighting
- Importance of Adequate Lighting: Proper lighting in a warehouse is essential to ensure that all areas are visible, reducing the risk of accidents and errors. Poor lighting can lead to missed hazards, misjudged distances, and increased likelihood of trips and falls.
- Types of Lighting: Use bright, well-distributed lighting to illuminate work areas. Ensure all high-traffic and high-risk areas, such as loading docks and storage racks, are well-lit. Use task lighting for detailed work areas where precision is needed.
- Regular Maintenance: Inspect and maintain lighting fixtures to ensure they work correctly. Replace bulbs promptly and clean light covers to avoid reduced illumination from dirt and grime.
- Emergency Lighting: Install emergency lighting in critical areas to ensure visibility during power outages or emergencies. Ensure that emergency lights are tested regularly and that backup power sources are available.
Proper Ventilation
- Importance of Ventilation: Adequate ventilation is crucial for maintaining air quality and controlling temperature within a warehouse. Proper ventilation helps to remove harmful fumes, dust, and heat, creating a safer and more comfortable working environment.
- Types of Ventilation: Use a combination of natural and mechanical ventilation systems. Ensure that exhaust fans and air intake systems are strategically placed to facilitate adequate air circulation. Use ventilation systems that meet industry standards for the types of materials handled in the warehouse.
- Monitoring and Maintenance: Regularly inspect and maintain ventilation systems to ensure they function correctly—clean filters and vents to prevent blockages and reduce the risk of air quality issues. Implement air quality monitoring to detect and address potential hazards.
- Ventilation in Confined Spaces: Ensure that confined spaces within the warehouse, such as storage areas or maintenance rooms, are adequately ventilated to prevent the buildup of hazardous gases and to provide a safe working environment.
- Confined Space Safety Skills: For more information on ensuring safety in these areas, consider enrolling in confined space training, which equips workers with essential skills for working safely in confined spaces and understanding proper ventilation practices.
10. Safety Training and Educational Programs

Safety training and education programs can prepare workers for emergencies, identify workplace hazards, and teach workers how to deal with common safety concerns.
Importance of Training
- Comprehensive Training: Thorough safety training ensures all warehouse employees understand and adhere to safety protocols. Training helps prevent accidents, improve response times, and build a safety culture.
- Types of Training: Offer various types of training, including initial orientation for new employees, specialized training for handling specific equipment or materials, and refresher courses to keep skills and knowledge current.
- Hands-On Training: Incorporate hands-on training exercises to give employees practical experience with safety procedures and equipment. Use simulations and drills to prepare employees for real-life scenarios, including a defensive driving course that teaches safe driving techniques and hazard recognition on the road.
- Training Content: Include training on safe lifting techniques, emergency procedures, equipment operation, and proper use of PPE. Tailor training programs to address your warehouse environment's specific needs and risks.
Ongoing Education
- Continual Learning: Foster a culture of continual learning by offering ongoing education opportunities for employees. Encourage attendance at industry conferences, workshops, and seminars to stay updated on the latest safety practices and regulations.
- Feedback and Improvement: Collect employee feedback about the effectiveness of training programs and use this information to make improvements. Review and update training materials regularly to reflect safety standards and best practice changes.
Evaluation and Assessment
- Testing and Certification: Assess employee knowledge and skills through testing and certification programs. Use assessments to identify areas where additional training may be needed and to ensure that employees meet safety standards.
- Documentation: Maintain records of all training and certification activities and ensure that training documentation is readily accessible for review and compliance.
11. Warehouse Layout and Housekeeping
The layout of the warehouse and housekeeping is essential for building a safety culture in the workplace.
Warehouse Layout
- Design for Safety: The layout of a warehouse should be designed to minimize hazards and ensure smooth workflow. Arrange storage areas, workstations, and aisles to promote safe and efficient movement of goods and personnel.
- Clear Aisles and Pathways: Ensure that aisles and pathways are wide enough to accommodate the movement of equipment and personnel. Keep these areas clear of obstructions, such as pallets or equipment, to prevent accidents and improve accessibility.
- Signage and Markings: Clear signage and floor markings indicate safety zones, emergency exits, and hazardous areas. Ensure that signs are visible and understandable to all employees.
Housekeeping
- Regular Cleaning: Implement a regular cleaning schedule to maintain a clean and organized warehouse environment. This includes sweeping floors, removing spills, and disposing of waste materials.
- Clutter Management: Keep work areas free of unnecessary clutter. Store materials and tools in designated areas to prevent tripping hazards and to facilitate easy access.
- Spill Response: Establish procedures for promptly addressing and cleaning up spills or leaks. Ensure that employees are trained in spill response and that necessary materials, such as absorbents and clean-up tools, are readily available.
Safety Inspections
- Routine Inspections: Conduct routine safety inspections to identify and address potential hazards. Regularly review the warehouse layout and housekeeping practices to ensure compliance with safety standards.
- Corrective Actions: Address any issues identified during inspections promptly. Implement corrective actions to prevent recurrence and continually improve warehouse safety.
12. Fire Safety and Prevention

Fire safety and prevention are critical aspects of workplace safety, designed to protect employees, property, and the environment from the devastating effects of fire.
Implementing effective fire safety measures helps prevent fire incidents. It ensures that, if a fire does occur, employees are prepared to respond swiftly and safely.
Importance of Fire Safety
- Preventing Fires: Fire safety protects employees, assets, and the workplace environment. Effective fire prevention reduces the risk of fire incidents and minimizes potential damage.
- Compliance: Adhering to fire safety regulations ensures compliance with legal requirements and helps avoid penalties or legal issues.
Fire Prevention Strategies
- Regular Inspections: Conduct routine inspections of electrical systems, heating equipment, and flammable materials to identify and address potential fire hazards. Ensure that all electrical wiring is up to code and that equipment is maintained in good condition.
- Safe Storage of Flammable Materials: Store flammable materials in designated, well-ventilated areas away from heat sources. Use appropriate containers and labeling to ensure proper handling and storage.
- Fire Protection Equipment: Install and maintain fire alarms, sprinkler systems, and fire extinguishers throughout the workplace. Ensure that fire extinguishers are regularly inspected and employees are trained.
- Emergency Exits and Evacuation Plans: Mark emergency exits and ensure they are unobstructed. Develop and regularly review evacuation plans to ensure a swift and orderly evacuation during a fire. Conduct fire drills to familiarize employees with evacuation procedures.
Employee Training
- Fire Safety Training: Provide comprehensive fire safety training to all employees, covering fire prevention, emergency procedures, and fire extinguishers. Ensure that employees understand their roles and responsibilities during a fire emergency.
- Fire Drill Participation: Conduct fire drills regularly to test the effectiveness of fire safety measures and ensure that employees are prepared to respond effectively in an emergency.
13. Hazard Communication and Chemical Safety
Hazard communication and chemical safety are vital for managing the risks associated with hazardous substances in the workplace.
Effective hazard communication involves informing employees about the chemicals they may encounter, including their properties, risks, and safe handling procedures.
Hazard Communication
- Understanding Hazards: Hazard communication involves informing employees about the chemical hazards they may encounter in the workplace. This includes understanding the properties, risks, and safe handling procedures for chemicals.
- Labeling and Signage: Ensure all chemical containers contain information about their contents, hazards, and handling instructions. Use appropriate signage to indicate the presence of hazardous materials and to provide safety information.
- Safety Data Sheets (SDSss): Maintain and provide access to Safety Data Sheets (SDSs) for all chemicals used in the workplace. SDSs provide detailed information on chemical properties, health effects, and emergency procedures.
Chemical Safety
- Proper Handling: Follow established procedures for safely handling, storing, and disposing of chemicals. Use personal protective equipment (PPE) as required to protect against exposure to hazardous substances.
- Emergency Procedures: Develop and communicate procedures for chemical spills, leaks, or exposures. Ensure employees know how to respond to chemical emergencies and where to find the necessary equipment and materials.
14. Incident Reporting and Investigation
Incident reporting and investigation are essential components of a comprehensive workplace safety program.
Reporting incidents such as accidents, near misses, or unsafe conditions allows organizations to address hazards promptly and prevent future occurrences.
Thorough investigations, supported by proper incident investigation training, help identify the root causes of incidents and lead to the development of corrective actions.
Incident Reporting
- Importance of Reporting: Promptly reporting incidents, such as accidents, near misses, and unsafe conditions, is essential for addressing hazards and preventing future occurrences. Reporting helps to identify trends and areas for improvement.
- Reporting Procedures: Establish clear procedures for reporting incidents, including how to document and communicate information. Ensure employees understand how and when to report incidents and encourage a culture of openness and transparency.
Incident Investigation
- Purpose of Investigation: Investigating incidents helps to determine the root causes of accidents or near misses and to identify corrective actions to prevent recurrence. Effective investigations can improve safety practices and reduce the risk of future incidents.
- Investigation Process: Conduct thorough investigations by gathering evidence, interviewing witnesses, and analyzing contributing factors. Use this information to develop and implement corrective actions, such as changes in procedures or equipment.
- Documentation and Follow-Up: Document all findings from the investigation and track the implementation of corrective actions. Regularly review and update safety procedures based on investigation outcomes to ensure continuous improvement.
15. Technology and Automation for Safety

Technology and automation have revolutionized safety practices across various industries by introducing advanced tools and systems that enhance workplace safety, efficiency, and risk management.
These innovations help proactively identify potential hazards, reduce human error, and ensure compliance with safety regulations.
Here's a detailed look at how technology and automation contribute to workplace safety.
Automated Safety Systems
Automated safety systems include automatic shut-off systems, collision avoidance sensors, and robotic process automation. These systems are designed to detect potential hazards and take corrective actions without human intervention.
For example, automated shut-off systems can immediately halt machinery if a malfunction is detected, preventing accidents and minimizing damage.
Collision avoidance sensors, often used in vehicles and heavy equipment, help prevent accidents by alerting operators to obstacles and automatic braking when necessary.
Real-Time Monitoring and Alerts
Real-time monitoring systems use sensors and data analytics to continuously track conditions and performance. They can monitor temperature, pressure, and equipment status.
When anomalies or unsafe conditions are detected, the system triggers immediate alerts to notify operators and safety personnel.
For instance, in a warehouse, real-time monitoring can detect if a temperature exceeds safe limits in a storage area, prompting swift action to prevent spoilage or fire hazards.
Wearable Technology
Wearable technology, including intelligent helmets, vests, and wristbands, is increasingly used to enhance worker safety. These devices can monitor vital signs, detect falls, and even track worker location within a facility.
Wearables can provide alerts in case of abnormal conditions, such as elevated heart rates or hazardous gas exposure, ensuring timely intervention.
Additionally, data collected from wearables can be analyzed to identify patterns and improve safety protocols.
Data Analytics and Predictive Maintenance
Data analytics and predictive maintenance use historical data and machine learning algorithms to predict equipment failures and safety incidents before they occur.
Organizations can proactively schedule maintenance by analyzing patterns and trends, reducing the risk of equipment breakdowns and accidents.
For example, predictive maintenance can identify when a piece of machinery will likely fail, allowing for repairs during scheduled downtime rather than in response to an emergency.
Automated Safety Compliance
Compliance with safety regulations is crucial for maintaining a safe work environment. Automated systems can help ensure compliance by tracking and recording safety checks, inspections, and training.
For instance, automated compliance management systems can generate reports, track safety training completion, and ensure that all necessary safety procedures are followed.
This reduces the likelihood of human error and helps organizations meet regulatory requirements more efficiently.
Enhanced Communication and Coordination
Technology facilitates better team communication and coordination, especially in complex or high-risk environments.
Digital communication tools, video conferencing, and real-time collaboration platforms enable instant information sharing and coordination during emergencies.
This enhances the effectiveness of emergency response and ensures that all team members are informed and aligned on safety protocols.
Virtual Reality (VR) and Augmented Reality (AR) for Training
VR and AR technologies offer immersive training experiences that simulate real-world scenarios without exposing workers to risks.
These technologies can be used for safety training, allowing employees to practice responding to emergencies, operating machinery, and dealing with hazardous environments in a controlled setting.
VR and AR training can improve skills and preparedness, reducing the likelihood of accidents and injuries.
Warehouse Safety Tips for the Workplace - FAQs
How often should employees undergo warehouse safety training?
Employees should undergo warehouse safety training regularly, ideally at least annually, or when significant changes to work processes, equipment, or safety protocols occur.
What role does personal protective equipment (PPE) play in warehouse safety?
Personal Protective Equipment (PPE) plays a crucial role in warehouse safety by providing a barrier between workers and potential hazards, reducing the risk of injuries, and ensuring their well-being.
How can I prevent slips, trips, and falls in a warehouse environment?
To prevent slips, trips, and falls in a warehouse environment, ensure proper housekeeping, promptly clean up spills, use non-slip flooring, and provide proper footwear for employees.
What steps should be taken to ensure the safe operation of forklifts and other machinery?
To ensure the safe operation of forklifts and other machinery, train operators properly, perform regular maintenance, establish designated traffic lanes, and enforce speed limits within the warehouse.
Final Words
The significance of warehouse safety cannot be understated, as it is essential for preventing accidents, protecting valuable inventory, and preserving a positive work culture.
By implementing the outlined warehouse safety tips for the workplace, employees can get the unlimited benefit of online training sessions and create a safer environment.
Warehouse safety can become the priority through an effective approach, including training, proper equipment usage, maintenance, vigilance, and following common safety engagement ideas.
The awareness of potential hazards and the application of recommended safety tips empower each worker to contribute to a safer work environment. With continuous dedication to these safety tips, we can ensure that warehouses can become safer workplaces for the employees!